How Robotic Palletizing Works
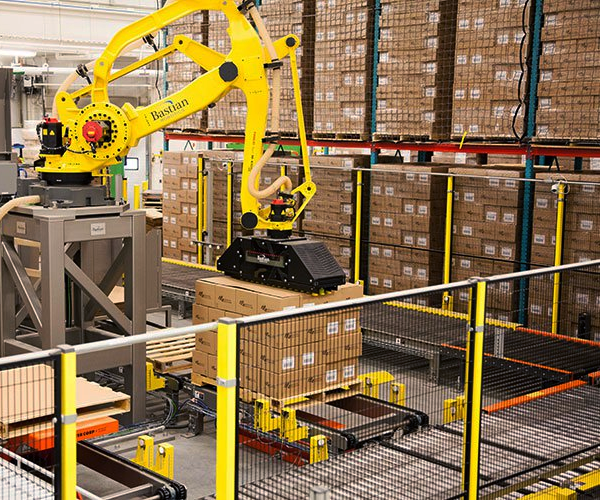
Products to be palletized are fed into the robotic cell via the infeed conveyor system. A pallet is deposited into the pallet loading area either by an automated pallet dispenser or by the palletizing robot. The robot picks one or multiple products at a time, then quickly and accurately places them on a pallet.
The pattern is constructed layer by layer, utilizing slip or tier sheets if needed. Once the load is complete, the pallet is removed from the robotic cell via the outfeed conveyor for stretch wrapping or other downstream processing. The palletizing robot repeats the process with a new pallet.
Bastian Solutions StackOrder™, our standard palletizing system, allows customers to visualize, edit and implement various pallet patterns in real time. This standard palletizing system combines industrial or collaborative robots, dynamic pallet pattern software, custom end of arm tooling and seamless integration to improve palletizing operations. This advancement in fully automated palletization delivers high uptime, fast ROI and operational flexibility.
Dynamic EoATs (end of arm tools) expand the robot’s capabilities beyond just stacking products, allowing it to also handle pallets, slip sheets and tier sheets, fully automating the palletizing process without adding additional equipment. Custom EoATs can also be designed for difficult-to-handle, delicate, or hazardous products such as bags, batteries and scrap metal bales.
Mixed Product Handling
Mixed load palletizing is the stacking of multiple products on a pallet to maximize pallet density, allowing for diverse, demand-driven pallets ideal for ecommerce and distribution operations. These loads, sometimes referred to as a “rainbow pallet,” can be comprised of homogenous layers of any single product, or mixed product within a layer.
For effective mixed-load pallet building, StackOrder™ controls where products are positioned on the pallet based on product characteristics - large and heavy items are placed on the bottom while small, lightweight items are placed towards the top. For beverage operations, integrating robotic palletizing alongside our automated case flow system increases the throughput speed of mixed case pallet building to 2,500-4,000 cases per hour.
Artificial Intelligence and Vision System
For effective mixed-load pallet loading, advanced machine vision and artificial intelligence aid the robot in accurately and safely picking and placing product. Equipped with this cutting-edge technology, Bastian Solutions’ palletizing robots don’t require training or programming to handle your current products or new product integration.
As new products are introduced, the AI software builds a library of objects it has seen and handled over time, along with optimal picking information. This is shared across the entire fleet allowing them to continuously learn from each other so they can function as a single, highly efficient depalletizing operation.
The AI and vision platform directly interfaces with Bastian Solutions’ Exacta® software, communicating product data and sharing outbound product information. This integration allows the cells to run with even higher autonomy.