Your Complete Guide to Robotic Case Packing Systems
Steven Hogg | 23 July 2015
Robot-based automation ensures the kind of flexibility needed to meet shorter product life cycles, new packaging designs, product variants and batch manufacturing. Compared to dedicated hard automation, robot lines are shorter and allow for better utilization of floor space.
Robot-based automation is also an excellent alternative to manual operation. In addition to increased up-time and total throughput, fewer accidents and increasingly demanding workplace ergonomics are compelling reasons to make the shift to robotics.
Robots are usually associated with handling repetitive tasks in a process – either in high volume production roles, or where flexible handling systems are needed for frequent changes. In the packaging industry, robots generally fall into two main areas: pick and place applications (where products are packed into trays or secondary packages) and feed placement (where products are prearranged on a conveyor to ease future packaging procedures, i.e. placing product into shrink tunnel infeed, etc.).
For case packing projects, generally all packages fall into three types: Rigid, semi-rigid, and flexible.
- Rigid packages have a known shape and size. Because of these characteristics, rigid packages lend themselves most commonly to static picking applications. They have known product features that can be controlled and staged for robot interaction. If known orientation cannot be obtained, they can easily be identified by a vision system based on their consistent vision targets.
- Semi-Rigid packages have a general shape and size but can vary based on product composition. Because of this variability, the packages can become difficult to manipulate into a static position and may require a vision system for identification. Detailed analysis is required on the package tolerances to determine if the package can be presented to the robot in a repeatable pick position.
- Flexible packages are the hardest to lane and stage for static picking. Because of the fluid nature of the packaging and product, most require a vision system for identification. In this scenario, the vision system is trying to identify a center point of the package that the robot will consider the base pick point. When the exact orientation of the package cannot be obtained, the case dimensions must have enough clearance to allow for the potential skewed package orientation.
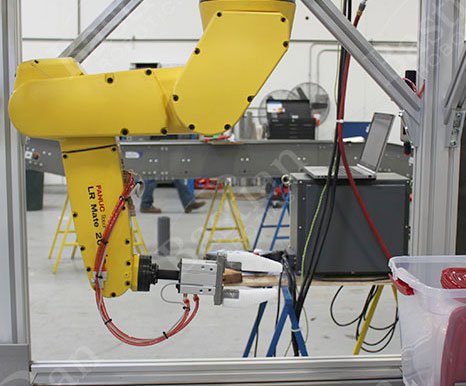
In robotic case packing systems, the system throughput requirements must be properly addressed within each sub-system of the case packing system. It is important that all sub-systems be capable of feeding the downstream sub-system at required rates and product orientation.
The core components of a robotic case packing system include:
- Robot:
- Delta, 4-axis, and 6-axis models are available based on rate, reach, and payload requirementsRobot Stand: A custom designed stand will ensure the proper mounting location for the selected robot to optimize the speed, reach, and throughput. Floor, side, or overhead mounting orientations are possible. The operating environment layout and space constraints typically dictate the mounting orientation.
- End of Arm Tool (EoAT):
- Vacuum and Mechanical grippers are the two most common applications. Needle for bakery, or a custom designed EoAT can be utilized for unique product handling applications.
- Product Conveyor:
- This conveyor brings product from the production lines to the robotic case packing system. Conveyor speed, product spacing, and production orientation will be dictated by the requirements of the robot. When a vision system is utilized a high contrast belt should be used for product orientation identification.
- Case Conveyor:
- This conveyor transports cases through the cell for robot interaction, and is typically outfitted with adjustable case guides for product changeovers. Case stops and metering devices may be required for starting and stopping the cases in a known location. In applications where the case is required to move during case packing, a belt should be utilized and cases tracked via an encoder. Special attention should be paid to the case flaps. If interference is possible with the product or EoAT, additional mechanisms will be required to contain the case flaps.
- Vision System:
- When product orientation is unknown, a vision system is required. For optimal cycle rate, the vision system should be mounted upstream of the robot cell in a static position. Depending on the environment, a vision enclosure may be necessary to ensure the hardware is protected from damage. The vision system can also be integrated into the robot EoAT but it will greatly reduce the robot speed capabilities.
- Pneumatics:
- Vacuum tools are typically powered by one of two methods: venturi generators or vacuum pumps. Depending on the environmental requirements, a separate enclosure may be necessary to house components.
- Safety Guarding:
- A risk assessment should be completed to determine the safety requirements of the system. Lexan safety fence is standard to increase visibility into the robotic case packing cell.
- System Control Panel:
- Contains all controls for equipment external to the robot. For wash-down environments, a NEMA 4X panel should be utilized.
- Robot Control Panel:
- The robot control panel should be located within close proximity of the robot cell in order to utilize standard length cabling. For wash-down environments, the robot control panel should be located in a separate NEMA 4X panel.
- Human Machine Interface (HMI):
- HMIs are typically mounted in the system control panel. If the control panel cannot be located within line of site of the cell, a remote HMI can be mounted local to the system.
- Optional Manual Pack Area:
- This area handles all bypass of product through the robotic case packing system. This is normally located near the outfeed of the cell so that cases can be metered to the packing station.
Basic Vision Guided Robotic Case Packing System Arrangements
Basic Static Position Robotic Case Packing System Arrangements
Steven is the Applications Manager for Robotics at Bastian Solutions. He helps lead the robotics automation solutions for picking, packing, palletizing, machine tending, turnkey options and more. He has a Bachelor of Science in Industrial and Manufacturing Systems Engineering from the University of Missouri-Columbia.
Comments
No comments have been posted to this Blog Post
Leave a Reply
Your email address will not be published.
Comment
Thank you for your comment.