What’s right for you? PLC or Safety PLC?
Vijay Kapila | 08 January 2014
Do you need a PLC (programmable logic controller) or a safety PLC? The answer depends on the safety requirement of the system or equipment in question. There are PLCs and there are safety PLCs which have safety built into them. So what's the difference, and what should you be using for your automated system when there is a stringent safety requirement? Each automated system or piece of equipment has an individual safety requirement based on the category of the safety circuit, and there are four different categories for safety circuits:
- Category 1: Single channel to safety relay, the lowest category of safety circuits.
- Category 2: Two channels for a safety circuit; the first channel is hardwired to an e-stop chain, the second channel can be another hardwire or PLC monitoring of auxiliary contacts on safety switches.
- Category 3: Two hardwired channels for a safety circuit; drives with a “safe off” feature generally fall under this category.
- Category 4: Two hardwired channels for a safety circuit with a self-monitoring safety relay. This is the most stringent of categories and the one most of the automotive industry follows.
PLCs can be programmed to do just about anything these days, from simple discrete logic, to a complex hybrid control. But why not take it a step further and use the PLC to detect and respond to potentially dangerous failures? This keeps safety top of mind and helps to get the system safety certified. It can definitely be DONE, and it can be accomplished in two ways:
1. Using a Normal PLC for a Safety Circuit
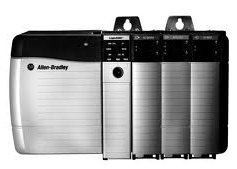
A controls system can be designed with a normal PLC and can be programmed however we want. A system can also be designed and programmed with any level of complexity with a PLC such that it can detect any kind of failure and put the equipment in a stopped, safe and controlled manner. To achieve a certain safety category with a normal PLC, all the equipment needs to be hard-wired as explained in the above categories for that equipment’s specific safety-circuit category. Pros of using a normal PLC:
- Simple to wire and troubleshoot
- Cost effective for simple systems
Cons of using a normal PLC:
- Many different relay types
- Problems increase with an increase in relays and can quickly get complicated
- Poor diagnostics and poor status indicators
- Very difficult to do multiple e-stop zones
2. Using a Safety PLC
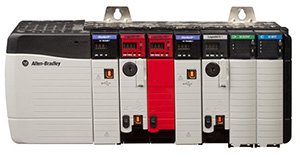
Now, on the other hand, a safety PLC is different in that it was purposely built, tested and certified to meet international safety requirements right off the shelf. A safety PLC is different from a conventional PLC in many ways, such as:
- Redundancy of onboard devices which are continuously monitored by a watchdog circuit
- Continuously monitors inputs with a smart circuit to detect failure or malfunction
- Additional safety circuitry between the output switching device and an actual device, which will detect system failure and facilitate a safe shut down by reverting to a known state
Pros of using a safety PLC:
- Major savings on field wiring (Safety Circuit Category 3-4)
- Flexible
- Scalable
- Remote I/O capability with safety
- Safety control and standard control in one unit
- Good diagnostic capability
- Perfect for multiple e-stop zone applications
Cons of using a safety PLC:
- Upfront cost is higher
- Requires programming
- Possibly too complex for certain applications
- Requires educated maintenance people
To summarize, safety relays with a normal PLC are not recommended for applications requiring 5 relays or 2 e-stop zones. A safety PLC can be very cost effective when packaged in one unit with its ability to increase production and its allowance for scalable solutions. Carefully examine the pros and cons of each option when designing your controls system to get the best results on every project.
Comments
Knowledge Sourcing says:
10/21/2020 07:22 AM
Hi, such a nice article when i am searching about the safety switches market. I reached on your website you have such a nice and helpful content.
Scott A. Somers says:
8/28/2018 10:09 AM
Mr. Kapila,
Thank you for this article, very informative and timely for me.
loganathan.M says:
8/28/2018 10:09 AM
good evening sir, i m a robotics and automation engineering student. i studied PLC and SCADA your article is very useful to me. and i m familiar with SIEMENS PLC SOFTWARE. If u read this comment please sir reply me....
Leave a Reply
Your email address will not be published.
Comment
Thank you for your comment.