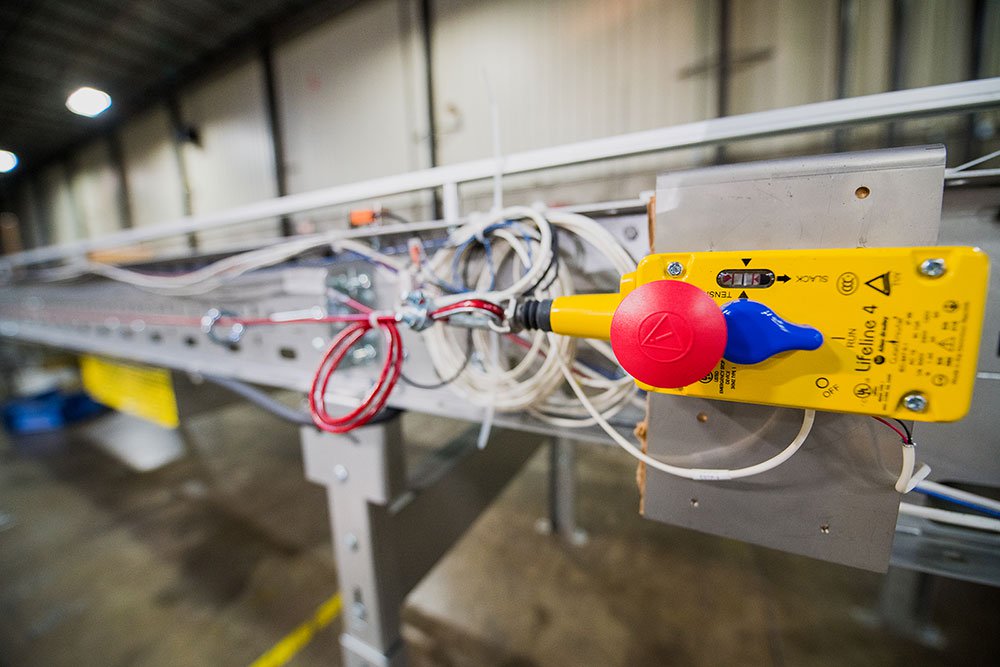
Understanding the Difference Between Safety Devices in Material Handling Automation Systems
Josh Reed | 13 September 2023
In today's rapidly evolving technological landscape, automation has become an integral part of various industries, ranging from manufacturing and logistics to healthcare and transportation.
With warehouse and distribution center material handling automation's widespread adoption, ensuring the safety of workers, equipment and the public is of paramount importance. To achieve this, various safety devices are employed to minimize risks and prevent accidents.
Common Safety Devices in Material Handling Automation Systems
There are numerous safety devices, equipment and processes that can be followed to help foster a safe work environment. However, in this article, we will explore the differences between some of the most commonly used safety devices in automation.
Emergency Stops
Emergency Stops (e-stops) are easily identifiable and prominently placed on machinery to enable immediate shutdown in case of an emergency. When pressed, they instantly control power to the machine, bringing it to a safe and controlled stop. E-stops are designed to be user-friendly, enabling any individual to act quickly in case of a hazardous situation.
These buttons are often color-coded with a red-mushroom shaped head for easy identification. Another e-stop commonly used when trying to stretch over a specified length versus a standalone location is an e-stop pull cord.
Safety Interlock Switches
Safety interlock switches are critical components in automated systems, designed to prevent unintended access or operation. These switches act as physical barriers or locks that must be engaged to allow the system to function. Common types of safety interlock switches include: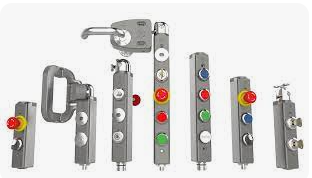
- Tongue Interlock Switch: This switch requires the insertion of a tongue or actuator to lock or unlock the safety guard. When the interlocked guard is open, the automation process is halted, ensuring that workers cannot access hazardous areas during operation.
- Keyed Interlock Switch: Similar to a tongue interlock switch, this device uses a unique key to lock and unlock the safety guard. The machine remains inoperable until the guard is properly closed and secured, and the key reinserted.
Safety Laser Scanners
Safety laser scanners are similar to safety light curtains in that they create protective fields to monitor hazardous zones. However, instead of using infrared beams, safety laser scanners utilize laser beams to scan the area continuously. These scanners can detect not only the intrusion but also the speed and direction of the moving object.
Safety laser scanners are particularly useful in applications where the shape and size of the hazardous area may vary, as they allow for flexible and adaptable safety zones. Additionally, they can be integrated into mobile machinery such as AGV/AMR (automated guided vehicles/autonomous mobile robots) and transfer cars.
Safety Light Curtains
Safety light curtains offer a non-contact solution for safeguarding personnel
around hazardous machinery. Comprising of infrared transmitter and receiver units, light curtains create an invisible sensing field. When this field is interrupted, the automation system stops to prevent any potential harm. Key features of safety light curtains include:
Resolution and Detection Capability: Safety light curtains are available in various resolutions, determining the size of the beams and their sensitivity. Higher resolutions offer finer protection, reducing the risk of bypassing the curtain.
Safety Switches vs. Scanners vs. Curtains
Safety devices in automation play a crucial role in safeguarding workers and preventing accidents. While safety interlock switches provide a physical barrier to access hazardous areas, safety light curtains offer a contactless approach with various resolutions and blanking options. On the other hand, safety laser scanners utilize laser technology to monitor dynamic areas effectively.
Promoting a Safe Work Environment
The choice of safety devices depends on the specific needs of the automated system, considering the level of risk, the nature of hazards, and the workflow. Eliminating hazardous energy through the use of established lockout procedures is necessary before performing service and maintenance activities on automated equipment, but employing the right safety devices ensures a harmonious integration of automation and safety, fostering a safe work environment for everyone involved. An experienced material handling systems integrator will help factor in the above considerations and work with suppliers and your specific operation needs.
Josh is a Field Application Engineer based in Toledo, OH. He received his degree in Electrical Engineering from The University of Toledo. Prior to sales he worked as an Electrical/ Controls Engineer where he implemented many small and large material handling solutions. Working as a solutions integrator this assisted him in gaining his 10 years of knowledge in electrical troubleshooting, programming and system design.
Comments
No comments have been posted to this Blog Post
Leave a Reply
Your email address will not be published.
Comment
Thank you for your comment.