Tips on Integrating Pallet Flow Rack in a Freezer
Greg Conner | 23 January 2019
Don't get stuck out in the cold
The name of the game in freezer and cooler storage applications is maximizing storage density. With operating expenses sometimes being as much as 10x the cost of ambient warehousing, it’s easily understood why cold storage companies are continuing to seek out solutions that utilize as much of their facilities as possible. A common solution many turn to is pallet flow systems, as they can increase storage density by as much as 60% over conventional selective pallet racking or floor storage solutions.
However, you need to be very careful when designing and implementing pallet flow systems in such an unforgiving environment.
The Harsh Environment of Cold Storage
Many cold storage warehouses store products at temperatures as low as -20 degrees Fahrenheit. Such a frigid environment will take a tremendous toll on equipment and must be taken into consideration. For example, many lubricants will lock-up at such low temperatures. In addition, plastics and rubber materials will crack and be very susceptible to premature wear.
Standard pallet flow components will not hold up to the rigors of cold storage. Time and time again, our team has seen the results of improper pallet flow equipment installed in cold storage environments by other companies. Most often, what we find is broken pallet flow wheels, locked up bearings and stuck pallets. Not only are these situations expensive to fix, but they also create extremely dangerous situations when operators are forced to retrieve pallets that become stuck in the system. 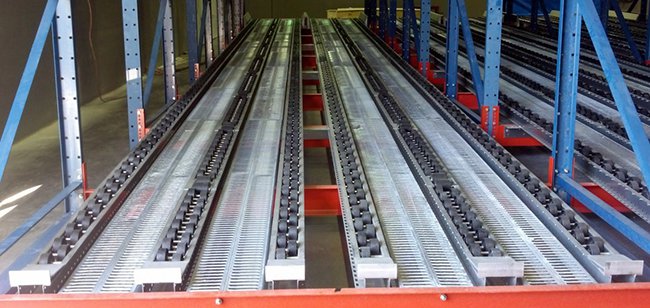
Cold Storage Considerations
So, what should you focus on to ensure your pallet flow system will work flawlessly in a cold storage warehouse? Below are a few things to consider.
1. Use quality pallets– Wooden GMA-style, CHEP and PECO are built to perform and flow consistently in tough freezer environments. Selecting a well-built and reliable pallet is vital, but you should also regularly inspect your pallets to ensure they are not damaged or have broken bottom boards that could get stuck in the pallet flow system.
2. Select the right wheel – Typical pallet flow wheels are manufactured with a standard polycarbonate which becomes brittle and fatigues in the brutal cold, ultimately chipping, cracking and breaking. This obviously leads to ongoing hang-ups, downtime and hefty wheel or lane replacement costs. The only pallet flow wheel we have found that holds up in the harshest freezer environments is Mallard Manufacturing’s Magnum Wheel. Mallard is also the only manufacturer we have found that will offer a lifetime warranty, further demonstrating how confident they are in their product.
3. Use the right speed controller – One of the biggest advantages of a pallet flow system is the number of pallets that can be stored in one lane. It is not uncommon for these systems to store as many as 15 pallets per lane. Obviously, the more pallets stored in each lane, the more backpressure will be present. In addition, when a lane is empty, the first few pallets that are loaded will have an opportunity to flow at a tremendous amount of speed. To slow and separate the pallets, a speed controller should be used – and it must be rated for use in cold storage.
4. Test your application – One of the biggest mistakes we find is that customers don’t setup a test prior to ordering their pallet flow system. Bastian Solutions will work with you to set up a test at our facility. This will help ensure that the system is configured with the appropriate slope for your specific product. Configuring a pallet flow system with the wrong slope and position of speed controllers can be extremely costly, and we work very hard to avoid this.
Is your existing pallet flow system showing signs of failure? We can help.
Bastian Solutions has a tremendous amount of experience correcting pallet flow systems that have been incorrectly specified and installed by others. In many applications, we can work with your team to strategically replace failed components, saving you time and money. Contact us today to learn more about how we can improve your cold storage operations.
Greg is the SVP of Corporate Development and Marketing at Bastian Solutions. A proud Purdue University graduate, at Bastian he works to identify and drive strategies to propel the company forward. His responsibilities include identification of emerging technologies, forming strategic partnerships and M&A activities and execution of the strategic planning process. He carries with him years of experience in the field, having previously worked as a project engineer, field application engineer and regional director of Indiana.
Comments
No comments have been posted to this Blog Post
Leave a Reply
Your email address will not be published.
Comment
Thank you for your comment.