Tips for Selecting the Right Tire Handling Equipment
Roger Wilke | 19 November 2014
The tire manufacturing industry continues to push for automation of tire handling, resulting in reduced labor costs and improved quality. The automation of this process includes a variety of conveyors and material handling situations. We will highlight several of these key processes and the equipment used to properly convey and store tires.
Green Tire (GT) vs. Finished Tire (FT) - The first critical consideration for conveying or storing tires in a manufacturing plant is the two basic forms of processed tires.
- “Green” tires are the output from the tire building process, where the tire components are assembled onto a tire building drum. The green tire material is soft, pliable, and susceptible to damage.
- “Finished” tires are the products of the curing process, where the tread pattern has been pressed into the tire and the material is vulcanized. After curing is complete, the tire looks like any tire you would see going down the road.
General Considerations for Handling Tires:
Both Green and Finished Tires
- Friction is very high, so it is not easy to push tires across conveyors (either along the direction of flow or side to side).
- Orientation is not usually a factor, except when scanning bar coded tires.
- Sharp edges cause problems. Watch for exposed bolts, angles, and conveyor-to-conveyor connection points.
- Conveyor frames – “Waterfall” the conveyors on 90-degree square turns to avoid tires getting stuck on conveyor frames.
- Tire size – Passenger tires and truck tires vary greatly in size, so technology used for passenger tires (e.g. O-ring rollers, kickers) may not be applicable for larger products.
Green Tires

- Should never touch each other
- “Saucer” shape is a factor
- GTs can flip backwards on inclines.
- Can “collapse” while conveyed or stored (as shown above)
- The GTs can be flipped over prior to picking it up with an end of arm tool.
- Must consider where the leading edge of the tire is and place photo-eyes high enough to capture that leading edge, whether the tire is collapsed or not.
- Need to support the shape of the tires when storing.
- Should not let green tires dwell on roller conveyors. They will leave indentations.
- Keep speeds of adjoining conveyors or zones the same to avoid abrasion on the GTs.
Finished Tires
- Usually a higher volume, warm and possibly dirty environment
- Conveyor speeds in the 35-65 meter per minute range
- Can allow tires to touch (but no more than 4-5 tires due to back pressure)
- Round shape can be helpful around corners
- Round shape can also result in side by side (and jammed) tires if conveyor width is not correct
Types of Conveyors Used for Tire Handling:
Although the following list isn't exhaustive, these are some of the most common conveyors used when handling tires.
- Modular plastic belts – Have gained popularity for their durability, good tracking and ease of maintenance, as well as “special belts” for diverts, merges, inclines, etc.
- Textile belts – Lower initial cost solution than modular belts
- Live roller conveyors – Good for transport and curves
- Gravity conveyors – economical, good for accumulation when combined with brakes
- Motor Driven Rollers (DC) vs. AC Motors – subject for another blog, but MDR driven conveyors have become much more popular in this industry.
Specific Tire Handling Situations:

Diverting tires – when a tire needs to be discharged onto another conveyor. This can happen thousands of times per day, so the durability of the equipment should be considered:
- Kickers vs. Plows – A plow is held in place while the tire changes direction. A kicker or “slap diverter” hits the tire to knock it in a different direction. With either method, you need rollers under the tire flowing with its new direction such as Transverse Roller Top (TRT) belt.
- Kicker/Slap Diverter:
- Need to justify the tire to the kicker side; helps transfer energy properly to move the tire
- Timing of kick – watch for various size tires
- Good for diverting individual tires at high volume
- Plows:
- Tire “justification” to one side is not needed
- Good for diverting groups of tires that are back to back
- Need open accumulation space downstream of the plow to divert multiple tires
- Activated Roller Belts – are gaining popularity because of speeds and ability to redirect tires without touching them.
Feeding tires onto a perpendicular line:
- Use bump rollers at 90 degree turns for FTs.

- Feed onto a TRT belt (high volume), or a transfer (low volume)
- Try to match speeds of the infeed and discharge conveyors, and use the infeed conveyor to “throw” the tire out onto the perpendicular line for a smooth transition around the corner.
Inclines/Declines:
- Don’t exceed 30 degree angles on inclines/declines to avoid flipping tires
Can be creative – you don’t always need noseovers or feeder belts. (E.g. use elevation changes for infeed conveyor or discharge to get a good transition. At the infeed of an incline, “overlap” the upstream conveyor to let the tire gently fall onto the incline.)
Vertical switching:
- 2-1 and 3-1 switches are useful for changing conveyor levels for tires at higher volume
- Lifts with powered rollers are good for tight areas, lower volumes
- Gravity rollers can be used to flip tires over between levels
Accumulating tires:
- 4-5 tires max on gravity declines – back pressure is significant, use roller brakes to separate groups of tires (about every 5-7 meters). A combination photo-eye/solenoid for the air brakes works well
- 24V conveyors with zero pressure logic are also a good solution
Separation of tires:
- Double pin stop, use reciprocating stops - lower volume
- Indexing belt (slaved section) and brake motor - higher volume
Centering:
- Used to help keep tires off side rails or centered for specific tire operations
- TRT belts combined with linked centering arms work well
Gravity conveyor:
- Back pressure can be a significant issue
- 1.9” rollers are okay for passenger tires, usually need 2.5” rollers for truck tires
- Typically, 3-4” roller centers on passenger tires, 4-6” roller centers on truck tires
- Watch for areas where tires get dropped onto conveyor; you may need heavier rollers or reinforcement
Side rails:
- Use skatewheel or “vertical” rollers; if skatewheel rails are used, the height needs to be lower than the shortest tire.
Combinations of these situations allow systems to be properly assembled for various tire manufacturing processes:
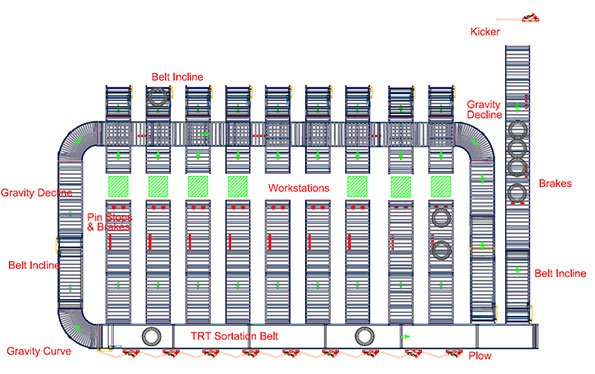
There are many new technologies that apply to handling tires including special conveyor belts, 24V rollers, AGVs, automated storage and retrieval systems and more. As long as the unique qualities of green and finished tires are considered in the application, there are many combinations of equipment that can properly handle tires during the manufacturing process.
Carefully review your operation and goals to determine the best solution for your tire handling facility. Contact us to learn more.
Comments
No comments have been posted to this Blog Post
Leave a Reply
Your email address will not be published.
Comment
Thank you for your comment.