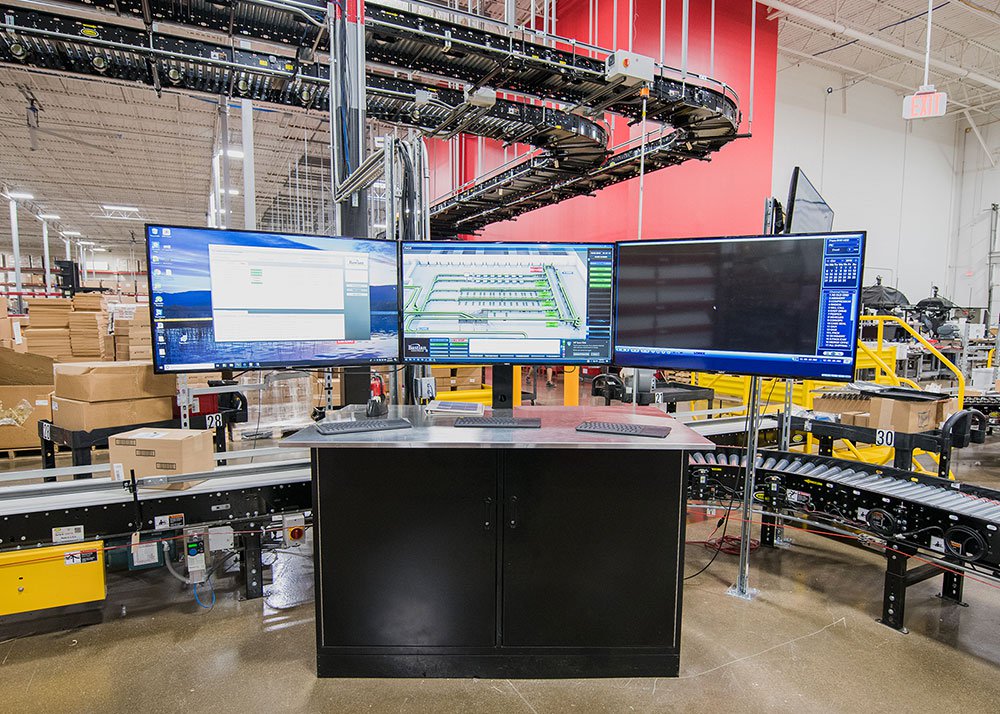
The Value of WES Software in a Modern Warehouse
John Young | 2 February 2022
In a modern warehouse, there are many systems that need to communicate with each other for operations to run smoothly. This is especially true for distribution centers that use any degree of automation.
In these cases, either the host ERP (Enterprise Resource Planning) system or the WMS (Warehouse Management System) controls inventory and is the brain of the entire warehouse. The WES (Warehouse Execution System), on the other hand, is responsible for controlling the various islands of automation to complete tasks given by the host or WMS system.
This might all seem a bit complicated at first. After all, if the WMS is like a brain, why can’t it just control everything in the warehouse on its own? Are multiple systems really better and more cost-effective than one? As I will explain below, a WES can greatly improve operations where automation is involved in many ways.
WES for Improved Automation Operations
Flexibility
An agnostic WES can easily integrate with technologies from goods-to-person systems to carton erectors to shipping sorters and can work with any automation manufacturer under the sun. This flexibility gives the operations team the opportunity to run the warehouse exactly how they want, with no limitations based on WMS functionality. The ability to get creative with your operations is key in designing an efficient warehouse, and a WES provides this freedom.
A WES also provides flexibility when expanding the functionality of an existing warehouse due to its modularity. Adding new automation systems to an existing operation can be as quick as adding a standard module, and expansion options are growing rapidly as new products are developed.
Communication
Communicating between many systems can be difficult. If a WMS has to send messages to a goods-to-person system and a conveyor sortation system, both of which are from manufacturers the WMS has never interfaced with, there will likely be many bugs that come up that can result in delayed go-live or affect operations. In contrast, with a WES, there is a single interface layer with a single protocol for the WMS to follow. This decreases the number of communication errors and allows for greater focus on the actual operations.
Quality
The primary purpose of a WES is to connect automation equipment with other warehouse processes. Naturally, a fully connected system translates into a higher quality system. The benefits of a WES don’t end with the software itself though, operations can also benefit from the WES provider itself. Working with an independent integrator allows customers to benefit from their experience and knowledge working with various projects, designs and technologies to effectively integrate a WES no matter the project. They’re able to leverage past learnings to develop a high-quality system both from a software and automation technology aspect. A software-only WMS provider, on the other hand, may not have the exhaustive knowledge or familiarity with a broad array of automation equipment to control the various islands of automation to complete tasks.
Business Relationships
WES teams often work directly with automation manufacturers, and therefore have fostered solid relationships with those companies. These relationships often lead to faster service, lower prices, and better communication.
Ready to Find Your Solution
Bastian Solutions has been fortunate enough to partner with great companies, small and large, to implement software and automated solutions that help increase productivity, streamline operations, and create a happier workplace in the order fulfillment world. If you have questions or want to know more in detail what our software suite can do for you, contact us.
John is a Logistics Consultant at Bastian Solutions’ software division based in Louisville, Kentucky. He received his B.S. in Mechanical Engineering and M.S. in Business Administration from the University of Kentucky. John works to design software for highly automated systems including those with goods-to-person technology, conveyor routing, sortation, and more.
Comments
No comments have been posted to this Blog Post
Leave a Reply
Your email address will not be published.
Comment
Thank you for your comment.