The Importance of Understanding Your Pallet for Proper Conveyance
Mike Kedvesh | 05 February 2013
I spend much of my time in manufacturing facilities, dealing with material handling issues related to moving and positioning pallets, plastic bulk box containers, steel racks, and multi-footed thermoformed pallets. Often times, we are given very little information on the pallet / container / rack we are asked to design around, let alone the details of the bottom surface. Let’s touch on the different types of pallet / container / rack bottoms that we commonly come across:
1. Wood GMA Pallets
These are typically 40” x 48” or 45” x 48” and generally have 3 to 5 bottom boards running the narrow dimension of the pallet. These bottom boards can range in width from approximately 2-3/4” wide to 5” wide. It is ideal to convey these with the bottom boards running perpendicular to the rollers. This allows the rollers to be spaced further apart and still allow for good conveyance. However, if for product orientation reasons, the pallet must be conveyed with the bottom boards running parallel to the direction of flow, then rollers spaced very closely or multiple strands of roller chain or flat running chain are typically used.
2. Bulk Box Plastic Containers 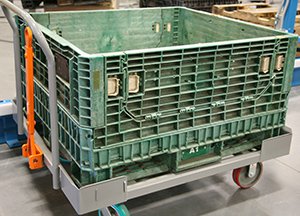
These tend to have bottoms that are a bigger challenge to convey. Some of these containers can have distinct “rails”, much like the bottom boards of a conventional wood pallet. Some, however, can have ribbed or even “honeycomb” bottoms which make conveyance rather difficult. These types of bottoms tend to require rollers on close centers, multiple strands of chain, or a wide belted surface. We often get asked to convey these on ball transfers, and this typically will not work as the ball casters will get “stuck” in the voids of the bottom details of these types of containers.
3. Steel Racks
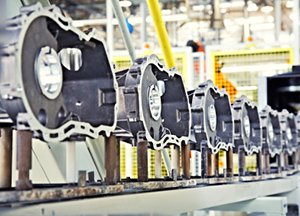
Steel racks come in a variety of shapes and sizes, and the bottoms can have an equally diverse range of offerings to complicate conveyance. Some racks have 2 steel runners, each being made of a structural steel member. These are actually the easiest and most forgiving to convey, provided that the steel runners are positioned correctly with respect to product flow.
However, some racks have “picture frame” bottoms, which can consist of steel tubing or flat bar. These steel “picture frame” style bottoms work best with either roller chain or with multiple lanes of narrow rollers on very close centers. Sometimes, these racks can also convey on powered rollers slightly wider than the product, provided they are on extremely close centers and very heavy gauge wall with high capacity bearings.
One other consideration of steel racks is the abuse and damage they can wreak on conveying systems. In particular with wider roller conveyors, steel racks can really damage and bend wider rollers, causing them to “wobble” and get progressively worse as more steel racks run down these conveyors.
4. Multi-Footed Plastic Thermoform Pallets 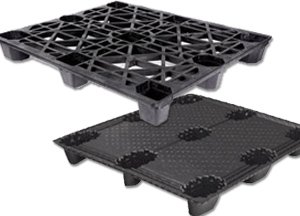
Many designers of conveyor systems find these pallet bottoms to be the most difficult to convey. Often times, these plastic pallets are thin walled construction (so they are not flat but rather warped / bent). They can have 9 individual “feet” on the bottom, often having a contact surface of less than 2” x 2”. Or, some of these pallets have 9 dual “feet”, which essentially have 18 very small contact surfaces against the conveyor.
Any way you slice it, these pallet bottoms are very challenging to convey. They convey best on narrow tracks of small diameter, heavy gauge rollers on very close centers. Or, if the load is not extremely heavy, multiple strands of mat top plastic chain or tabletop chain can be used.
Other considerations with pallet handling include:
- Quality of pallet / container bottom
- Is it flat and level, or is it chipped and has broken, protruding pieces?
- Based on the amount of contact surface touching the conveyor, how concentrated is the load as it is transferred to the conveyor?
- With gravity flow conveyor systems and pallets, it is important to remember that there is no 100% guarantee of conveyance 100% of the time
- With gravity flow conveyor systems, be aware of having sloped gravity conveyor systems which mate up to “level” gravity conveyor systems. These typically don’t work very well – product often will get hung up during the transition.
- When going from chain strands to full width roller conveyor or wide belts, be careful when using picture frame bottom pallets / racks / containers.
Comments
No comments have been posted to this Blog Post
Leave a Reply
Your email address will not be published.
Comment
Thank you for your comment.