The Final Step in the DMADV Decision Making Process: Validation
Marvin Logan | 30 July 2014
Validating a system design offers an array of benefits from risk avoidance to better resource forecasting. For this reason, validation is a critical part of the final design process.
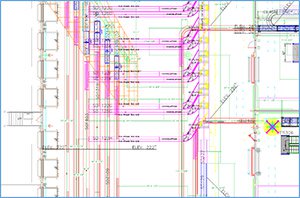
For several weeks, we have discussed the DMADV process for decision making. The first four (4) phases (Definition, Measurement, Analysis and Design) have been completed, so now we need to consider the effectiveness of the design(s). The complexity of the proposed layout, and its changes, will typically drive the method of which validation type, our 5th and final phase, should be used.
Why Do We Validate?
Validation, in some fashion, is extremely important in any project. This reasoning likens itself to the adage, “Measure Twice and Cut Once”. (Shameless plug for another blog article I’ve written). You would never want to invest time, money, resources and energy into an unproven… well, anything! Making it through the first four stages was the hard part, now we need to test the design(s) against real-world data and be sure it can pass your business’ litmus tests. Testing will allow us to determine the design’s ability to receive inventory, process orders, and understand systemic bottlenecks and inadequacies.
Validation Types
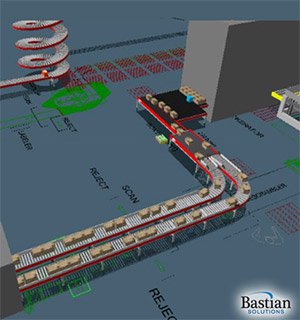
Determining the type of validation for the level of design is usually pretty straightforward. We offer several “flavors” of validation types. They can be as simple as a spreadsheet mock-up, with the inclusion of the system’s amenities, which in turn can give payback periods, expected resource utilizations and other high-level information. Or, if the system proves to be more complex in nature, we will use simulations to help mimic the flow of products, information and orders.
With simulations, we often make use of a couple different packages which allow us to virtually create the proposed design of the layout. Simulations allow us to "look ahead" and perform "what-if" scenarios prior to a single change made to the real system. We equate simulation to a painting, rather than a picture of the system.
Simulations have the ability to closely mimic product flows, picking and putting methodologies as well as a myriad of other practices very similar to its real world counter-part. Although, we realize that every detail can’t be duplicated (hence the painting metaphor). Yet, this method is leaps and bounds above a spreadsheet mock-up and proves vital in capturing additional system-wide details. By the usage and inclusion of statistical distributions, we can create “randomness” in the simulation that can be ran many times over yielding more concise findings than a one-dimensional table.
Simulation Process
Simulations are done in five (5) phases as well.
- Kick-off Meeting, Design Parameters and Assumptions
- We study and document the material flow and assumptions for the system.
- We then create an assumptions document that defines the objectives of the model, operation description, input data requirements, project schedule, and experimentation to be performed.
- Base Model Development
- The data collected from the assumptions document is built into the model and the associated processes.
- Layouts drawn and coding written to run the model.
- Validation / Verification / Model Review
- We then ensure that the computer model operates according to the parameters detailed in the assumptions document.
- Experimentation
- The model is then run with different experiments detailed in the assumptions document. This includes the testing of the sensitivity of the key system parameters.
- Final Reports / Review Meetings
- The final report includes all required graphs, tables, etc. that document the findings from the simulation and recommendations to move forward.
Validation Benefits
Validating a system design offers an array of benefits from risk avoidance to better resource forecasting. For this reason, validation is a critical part of any design process. Here are more benefits of a thorough validation process:
- Risk mitigation and cost avoidance
- The ability to challenge “what if” scenarios
- Increased confidence in the final design
- The ability to analyze expected throughput capability
- The identification of process bottlenecks
- The ability to measure cycle time for specific activities
- The ability to study the dynamic interactions within the facility
- The ability to determine optimum staffing levels in each area
- Avoid costly mistakes – verify design and ensure the material handling system will meet your current and future needs
- Help with integration to existing systems
- Establish and verify labor and manning requirements
- Experiment – see how changes to one area of your system affects other areas
By stepping through the five (5) phases of the process, we ensure that our customer’s needs, concerns and goals are met. This allows us to understand, in greater detail, their processes and vision to create the partnership necessary for their continued success.
Marvin Logan is the Vice President of Consulting and Integration at Bastian Solutions. After graduating from Purdue University, Marvin started his career as an industrial engineer and quickly moved into management. He has had roles as a distribution system manager, operations manager, director of engineering, director of distribution, and vice president of distribution for several leading companies.
Comments
No comments have been posted to this Blog Post
Leave a Reply
Your email address will not be published.
Comment
Thank you for your comment.