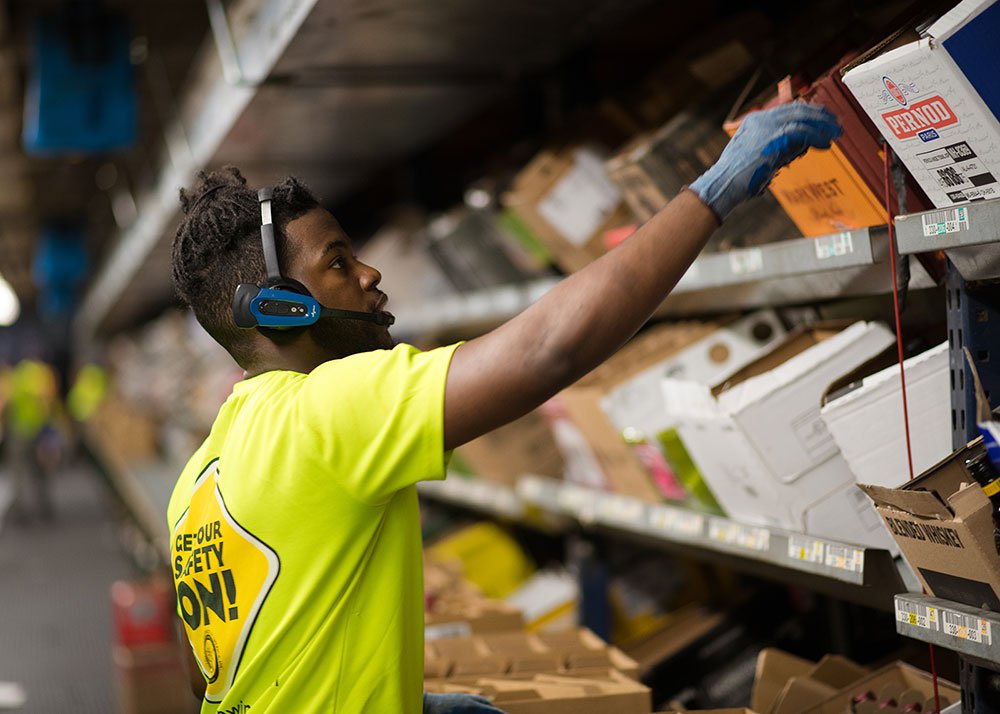
The Evolution of Pick Modules: Efficiency Meets Innovation
Blake Bearden | 22 January 2025
In today’s fast-paced order fulfillment landscape, fulfillment centers power the seamless shopping experience consumers have come to expect—delivering speed, accuracy, and innovation like never before. To keep up with increasing demand and consumer expectations, operations must strike the perfect balance between speed and accuracy. Distribution centers continue to rely on automation solutions like order pick modules for a good reason. These proven and reliable order-picking systems have evolved with advanced technologies to meet the demands of modern fulfillment operations, maximizing throughput and efficiency. In an era dominated by automation and robotics, pick modules remain adaptable and cost-effective, seamlessly integrating into hybrid operations to handle both high-velocity SKUs and slower-moving items with unmatched versatility.
Pick modules are transforming the landscape of order fulfillment, and for many distribution centers managing both ecommerce and traditional store orders, they’re more essential than ever.
Pick Modules vs. Goods-to-Person Systems
Goods-to-person systems are designed to minimize operator movement by bringing items directly to pickers. These systems are ideal for operations with a high number of SKUs and low cubic velocity. However, they can be cost-prohibitive for handling fast-moving or large items. On the other hand, pick modules provide a versatile and cost-effective solution for managing high-velocity SKUs. While goods-to-person systems focus on automation and centralized picking, pick modules excel in scalability and adaptability, making them an ideal choice for hybrid operations.
How Distribution Center Pick Modules Work
Pick modules can be single—or multi-level rack structures used to store inventory and facilitate item picking for order fulfillment. While the main component of a pick module is racking, these systems may include various rack types such as pallet flow, carton flow, or shelving. Depending on the configuration, pick modules can hold hundreds to thousands of SKUs.
Pick modules are highly versatile. Large distribution centers often feature multi-level pick modules with specialized levels tailored to specific product types. Alternatively, businesses can set up entire pick modules dedicated to specific product categories or configurations. For smaller operations or companies new to this technology, pick modules are a great way to gain confidence in the productivity and efficiency benefits and establish an efficient operation process.
Critical Elements of Order Picking Systems
Most of today’s order fulfillment thrives on speed, precision and adaptability. With their modular and scalable designs, pick modules have become central to this process. Below, we explore the key elements and technologies that make pick modules indispensable in today’s distribution centers.
1. High-Speed Transfers
A three-directional transfer conveyor within your pick module ensures quick, efficient carton handling. Like those from Bastian Solutions, high-speed right-angle transfers use advanced DC servos for precise, gentle handling. These transfers can divert up to 40 cartons per minute and accommodate cartons as small as 4” x 4”.
This capability allows operations to pick directly into shipping cartons, reducing touches and dimensional weight costs. By increasing the efficiency of transfers, businesses can reduce the size or number of pick modules required, leading to significant cost savings.
2. Optimized Carton Flow
Carton flow technology remains a cornerstone of efficient pick modules. By maximizing pick-face density, carton flow minimizes picker travel time and optimizes space utilization.
Depending on your needs, you can choose from full-bed rollers, rails, or plastic wheel beds for flexibility. Pallet flow can also be an option for extremely high-velocity SKUs, though it requires more space and increases picker travel time.
3. Smart Conveyor Systems
Conveyor systems have advanced significantly, with DC conveyors now offering zero-pressure applications to maintain the spacing and alignment of shipping cartons. Adjustable speeds and gappers ensure smooth flow even at rates of up to 60 cartons per minute.
Smart sensors detect products at put zones for added efficiency, pausing upstream movement when needed. This eliminates the need for operators to rush, ensuring product alignment and reducing errors.
4. Pick-to-Light (PTL) Technology
Pick-to-light systems are a game-changer for high-speed operations. When a shipping carton enters a zone, barcode scanners trigger lights on the carton flow rack, indicating which SKUs to pick. This technology enables operators to pick 400-600 lines per hour, depending on the layout. PTL's visual simplicity reduces errors and speeds up operations.
5. Put-to-Light Technology
A put to light system is similar to a pick to light system, only instead of picking product to ship to consumers, it is designed to replenish stock to a store. Put-to-light systems provide an efficient solution for sorting and consolidating orders. This technology uses light indicators at designated put locations to guide operators on where to place items within orders. Especially beneficial in high-volume operations, put-to-light streamlines sorting tasks and ensures order accuracy.
6. Dynamic Batch Picking
Batch picking—coupled with pick-to-light technology—takes efficiency to the next level. Operators can pick multiple orders simultaneously by grouping similar SKUs, significantly increasing throughput. With advanced systems in place, material handling equipment can keep pace, ensuring seamless order fulfillment.
7. Autonomous Mobile Robotics
AMRs are transforming warehouse operations by efficiently transporting goods between pick zones and consolidating orders. AMRs can also dynamically adapt to changing warehouse layouts and demand patterns.
8. Artificial Intelligence (AI) and Machine Learning (ML)
AI and ML are revolutionizing order-picking processes by analyzing historical data to predict demand, optimize picking routes, and enhance inventory management. Predictive analytics helps reduce stockouts and ensures faster replenishment cycles.
The Role of Warehouse Intralogistics Software in Order Picking
Integrating advanced software is essential to achieving greater efficiency. Bastian Solutions’ Exacta intralogistics software integrates seamlessly with your existing host systems through Exacta WES or WCS solutions. This software manages important order information, sending real-time updates as picks are completed or batching updates as individual orders are finalized. Additionally, operator performance metrics are accessible through Exacta’s detailed reporting tools, providing insights to enhance productivity.
Enhance Your Fulfillment Operations
Whether you’re looking to optimize existing operations or implement a new pick module, choosing the right material handling automation integrator is key. By embracing advanced material handling technologies found in modern pick modules, you can stay ahead in the competitive e-commerce landscape. Partnering with experienced automation integrators, such as Bastian Solutions, ensures your operations are optimized for peak efficiency and adaptability.
Talk to an engineer today to learn how pick modules and other advanced material handling technologies can transform your fulfillment center.
Blake Bearden is a District Director with Bastian Solutions and works out of the greater Los Angeles area office. He graduated from the United States Air Force Academy with a degree in human factors engineering and has an MBA from Embry-Riddle Aeronautical University. Blake has experience with automation across a range of industries including 3PL, retail distribution, manufacturing, food and beverage, and e-commerce and omni-channel fulfillment.
Comments
No comments have been posted to this Blog Post
Leave a Reply
Your email address will not be published.
Comment
Thank you for your comment.