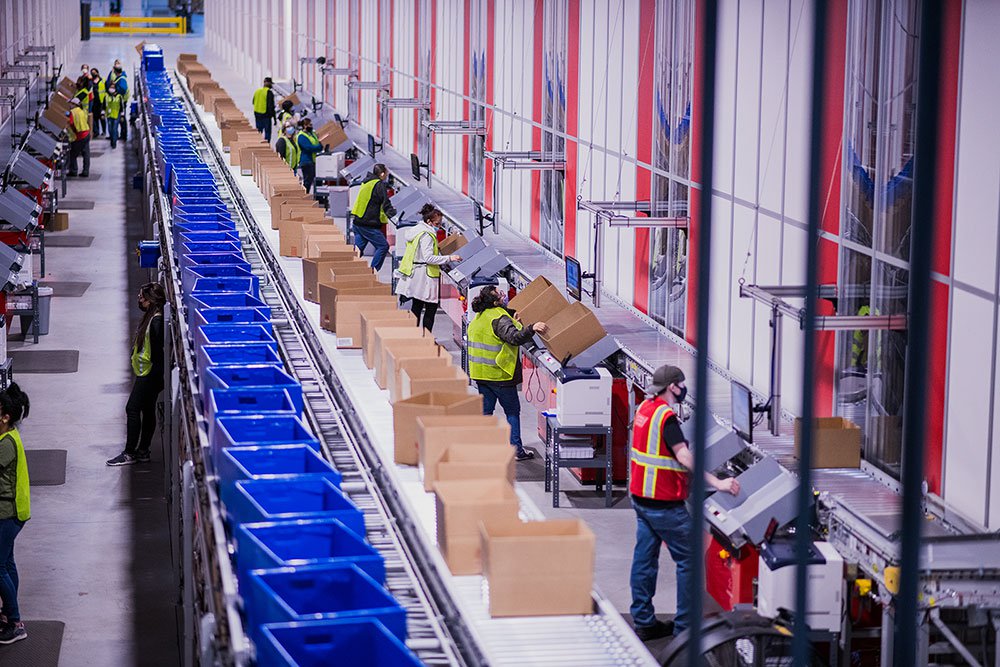
Strategic Operations in Warehouses: Enhancing Efficiency Through Automation
Carlos Minjares | 16 July 2024
“The first rule of any technology used in a business is that automation applied to an efficient operation will magnify the efficiency. The second is that automation applied to an inefficient operation will magnify the inefficiency.” Bill Gates
This quote highlights a fundamental truth: the success of automation hinges not just on the technology itself but on the underlying efficiency of the processes it aims to enhance. This means that strategic planning and process optimization are essential prerequisites for reaping the full benefits of automation in warehouse operations.
The logistics landscape has transformed dramatically over the past few years. Several factors drive this evolution, each presenting unique challenges and opportunities for warehouse operations:
- Ecommerce Growth: The surge in online shopping has significantly increased order volumes, necessitating faster and more efficient delivery systems.
- Demand for Fast Deliveries: Customers now expect rapid delivery times, putting pressure on warehouses to streamline their processes.
- Supply Chain Complexity: Modern supply chains are intricate and multifaceted, requiring sophisticated management strategies to ensure seamless operations.
- Labor Scarcity and Rising Costs: The shortage of skilled labor and increasing wages are pushing businesses to find alternative solutions to maintain productivity.
- Technological Advances: Innovations in technology offer new tools and methods to enhance efficiency and effectiveness in warehouse operations.
- Focus on Efficiency and Sustainability: There is a growing emphasis on making logistics operations more efficient and sustainable to reduce costs and environmental impact.
Understanding these factors is crucial for businesses looking to implement or enhance warehouse automation. By identifying their specific challenges and leveraging the right technologies, companies can significantly improve their operational efficiency and responsiveness to market demands.
Identifying Opportunities for Warehouse Automation
Recognizing potential areas for automation within warehouse operations is the first step toward optimizing efficiency. Here are foundational criteria to consider:
- Repetitive Manual Operations: Repetitive and labor-intensive tasks are prime candidates for automation. Automating these operations can significantly reduce human error and increase speed.
- Key Processes: Focus on automating crucial processes such as receiving, material movement, picking, and order preparation. These areas often involve high volumes of manual work that can be streamlined with automation.
- Product Identification through Barcodes: Automation is more effective when products can be easily identified through barcodes or other means. This facilitates tracking and inventory management.
- Suitability of the Intralogistics Software: Ensure your software can support automation. A robust software platform can integrate with various automated systems, providing seamless operations.
- Optimization of Current Processes: Optimize your existing processes before implementing automation. Automation applied to inefficient processes will only magnify inefficiencies. Streamlining workflows and eliminating bottlenecks will maximize the benefits of automation.
Solving Operational Problems through Warehouse Automation
Automation can address several common challenges faced by warehouses, leading to significant improvements in operations:
- Accurate Inventory Management: Implementing technologies like RFID and automated inventory tracking systems can enhance inventory management and product location tracking accuracy.
- Reducing Picking, Packing, and Shipping Errors: Technologies like voice picking, pick-to-light systems and automated packing solutions can minimize human error and improve order accuracy.
- Managing Peak Season Fulfillment: During peak seasons, the volatility of orders can be managed with autonomous robots, conveyor systems and goods-to-person technologies, ensuring timely fulfillment.
- Efficient Use of Warehouse Space: Automated storage and retrieval systems (ASRS) and optimized layout designs can maximize available space, reducing congestion and increasing storage capacity.
- Finding and Retaining Qualified Personnel: Automation solutions can help mitigate labor shortages by taking over repetitive tasks, allowing personnel to focus on higher-value activities. This can also reduce turnover and improve job satisfaction.
- Reducing Order Processing Times: Implementing warehouse control systems (WCS) or warehouse execution systems (WES) can automate and optimize order processing, reducing delays and enhancing throughput.
- Lowering Product Return Rates: Automated quality control processes, such as vision systems and automated weigh-scales, can ensure product accuracy and reduce the incidence of returns due to wrong item or other defects.
- Enhancing Safety and Reducing Accidents: Safety can be improved by implementing guards, movement sensors, automated safety doors, and comprehensive safety training for personnel.
Businesses can harness automation's full potential by strategically identifying and addressing these areas, transforming their warehouse operations into highly efficient and responsive hubs.
Role of Material Handling Automation Systems Integrators
Collaboration with systems integrators and automation suppliers is crucial for successfully implementing warehouse automation. Integrators like Bastian Solutions bring a wealth of knowledge and experience, helping businesses navigate the complexities of automation and ensuring that all components work seamlessly together. They play a vital role in bridging the gap between technologies and processes, working closely with businesses to understand their unique needs and challenges. Integrators ensure the implementation process runs smoothly by providing tailored solutions that align with operational goals and facilitating communication between various stakeholders. Many companies have significantly benefited from such partnerships, achieving remarkable efficiency and operational effectiveness improvements through strategic automation initiatives.
Warehouse Automation Success
One of the standout examples of successful warehouse automation is the PUMA distribution center in Whitestown, Indiana, USA. PUMA's warehouse worked with Bastian Solutions to implement various advanced technologies to streamline operations. These included a Warehouse Execution System (WES), "put to light" devices at picking stations, automated labeling machines, in-line scales, a comprehensive conveyor system stretching 16,000 feet, automated box cutters, and customized packing equipment. Additionally, an AutoStore goods-to-person system featuring 175 AutoStore robots and 305,000 totes was integrated to enhance efficiency further.
The implementation of these technologies led to remarkable enhancements in PUMA's warehouse operations:
- Order Cycle Time: The order cycle time improved drastically, reducing from 8 days to just two days.
- Warehouse Capacity: The capacity of the warehouse increased more than tenfold, accommodating a vast inventory of 5.5 million units and 45,000 SKUs.
- Inventory Management: Inventory management efficiency was significantly boosted, facilitating better tracking and handling of products.
- Shipment Density: A 25% increase in shipment density was achieved through made-to-measure packaging for orders.
- Processing Volume: The warehouse managed to ship over one million units monthly and expects to double this number within the first year.
- Picking Efficiency: Integrating the AutoStore system enhanced picking efficiency by reducing the time personnel spent walking around to pick orders.
The PUMA case study exemplifies how a well-planned and strategically executed automation initiative can transform warehouse operations. By adopting advanced technologies and collaborating with experienced systems integrators, PUMA achieved significant efficiency, capacity, and overall operational effectiveness gains.
Warehouse automation offers immense potential for improving logistics operations' efficiency, accuracy, and productivity. However, the success of automation initiatives depends on strategic planning, process optimization, and effective collaboration with systems integrators. By understanding the evolving logistics environment, identifying opportunities for automation, addressing common operational challenges, and learning from successful implementations, businesses can unlock the full potential of automation and gain a competitive edge in the marketplace.
Ready to transform your warehouse operations with cutting-edge automation solutions? Contact Bastian Solutions today to speak with one of our experienced engineers.
Carlos has over 20 years of experience in logistics, manufacturing and operations. He started as an operations coordinator in a manufacturing plant, then moved to the logistics world overseeing 13 warehouses. He worked for a prominent 3PL company designing and improving warehousing solutions. Currently, with Bastian Solutions, he has concentrated on elevating operations to a higher standard by integrating cutting-edge technology and embracing automation to enhance efficiency and productivity.
Comments
No comments have been posted to this Blog Post
Leave a Reply
Your email address will not be published.
Comment
Thank you for your comment.