Split Case Picking Systems: A Beginner's Guide, Part 2
JD Stumpf | 14 February 2019
Options for Designing a Split Case Picking System
Part 1 of this Beginner's Guide explained what split case picking systems are. Next we explore the various decisions and options involved when designing a split case picking system.
The diagram below helps illustrate the components of the various split case picking systems available.
Adapted and modified from The classification of order picking system categories (Dallari et al.,2009)
Physical Pick Execution
Who is going to physically pick items? There are essentially three options: humans, machines, or robots. The overwhelming majority of operations are only concerned with humans picking, but take note that robotic piece picking applications are maturing rapidly. Mechanized picking with A-frames or dispensers are prevalent but only apply to a limited range of items.
Is It the Goods or Picking Operators That Move During the Picking Process?
The most common systems utilize a Person-to-Goods (PTG) format where operators are walking in aisles or pick modules. However, over the last decade there has been widespread adoption of Goods-to-Person (GTP) technologies and this trend will continue. Technologies such as the AutoStore, Perfect Pick and AGVs provide unparalleled throughput and high storage density compared to traditional picking systems. More recently, there are pilot versions of Goods-to-Robot (GTR) where robots piece pick from goods-to-person technologies as well as Robot-to-Goods (RTG) where robots piece pick from static shelving or flow rack. These systems are in their infancy but will continue to evolve rapidly over the next few years.
Transport Methodology
Will humans (via carts or vehicles), autonomous robots or conveyors transport orders from location to location during the picking process? Most DC’s start up with cart picking and naturally progress to conveyor transport when throughput requirements warrant the investment. There is now an intermediate technology available in Autonomous Mobile Robots (AMRs) that improves the picking process by removing most of the travel requirements for picking operators but does not require the ‘permanent’ investment of conveyor systems.
Picking Methodology
A general decision should be made as to whether the picking process will be by order or by item. When picking by order, no downstream sortation is required. When picking by item, downstream sortation is required to sort items to orders.
- Discrete Order Picking – The most common and least complex method of order picking, this is where an operator is picking to one order, one line at a time. Discrete order picking can utilize pick to cart or pick to conveyor transport methodologies. If pick to conveyor, then there are ‘pick and pass’ (every operator touches every container) or ‘zone routing’ (containers only divert to zones where picks are required) formats available.
- Discrete Order Batching (Cluster) Picking – Operators pick into multiple order containers at one time which reduces the travel time per order line, thus, increasing picking productivity. Items are sorted to the individual orders during the picking process, therefore no downstream sortation is required. For maximum benefit, the Warehouse Management System (WMS) batches orders together that share common SKUs. Cluster picking can be used in conjunction with pick carts, conveyor put-to-light sort positions, and goods-to-person technologies such as shuttles, VLMs, carousels, AGV’s.
- Batch Picking – Multiple orders are grouped together in ‘batches’ and picked by item into a single transport container. Items are then sorted to individual orders downstream using manual or automated methods (putwalls, sure sorts, unit sorters). Batching increases picking productivity as the average travel distance per pick is decreased, however, additional labor is required to sort items to orders. Batch picking can be deployed in pick to cart or pick to conveyor environments. Generally speaking, batching makes sense when the additional cost of labor and space to sort items to individual orders is less than the cost of picking orders discretely. Batching orders together also reduces material handling requirements as there are less containers to process through the system.
- Wave Picking – Similar to batch picking, a large group of orders are grouped together in a ‘wave’. The warehouse is organized into zones and SKU demand is aggregated for orders in the wave and batch picked from each zone simultaneously, in parallel, and transported to the sortation and consolidation area. This is often-called parallel zone picking. Wave picking is different than batching picking as orders are not picked complete into one transport container. Picking productivity is significantly increased as each pick location is visited only once for a wave. Systems can be designed to process many waves simultaneously. This picking methodology is most suitable for high SKU count operations where order volumes exceed MHE and picking capacity if orders were picked discretely or by batching.
Picking Technology
There are more picking technologies available on the market today than ever for companies looking to improve productivity and accuracy in their order picking operations. The table below highlights some of the most common technologies utilized in picking operations along with a short list of key benefits and drawbacks.
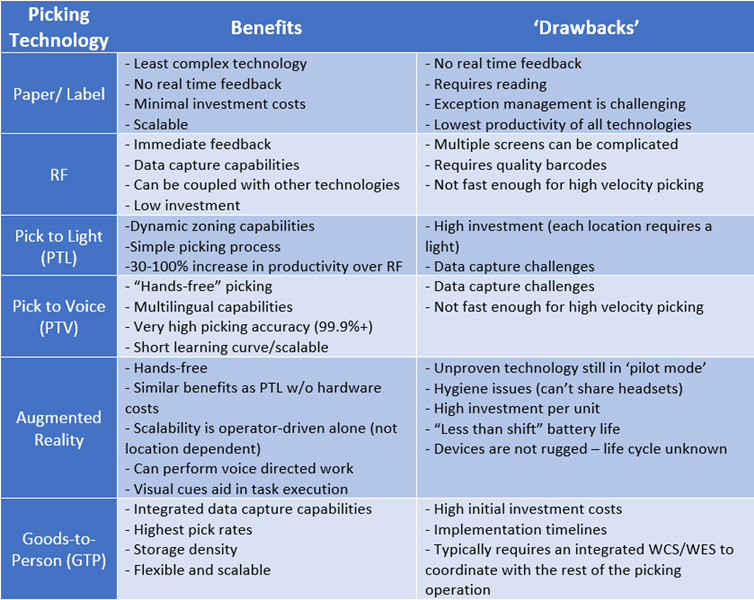
Sorting Technology
If batching or wave picking, then sortation of items to discrete orders is required. The use of manual put walls are fairly common where items are sorted to ‘cubbies’ using RF or put-to-light. There is now a form of an automated put wall with OPEX’s Sure Sort technology that uses robots to deliver items to cubbies which eliminates the need for ‘putting’ labor. Like manual put walls, completed orders in the sure sort are removed from the cubbies and packed into shippers. High volume operations utilize unit sorters to sort items to chutes or even put walls.
Which Split Case Picking System Design is Best?
After considering the various storage, transport, picking and sorting technologies coupled with the different picking methodologies available, it is easy to realize that there nearly innumerable design alternatives to consider. Consequently, distribution center design professionals are frequently asked “which split case picking system is best? Truth be told, there is no such thing as a universal ‘BEST’ split case picking system or technology, but there is a ‘BEST FIT’ solution for a set of business and operational requirements.
Determine the Design Factors & Decision Factors
With all distribution design and optimization projects, it is crucial to take a structured and objective approach that considers a wide variety of applicable technologies and processes. The first step in the design process is to conduct a thorough distribution center activity profiling exercise and document business requirements to determine the key design factors. The key design factors serve as a road map during the design process and help narrow the scope of feasible alternatives to consider.
After feasible design alternatives have been generated, one must conduct a formal economic analysis and evaluate the key decision factors relevant to your design or re-design objectives. While not intended to be comprehensive, some of the most common design and decision factors evaluated are listed in the table below.
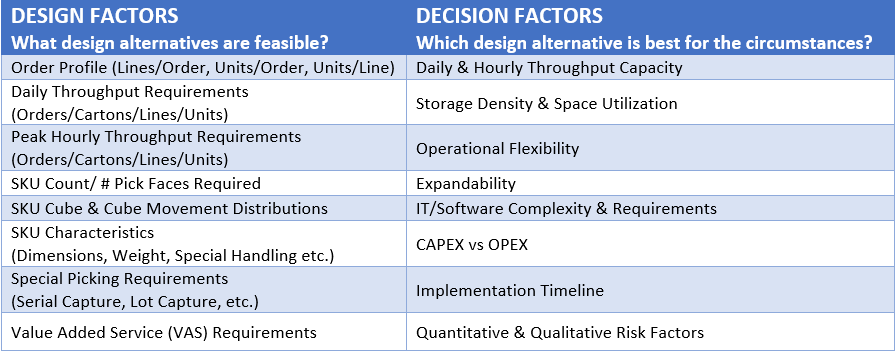
With all of the configurations possible for a split case picking system, it's hard to pick the best one for your operations. Part 3 of this guide explores important considerations when choosing a split case picking system design to best suit the needs of your unique operations.
J.D. is a Senior Consulting Engineer with Bastian Solutions out of Denver, CO. He received both his Bachelor and Master of Science in Industrial Engineering from the University of Missouri. His specialties include data analysis and modeling, simulation, warehouse design & operational excellence. Experience includes: eCommerce, Footwear/Apparel Retail, Health, Beauty and Cosmetics and Consumer Electronics.
Comments
No comments have been posted to this Blog Post
Leave a Reply
Your email address will not be published.
Comment
Thank you for your comment.