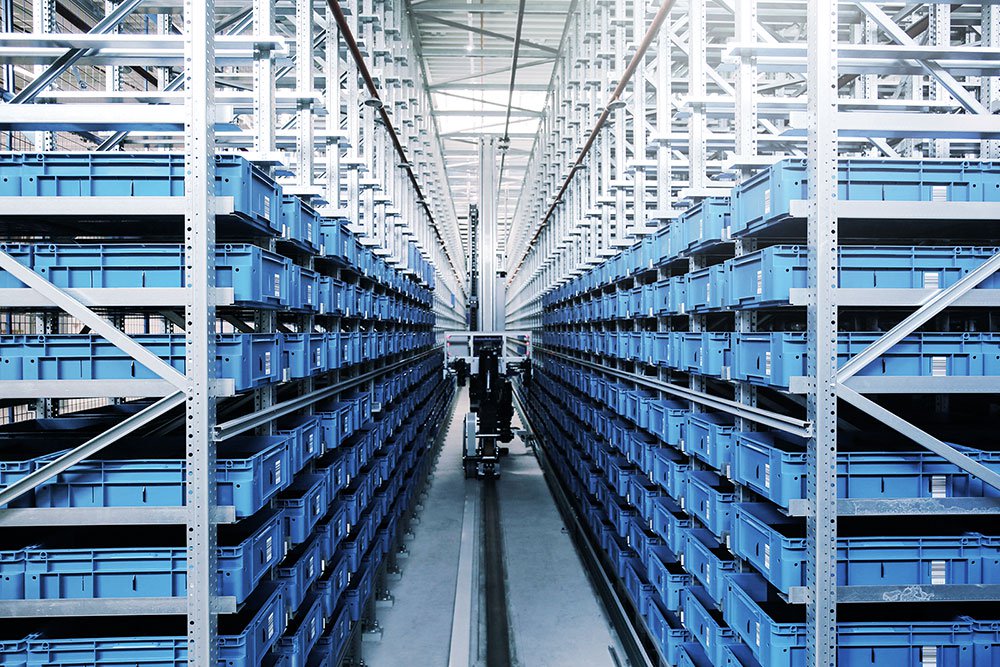
Solve the Complexities of Payload Storage and Retrieval
Sriram Bandal | 4 January 2022
Managing a warehouse operation is not an easy job. Land costs and warehouse leasing charges are increasing exponentially. At the same time, there is also limited availability of trained operators which adds to expenditures, either in training cost, recruitment or addition of new technology that fulfils the task. However, for a business to successfully meet consumer needs, it is essential to optimize the centre for picking, storing and shipping. These opportunities for efficiency cannot be overlooked.
By upgrading to an automated storage system, forklifts no longer need to travel beyond the shipping dock and lane entry, reducing labour requirements, traffic, and risk of damage to product and storage racks. In manufacturing and warehouses, AS/RS or Automated Storage and Retrieval Systems are a safety enhancement, provide productivity improvement and save floor space by replacing large shelving areas. These systems are beneficial to automatically transport pallets, heavy loads, and move totes containing smaller items in and out of storage locations.
To maximize return on investment it’s imperative to fully understand why, when and which AS/RS technology is the right solution for the task.
Introducing an AS/RS System
Mitigate unexpected expenses, reduce time and appropriately utilize resources by selecting the right automation solution from the start. AS/RS systems can automatically place and retrieve loads from the specified storage locations in a facility with accuracy and speed. There are multiple variations of AS/RS systems – cranes, shuttles, lifts and cube-based systems –available to fulfil different warehouse purposes.
- Crane-based Mini load and Unit Load AS/RS systems can easily store and handle the weight from 300 kg to 3000kg. These cranes move inside the racks to store and pick the products and can reach a height from 27m to 37m.
- Shuttle AS/RS which are either fully automatic or semi-automatic are suitable for LIFO (last in, first out) or FIFO (first in, first out) product flow operation and if you have fewer varieties of SKUs. These systems can handle the load from 1500kg to 2000 kg and can reach up to 12m height for storage racking and lifting.
- Vertical lift modules and industrial carousals consist of a column of trays in the front and back of the module with an automatic inserter/extractor in the centre that stores and retrieves the required trays, totes, bins and more.
- Cube-based systems are the goods-to-person technologies to store and retrieve inventory bins in a cubical storage grid. These are best for micro fulfilment centres and high-density storage.
When to Invest in AS/RS
Regardless of whether you are considering a mini load, unit load or custom AS/RS crane, an automated storage and retrieval system is an investment.
As you evaluate whether an AS/RS solution is the right fit for your needs, consider the following key business objectives and operation points:
- Are you struggling to keep up with throughput?
- Do you need 24/7 operation for demand fulfilment?
- Are you noticing frequent errors in product or parts storage and retrieval operations?
- Are you looking to reduce worker/co-worker injuries and improve working environments?
- Do you see low productivity and efficiency?
- Do your products require extreme working conditions, like refrigeration or frozen storage?
- Is labour availability a challenge or are you looking to make better use of staff? With the AS/RS, employees can focus on value-added tasks that will benefit your bottom line.
Factors For Selecting the Right Technology
As with all warehouse solutions, understanding company timelines, needs and objectives can help clarify and narrow the right automation selection for your specific situation. Some storage and/or retrieval automation options and combinations of technologies provide faster project time frames than others.
These are few factors for initial discussions to select the optimal technology:
- Facility structure, available footprint and vertical space, storage locations
- Product details - bulk or parts storage needs, SKUs
- Order sequencing or buffer needs
- Throughput needs
- Labour availability
- Extreme conditions – clean room environment, quality control, refrigeration, freezer, seismic concerns
Solve the Complexities Now
Automated storage and retrieval offer a great solution for a variety of industries and applications where high-volume products repeatedly move in-and-out of facilities. Through its vertical structure, AS/RS can add to your existing or future operations and bring an added level of inventory storage security creating for a dependable solution and solid return on investment.
A turnkey or custom solution, utilizing AS/RS increases throughput and efficiency, saves space and allows you to use your vertical space for reduced facility expansion costs.
Our experts have designed and integrated automated storage solutions across a variety of industries and product handling needs. With this expertise, they can assess your operational needs, business objectives and technology options to identify a right-sized automated solution to reliably and effectively handle the complexities of moving and storing payloads in your facility. From large, heavy pallet storage to smaller, lightweight goods, or custom features that accommodate unique requirements, our experts work with you to integrate the appropriate level of flexibility and functions.
Sriram is a Sales & Application Manager at Bastian Solutions India. He has a degree in Mechanical Engineering from Pune University and brings more than 10 years of experience in product management, applications and sales experience in EOT (electric overhead traveling) cranes, forklift trucks and the material handling automation Industry.
Comments
No comments have been posted to this Blog Post
Leave a Reply
Your email address will not be published.
Comment
Thank you for your comment.