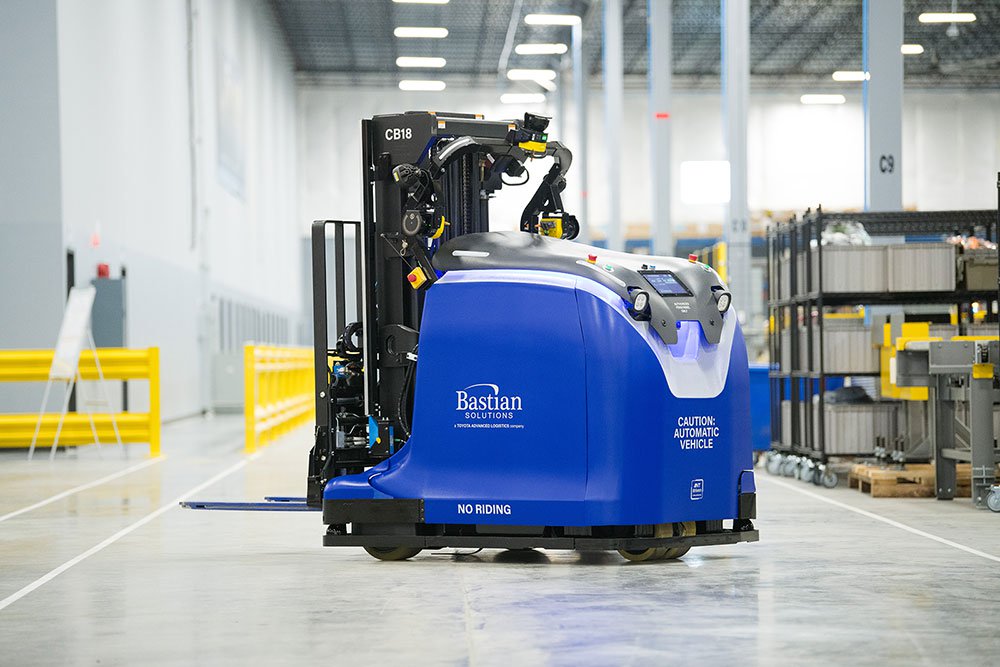
Self-Driving Forklifts: The Future of Pallet Transportation
Kyle McMillin | 25 October 2023
The fascination with automation has been amplified by the rise of AI (artificial intelligence) and the emergence of seemingly self-driving cars. This trend has made “automation” an ubiquitous term worldwide.
Manufacturing and warehousing facilities are at the forefront of adopting automation due to the numerous advantages it offers, including waste reduction, increased production efficiency and a compelling ROI (return on investment). In fact, technology like self-driving vehicles isn’t new to the warehouse environment but it has come a very long way since it was first introduced. In this post, we’ll dive into how advanced technology is being leveraged to complement warehouse operations and how you can plan for successful integration.
The Role of Autonomous Vehicles in Intralogistics
In these modern distribution centers and factories, material handling equipment and human operators work collectively to efficiently produce, store and move goods. The degree of automation in each facility varies and is dependent on many factors – complexity of operations, materials handled and environment, just to name a few. When properly designed and integrated, automation doesn't replace human team members but complements human labor efforts by streamlining processes, allowing them to focus on tasks that demand intuition and creativity.
Automated Product Movement
The concept of self-driving vehicles isn’t new to industrial and warehousing sectors; in fact, AVs (autonomous vehicles) have been automating processes in those facilities for years. Historically, these mobile solutions were exclusively guided by fixed infrastructure (e.g., magnetic tape, RFID, etc.) and carried out simple tasks in operator-free environments. Today, companies are faced with challenges such as customer demands for faster cycle times, seasonal operational changes and increased safety requirements that necessitated a more agile, scalable solution for product movement.
The Future of Pallet Transportation is Here
To help address this automation gap, Bastian Solutions unveiled the CB18 at the ProMat Conference in Chicago, IL. The CB18 AGF (automated guided forklift) stands out as a versatile and adaptable automation solution designed to enhance material handling operations in both factory and warehouse settings. Leveraging the robust research and development capabilities of Bastian Solutions, the CB18 boasts a range of industry-leading features, including:
- BlueBotics ANT Driven 2D LiDAR guidance technology
- Impressive 4,000 lbs. (1,800 kg.) load capacity
- 360-degree Category 3 LiDAR safety rated system with cantilevered load detection
- Virtually zero turn radius (ZTR) for exceptional maneuverability
- Simultaneous motion along multiple axes:
- A maximum lift height of 14.7 feet
- Side shift capability of 5.6 inches in both left and right directions
- Tilt function up to 5 degrees
With travel speeds of up to 3.0 m/s when moving and having the forks trailing, and up to 2.0 m/s when moving forks forward, the CB18 also features advanced tricycle kinematics design with front traction wheels, mitigating slippage concerns. This design accounts for the growth of friction coefficients with increasing payload weights. The vehicle’s regenerative braking is enhanced by electromagnetic failsafe system that activates in emergency situations.
It’s oversized mast which reduces deflection at height and ensuring precise product placement. It also includes industry leading inductive, non-contact opportunity charging allowing for 24/7 “hands free” operation. Like all automation equipment and systems, maintenance and support are crucial to keeping operations running smoothly. The CB18 is supported through the expansive network of Toyota Material Handling (TMH) and Raymond technicians to enhance ease of maintenance and repair processes.
Planning For Successful Autonomous Vehicle Integration
Making the decision whether to automate a process is step one. Next, is determining how that process will be automated. When contemplating the implementation of AGFs within your operation, addressing the following points helps to create a successful system:
- Process Standardization: Before automation can be implemented effectively, it’s crucial to have a standardized process in place. This involves defining step-by-step procedures for how tasks are performed. In cases where institutional knowledge or varying approaches exist; the first step is to create a clear and documented SOP (standard operating procedure).
- Exception Handling: Automation doesn’t eliminate the possibility of quality defects or exceptions in the process. It’s essential to plan for these scenarios by creating designated locations or workflows for exception handling. This allows for efficient identification, correction, or removal of defective items without disrupting the primary automated flow.
- Data and Monitoring: A standardized process also facilitates data collection and monitoring. Automation systems can generate valuable data for performance analysis and quality control. Having a standardized process ensures that the data collected is consistent and meaningful.
- Kaizen (Continuous Improvement): Once a standardized process is established and automation is in place, it becomes easier to identify areas for improvement.
- Training and Documentation: Alongside SOPs, training programs and documentation play a crucial role. Ensure that employees are trained to follow the standardized procedures and understand how automation interfaces with the process. At Bastian Solutions, we uphold the principle that customers should have complete ownership of their system. Our training programs cater to a wide spectrum of expertise levels, from beginners to advanced operators. Importantly, our approach ensures there are no “black boxes” that are exclusively accessible by the OEM (original equipment manufacturer).
Maximize Automation System Productivity
The innovative CB18 transforms not only floor operations but interfaces with other manually operated and automated material handling equipment to increase the productivity of the entire system. Our experts will analyze your current processes, carefully design and seamlessly integrate a cutting-edge solution that optimizes your manufacturing or distribution operations with efficiency and precision. Reach out today to discover how a CB18 and other AVs can support your business goals.
Kyle McMillin is an Application Engineer at Bastian Solutions’ Autonomous Vehicles Group, based in Georgetown, KY. He has Bachelor of Science degrees in Supply Chain Management-Engineering and Finance from Auburn University. As an Application Engineer, Kyle works with clients to analyze, design, and implement autonomous vehicle systems.
Comments
No comments have been posted to this Blog Post
Leave a Reply
Your email address will not be published.
Comment
Thank you for your comment.