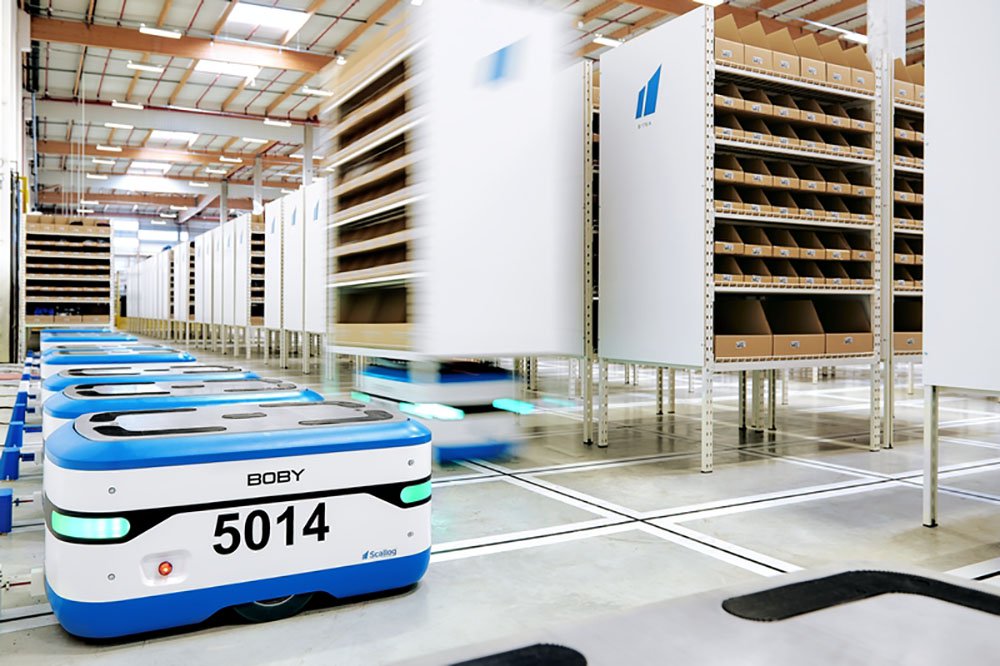
Scallog: Creating a Resilient Solution for the Future of Warehouse Logistics
Bailey Ludlam | 28 April 2021
Dynamic and easily scalable, goods to person technologies have risen to the forefront of order fulfillment conversation amid rapid ecommerce growth. Answering the challenge of automation for various industry applications and operation sizes, Scallog’s order fulfillment system adds a mobile robotic solution to the mix. Announced late last year, Bastian Solutions, an independent integrator, has added Scallog’s technology to our growing portfolio of automation capabilities.
We talked to Olivier Rochet, founder and president of Scallog, for a deeper insight on the technology and future of DC automation development. This French robotic automation system manufacturer, already installed in six countries, offers a goods to person technology based on robots that move shelves around the warehouse.
“It’s necessary to have a system that can move and grow with possibility. It can’t just be a flexible solution. It needs to also be a resilient solution for the future,” says Olivier Rochet.
Q: The ability to adjust operations is a big focus right now with the uncertainties of COVID-19 with respect to investments, workforce changes, and future planning. What kind of flexibility does Scallog technology bring?
It’s very complex to know what the future will be so our customers are looking for very scalable solutions. Solutions that can adapt in the future. They want to start with a small system and grow with the system. And, we agree. We often say – start small, think big, scale fast. That formula is adopted into our systems.
Because our system is based on a fleet of mobile robots, you can start with a small system of 10 or 20 robots and add more robots or add more shelves. You don’t need to start with a big configuration. The main point is to have a very smart hardware, smart robotics, and complete with a global software solution that can be adapted to the configuration of our customer. The big value of our system is the capacity of the software to adapt.
Q: What efficiencies and optimizations does Scallog technology target in a warehouse?
The objective is to optimize the logistics process of our workers. The main problem today is that a manual process is not efficient because workers need to work throughout all of the warehouse to pick products and prepare orders. We know that of a worker’s time, 70% is lost because of time spent walking around the warehouse throughout the day. It can be about 15km (9.3 miles) per day. That’s a lot of wasted and unproductive time.
The Scallog system consists of a fleet of robots that move shelves around the warehouse, around to workstations, and without walking, the worker can prepare each order at the workstation. The big benefit is to stop the waste of time. We aim to focus on the operator’s value in the picking process.
Q: How does mobile robotics impact the work environment for operators?
It’s always about how to keep the operators at the heart of the logistics system. We don’t want to delete the human and work in a total robotic environment. We want to improve the work conditions.
In terms of ease of use, today, the work environment is changing in that the tools you need must be able to be understood very quickly. You need to have something simple to understand and simple to use that doesn’t require two days of training. At Scallog we focus on simple screens, easy information gathering from different sources, and different levels of complexity that fit both managers and operators. This creates easier and better work conditions.
Q: What does the future of autonomous vehicles and mobile robotics look like?
Scallog started eight years ago and at this time there weren’t a lot of companies like us. Now, I think the future will go to this type of product – very smart and robotic solutions. With Scallog we have a lot of applications with different types of customers, and it’s adaptive to a lot of different types of warehouses.
Of course, it’s obvious that ecommerce specialists like Amazon and others want to use automation. But now we are also seeing that even smaller companies that used to work manually are also interested and want to try new solutions that better fit their need – in return on investment and in terms of flexibility.
We know that 90% of the market is not currently using automation – that they don’t currently experience a need. Our solution is still a novelty solution. We want to be an expert in it to have the capacity to bring the value to small and different systems. Starting small, you can grow faster and better.
Q: Goods to person systems have been around for a while and there are numerous combinations of technologies that can be implemented to create custom solutions. What kind of concepts or concerns are top of mind for future tech development?
The technology will continue to improve in terms of robotics, in terms of hardware and sensor solutions, but that’s not the main point. The main point is that effectively in the future we will have more efficient robots and sensors, and lower cost. The objective is to have low cost products that are more accessible and remain reliable.
In terms of where you’ll see this technology, we could install these systems in a lot of different environments – microfulfillment, warehouses, stores, parking structures and probably many other environments. The future will not only be a big warehouse but a lot of different warehouses around the city. For that, we need to have small systems that we can move and change their location. It can’t just be a flexible solution. It needs to also be a resilient solution for the future.
Most of our systems work with other technology and automation like conveyor and put to light systems. The future is to have global integration of these type of systems. That’s why we are working with integrators like Bastian Solutions because we really think the future is to have global automation between inbound and outbound logistics. And, for that, there is not just one solution. Different smart systems need to be integrated globally and each of these need to be efficient and with really simple plug and play integration.
Bailey is the Brand Manager at Bastian Solutions, based out of Indianapolis, Indiana. She is PCM certified through American Marketing Association, has a bachelor’s degree from Washington College and 10 years experience working in marketing and journalism. Outside of work, Bailey enjoys spending time with her husband and two children and can usually be found hiking, running or creating with LEGO bricks.
Comments
No comments have been posted to this Blog Post
Leave a Reply
Your email address will not be published.
Comment
Thank you for your comment.