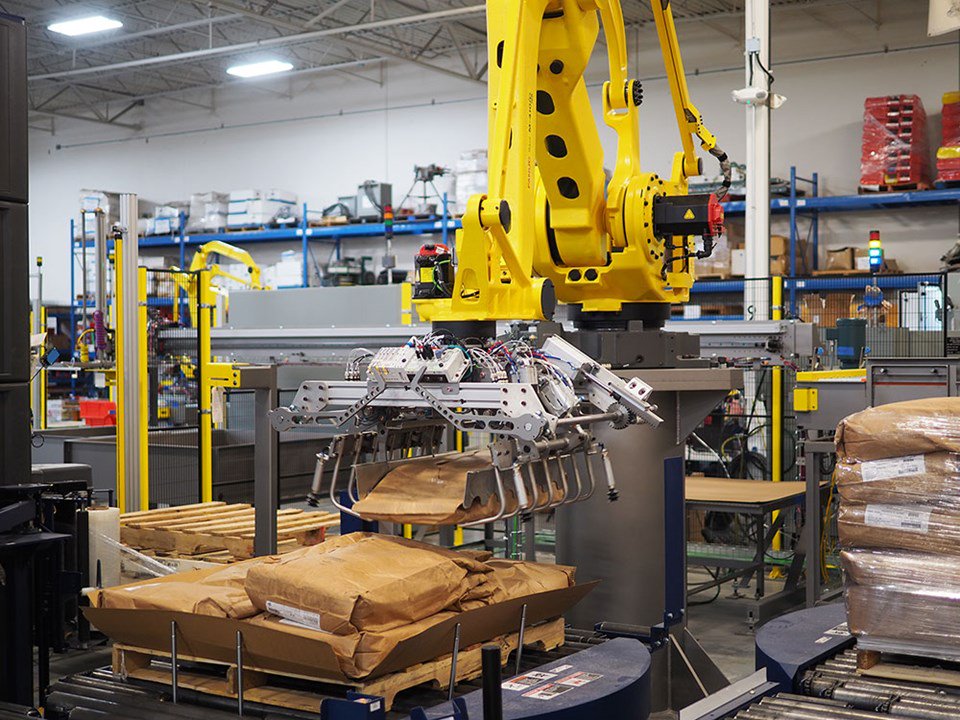
Robotic Bag Palletizing: Making Light of Heavy, Difficult Lifting
Trent Wideman | 24 July 2024
Most manufacturers are well aware that manual palletizing is no easy job. Awkward movements, repetitive motions and production requirements make for a challenging process that is difficult to keep staffed. Throw in the requirement that handled products are 50 lb. bags – which can be unwieldly and hard to hold and balance – and a difficult job to staff becomes a close to impossible. This is a well-known challenge for any manufacturers that handle bags, totes or oddly shaped items like tires. The geometry of an item can pose a challenge just like weight and size.
Robotic bag palletizing is a tried-and-true automation solution that allows for the reallocation of your staff to avoid costly on-the-job injuries and increased job satisfaction. The automation will also result in higher line uptimes and greater throughputs to be handled.
Optimizing Robotic Bag Palletizing Operations
End of Arm Tooling
Typical bag palletizers utilize a “clamshell” style EoAT (end of arm tool), which features actuating fingers that engage or scoop the bag. This style of tool allows the robot to handle the bottom surface of the bag to ensure maximum load handling stability. This tooling is paired with an infeed conveyor that features gapped conveyor rollers to allow for the EoAT to close around the bag in between the rollers. The end of arm tool also features a top tamp and side squaring plates to secure the bag during robot motion as well as maintain the bag shape, resulting in higher quality pallet builds.
Depending on the required throughputs, the robotic end of arm tool can also be fitted with mechanisms to place empty pallets beneath the first layer of bags and to put slip sheets between layers of bags, automating the complete the pallet build process.
See this process in action below.
Complementary Material Handling Equipment
While the robotic bag palletizer automates the process of putting the bag on the pallet, a variety of automation can support upstream and downstream operations.
Upstream Automation
Upstream of the bag palletizing cell, it is very common to have conveyance to transport the bags from the filler to the palletizing area as well as several quality checks that ensure product going out the door meets all necessary requirements. Bag conveyance systems can be as simple as a few sections of belted, AC-driven bag conveyor all the way to complex conveyor lines that feature spirals or vertical lifts to change elevations.
Quality checks often include a weight check to ensure the bag is filled to the required level and a metal detector to ensure that no metal foreign objects have entered the bag. These quality checks can be paired with mechanisms to reject failed bags to a conveyor lane, effectively removing the failed bag from the product flow, while allowing the line to continue to run.
Prior to being palletized, bags are typically run through a bag flattening mechanism to condition the bag for palletizing. Bag flatteners can have several forms depending on the product density and bag construction, but common types are dual belted compression, square roller conveyor or vibratory conveyor.
Downstream Automation
Downstream of the bag palletizer, there are many configurations of automation depending on your requirements. These automated solutions can be as simple as conveying out a palletized load of bags for forklift pickup to complex systems that produce a pallet load that is wrapped, labeled and double stacked.
It is very common for robotic bag palletizers to feed an automated stretch wrapping system that applies stretch film around the pallet load after palletizing. This close coupling of automated palletizing & stretch wrapping ensures that the pallet load stability and quality is maintained allowing for better pallet loads to be moved throughout a facility and eventually shipped to end users.
If your bags do not lend themselves to quality pallet load builds either due to the geometry of the bag or the height of the pallet load, robotic palletizing cells can be designed so the robot places bags onto a pallet that sits on a turntable stretch wrapper. This turntable stretch wrapper will incrementally wrap the pallet load as the robot progresses through the pallet build sequence. This eliminates the need for an unwrapped pallet load of bags to be conveyed throughout the system.
Expert Advice for Palletizing Bags, Totes, Tires and More
Having an unwieldy product – due to size, weight or geometry – can make even manual palletizing operations tricky. Trying to automate that process may seem more daunting, but Bastian Solutions is heavily experienced in robotic palletizing systems, and bags are no exception. Having supplied various bag palletizing solutions to customers across several industries, our experts can support the application analysis for your project to determine what end of arm tool and supporting upstream and downstream equipment make the most sense for your business needs. Robotic palletizing, with the right end of arm tool, offers a tried-and-true automation solution resulting in higher line uptimes and greater throughputs. Contact our team today and discuss how we can help you accomplish your goals!
Trent is a field application engineer with the robotics group of Bastian Solutions in St. Louis, MO. He has a Bachelor of Science degree in Industrial & Manufacturing Systems Engineering from the University of Missouri – Columbia. As a field application engineer, his duties include working with clients to determine their material handling needs and developing layouts for robotic systems.
Comments
No comments have been posted to this Blog Post
Leave a Reply
Your email address will not be published.
Comment
Thank you for your comment.