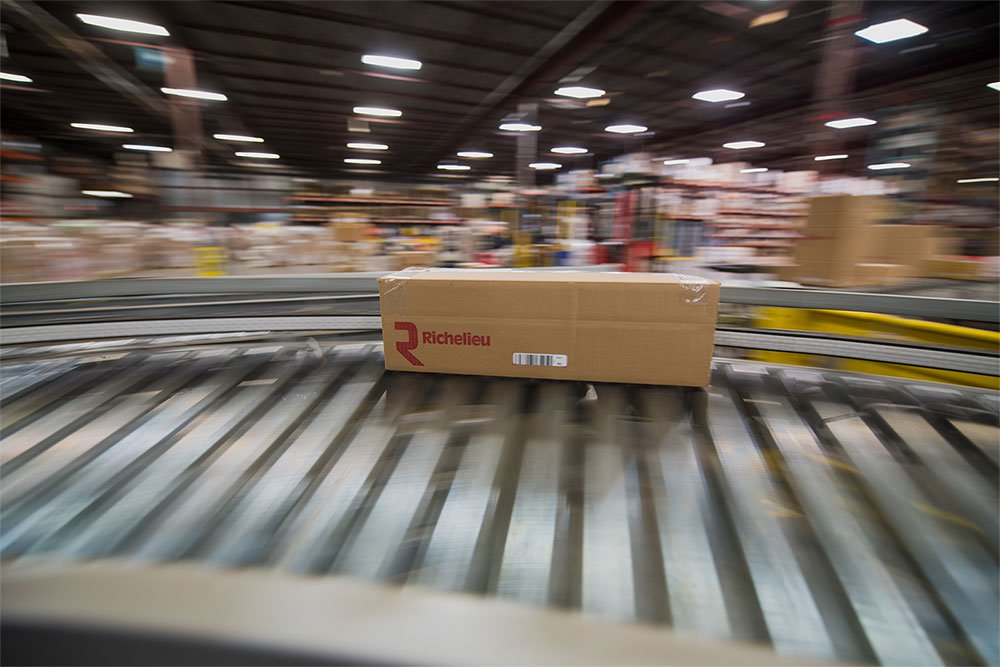
Richelieu Streamlines Order Fulfillment for Improved Customer Experience
Kevin Auger | 5 August 2021
Serving more than 80,000 customers in both Canada and the United States, Richelieu aimed to increase customer satisfaction with faster, reliable order fulfillment.
As an international importer, distributor and manufacturer of specialty hardware, Richelieu manages over 110,000 SKUs. In addition to a faster and more streamlined order fulfillment approach, Richelieu was able to consolidate external storage by leveraging their Montreal facility.
They looked to Bastian Solutions to advise and implement the right combination of automation technology to add to Richelieu’s facility longevity and implement a system that helps them reliably maintain strong customer service.
Faster Varied SKU Throughput
Richelieu’s products range from decorative hardware to sliding door systems, and as such, these products have varying sizes, weights and dimensions. This can make operations inherently complex. Looking for a goods to person automated system that handles not only a large volume of more than 100,000 SKUs, but also varying products, required creative solutions and technology combinations for more effective operations.
AutoStore’s innovative solution allowed for simplicity and fast order processing. Additionally, its complete configurability and flexibility, provided the needed volume for Richelieu’s product assortment. About 19,788 bins were added with 25 robots and four carousel ports.
Pick to light make both product picking and stock replenishment more efficient using visual cues, coupled with Exacta’s software for better accuracy and to keep labor costs down with optimized picking, putting and sorting.
Previously, the standard manual storage and fulfillment process could take several hours. Now, orders are picked, packed and shipped in about 10 to 12 minutes and in-store orders take 3 to 5 minutes to fill.
AutoStore and pick to light are easy to learn systems with the flexibility to operate individually or together. They made way for faster, visible benefits soon after implementation. In total, the primary technologies implemented in this project included:
Additional features were added to help make processing even more efficient including - semi-automatic case sealers, in-line scales, and a print and apply automated labeler.
Optimized Operation Movement
Inefficient product and operator movement adds time to the overall fulfillment process. Developing efficiencies by reducing travel time can save minutes or even hours.
Previously, manual storage and fulfillment processes required Richelieu operators to walk between mezzanines and racking to select and pick fulfillment orders. A combination of AutoStore and the sortation conveyor, created dedicated operator stations where the products are sorted and delivered to each operator. Not only did this reduce the operator’s travel time to and from the product, but it also created efficiencies in picking. Operators can pick more frequently and for longer periods.
Defined Workstations
In light of COVID-19 social distancing requirements, the goods to person system layout allowed for Richelieu to continue delivering orders on time despite required spacing and personnel adjustments. The naturally dedicated workstations meant that spacing requirements were met with already spaced workstations, and easier planning and tracking of personnel shift hours. Additionally, the reduced travel throughout the distribution center helped to simplify any needed contact tracing.
HMI Assist
The Human Machine Interface (HMI) further assists in work productivity and optimizing movement throughout the operation by providing easy access to real-time data. This data includes system status, sortation statistics, and live monitoring.
Simplicity for Easy Growth
Since the implementation of the automation system, ever increasing business demands initiated two expansions for Richelieu’s facility. AutoStore’s modular systems makes for fast and easy growth during full operation, without interrupting activities. “It’s a system that is easy to grow, to up size. So, we can add robots if we have more lines. If we have a new product, we add bins. And, you can add the part you want without stopping the system,” says Stephane Bourque, Distribution Director at Richelieu. During the expansions, two pick ports were added to further increase pick rates and 4,000 bins were added to accommodate increased product volume.
Maximum system uptime
As seamless as expansion is for this system, maintenance is also fast and easy. The simplicity of the system means that there are fewer components to maintain and repair. As a whole, AutoStore requires minimal maintenance and downtime with seasonal changes that can be automatically adjusted. In general, it features a minimum 98% system availability.
Modernizing Existing Resources
Finding solutions that solve today’s challenges and make room for tomorrow’s growth is no easy feat. “With any implementation there are always challenges, but Bastian Solutions really stuck with us. I enjoyed working with people who had the expertise and were willing to do what it took to get the project going,” says Stephane.
With focus not only on speed, together Bastian Solutions and Richelieu were able to maximize storage space of an existing facility to ultimately make throughput more efficient and bring reliability to the company’s operations.
Kevin Auger is a Canada Country Sales Manager at Bastian Solutions based in Montreal, Quebec, Canada. Featuring a background in engineering, Kevin has a Baccalauréat en génie de production automatisé from Université du Québec - Ecole de Technologie supérieure and a Diplôme d'étude collegial in industrial electronics from Cégep de l'Abitibi-Témiscamingue.
-
Kevin Auger est un directeur des ventes chez Bastian Solutions et travaille à Montréal, dans la province de Québec au Canada. Kevin possède de l’expérience en ingénierie et un Baccalauréat en génie de production automatisé de l’Université du Québec – École de Technologie supérieure, ainsi qu’un Diplôme d’études collégial en Électronique industrielle Du Cégep de l’Abitibi-Témiscamingue.
Comments
No comments have been posted to this Blog Post
Leave a Reply
Your email address will not be published.
Comment
Thank you for your comment.