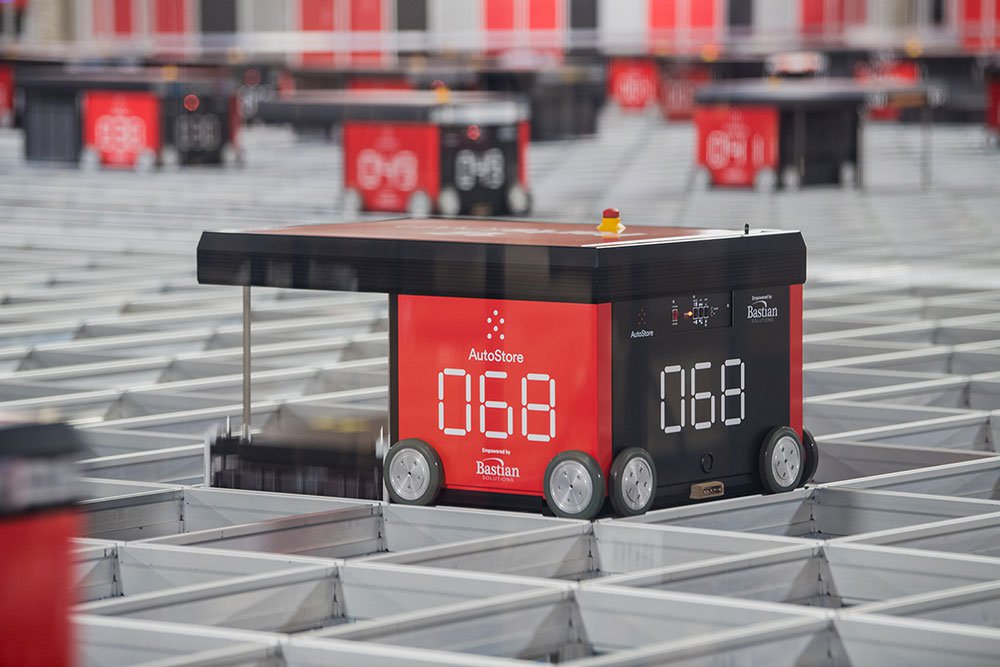
Product Storage & Retrieval: Goods-to-Person and Traditional Shuttle Systems
Jason Blackney | 4 December 2024
Every movement within a distribution center or warehouse, from picking to replenishment, impacts the bottom line. Implementing a goods-to-person (GTP) system is one way to optimize these movements, reducing the time spent searching for items and improving overall accuracy.
Two of the most widely used GTP solutions are AutoStore and traditional shuttle systems. While both streamline storage and retrieval processes, they operate in ways that can lead to different outcomes for your operation. Choosing the right one can affect everything from storage density to system flexibility and long-term scalability.
Understanding the key differences between AutoStore and shuttle systems is essential to finding the best fit for your warehouse.
Infrastructure: Conveyor Requirements and System Footprint
One of the most significant differences between AutoStore and traditional shuttle systems is the required conveyor equipment. Shuttle systems depend heavily on a complex network of conveyors to move totes between storage areas and pick stations. These systems require dedicated aisles for the shuttles to travel along; the conveyors can take up significant space in many cases. This increases the initial setup costs and adds to the ongoing maintenance requirements as every part of that conveyor system needs to stay operational to avoid bottlenecks.
AutoStore operates with much less conveyor infrastructure. Its pick stations are directly attached to the grid where the products are stored, meaning there’s no need for extensive conveyor systems to shuttle goods back and forth. Each AutoStore robot can move totes within the grid and deliver them directly to the attached pick stations, drastically simplifying the system’s overall footprint.
Additionally, AutoStore’s design eliminates the need for aisles. Totes are densely stacked within the grid, and the robots move across the top of the storage system to retrieve them. This creates a much more space-efficient setup than shuttle systems, which must reserve aisle space for shuttles to travel up and down.
Redundancy and System Reliability
One of the standout features for the AutoStore system is its built-in redundancy. Each robot in the system operates independently, allowing for high flexibility and fault tolerance. If one robot experiences an issue, it can be taken offline while the others continue operating without interruption. This design reduces the risk of a single point of failure, ensuring that your operation can keep moving smoothly, even during maintenance or unexpected breakdowns.
Shuttle systems use centralized lifts to move goods between storage levels and conveyors. While these lifts are efficient when functioning correctly, they can create significant vulnerabilities. If a lift goes down, it halts movement for the shuttles for that entire aisle, directly impacting throughput. This dependency on a single lift means a failure could require immediate repairs, resulting in downtime and delayed orders.
Flexibility and Expansion
When it comes to flexibility and future growth, AutoStore stands out for its modular design. Expanding storage capacity or adding additional pick stations is a relatively simple process that doesn’t require major system overhauls. AutoStore’s grid can be extended, and new robots or pick stations can be integrated without disrupting ongoing operations. This makes it an ideal solution for companies looking to scale their operations over time.
Shuttle systems can be more challenging to expand. While it’s possible to add more storage racks, the real complexity lies in the conveyor infrastructure. Expanding the system often means redesigning the conveyor layout and reprogramming the warehouse control software to accommodate new zones and routes. This can lead to significant downtime during installation and increased operational complexity.
Choosing between AutoStore and shuttle systems depends mainly on your operation's flexibility needs. If you anticipate future growth and need a system that can easily adapt to changing requirements, AutoStore offers a seamless path to expansion.
Throughput and Order Picking Efficiency
When evaluating throughput and order picking efficiency, AutoStore and shuttle systems each have their strengths, but they differ significantly in how they achieve results. AutoStore excels in handling high volumes of discrete order picking. Its robots can retrieve any tote from the grid and deliver it to any pick station, which allows for more flexibility and faster processing of orders across multiple stations. This ability to route totes to any pick station simplifies the picking process and increases efficiency, especially for operations handling diverse product lines or fluctuating demand.
Shuttle systems are designed to deliver totes to pick stations at high speed. Shuttles move along dedicated aisles, quickly retrieving totes and sending them to the conveyor system for processing. While this can result in faster delivery to the pick stations, the complexity arises with downstream sortation. Shuttles often require additional sorting and routing systems to get the right tote to the right pick station, adding extra steps and slowing down the overall process.
AutoStore tends to outperform Shuttle systems in high throughput—fast, continuous order processing when considering order turn time. Since AutoStore eliminates the need for additional downstream sortation and allows any robot to bring totes to any pick station, it reduces delays and keeps the picking process moving smoothly. This advantage makes AutoStore a better fit for operations requiring a high volume of orders with minimal interruptions. In contrast, Shuttle systems may be more suited for operations focused on large batch orders where speed to the pick station is the top priority.
Replenishment and Top-Off Capabilities
AutoStore offers an advantage with its ability to perform top-off replenishment. This process allows a bin that already contains items—say, a tote with two red shirts—to be easily retrieved and brought to a replenishment station where more items can be added, all without disrupting the overall operation. The system’s flexibility in routing any tote to any replenishment station simplifies the process and eliminates the need for labor-intensive compaction steps, making it more efficient.
Choosing the Right Goods-to-Person System for Your Operation
When selecting the best goods-to-person system for your operation, understanding the key differences between AutoStore and shuttle systems is critical. Here’s a quick recap of the main distinctions:
- Infrastructure: AutoStore requires minimal conveyor systems and offers a smaller footprint with dense storage, while shuttle systems rely heavily on complex conveyor networks and aisles.
- Redundancy and Reliability: AutoStore’s independent robots provide built-in redundancy, minimizing downtime, whereas shuttle systems depend on centralized lifts, which can become a bottleneck if a failure occurs.
- Flexibility and Expansion: AutoStore’s modular design allows for seamless expansion, making it easy to scale, while shuttle systems require more intricate planning and resources to expand.
- Throughput and Efficiency: AutoStore excels in fast, continuous order picking, especially for diverse product lines. Shuttle systems may offer quicker delivery to pick stations but can be slowed by downstream sorting.
- Replenishment: AutoStore’s top-off replenishment simplifies the process and reduces labor, while shuttle systems rely on compaction, adding extra steps and time.
Choosing between these systems depends on your facility’s unique requirements, such as space constraints, order volumes, and flexibility. Bastian Solutions can help analyze your needs and determine the right solution for your operation, ensuring maximum efficiency and productivity. Contact our team today to explore which goods-to-person system fits your future growth plans.
Jason is a Solutions Account Executive in System Sales at Bastian Solutions, based in Carmel, Indiana. He is University of Wisconsin - Madison BSIE grad. He has extensive experience in all facets of the material handling industry including engineering as an end user, an operational leader in a high-volume ecommerce fulfillment center and leading solutions engineering as an integrator. With Jason's well rounded MHE experience, he is constantly focused on delivering solutions for customers that solve their biggest challenges for the best value.
Comments
No comments have been posted to this Blog Post
Leave a Reply
Your email address will not be published.
Comment
Thank you for your comment.