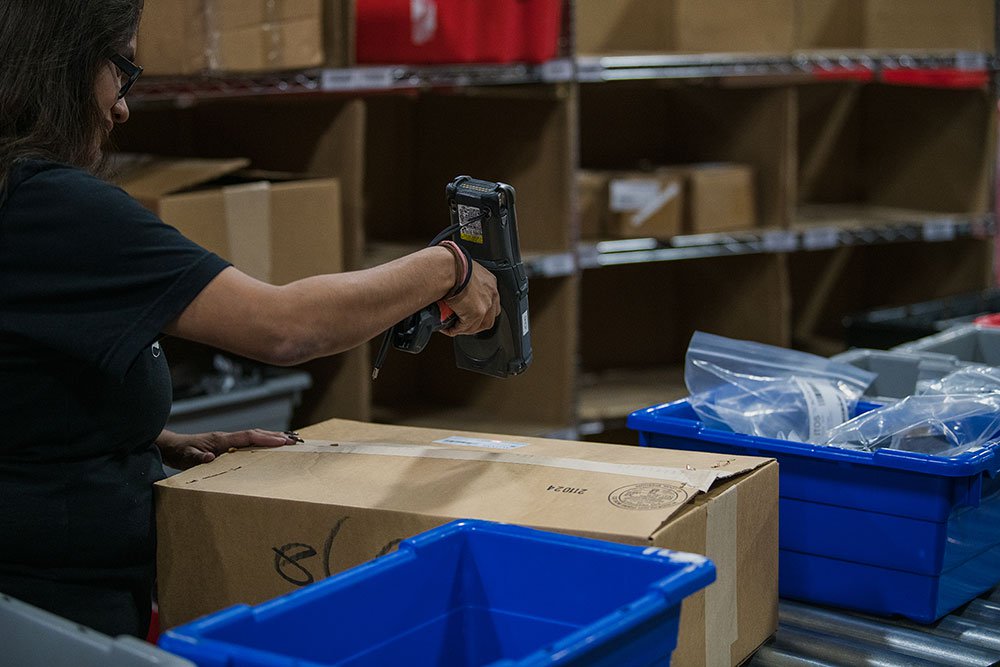
Planning for Warehouse Automation: Where to Begin?
Matthew Theriault-Thompson | 13 November 2024
“Let’s look at this thing from a standpoint of status. What do we got on the spacecraft that’s good? “ –Gene Kranz (Ed Harris), “Apollo 13.”
There’s a lot of genius in that simple question.
If you haven’t watched the movie, it’s worth a few hours of your time.
The quick summary is that the mission was in serious trouble, Gene Kranz had just put on the flight director vest, and he was beginning the process of recovering not just the equipment, but most importantly, the crew of the Apollo 13 spacecraft.
The genius in the question is recognizing that you have no ability to reach an endpoint if you don’t know where you are at the beginning.
While it’s not quite as riveting, automating your warehouse CAN feel as daunting as the task facing NASA Flight Director Kranz so many decades ago. And, while a mission crew’s life is not at stake, should something go wrong, the threat to production and career can be very real.
Let’s take a look at some helpful guidelines, information and ideas to help minimize the threat of something going wrong as you look to automate your facility. While some details may not fit all industries, much of what I discuss can be universally applied. Keep an eye out on future posts for even more information.
Let’s start at the beginning…
For clarity of “status”, you’ll need to do the following:
- Assemble your tools.
- Go to where the work happens.
- Document the steps.
- Talk with your operators and front line employees.
Set the Stage for Automation Success
To set the state for your automation success, let’s break these down further.
1. Assemble Your Tools
Take an account of the tools at your disposal and the data that is being generated. Looking at time stamps in your WMS is only going to tell you a part of the story, so you’ll want to dig deeper.
While there are many data analytics applications and services, including AI, in this situation, the simplest tools like a cell phone camera, a pen, a notepad, and a spreadsheet can be incredibly helpful. They’ll also be easily distributed among your operations supervisors and managers who will be instrumental in helping gather information and begin truly understanding what’s happening in your warehouse.
2. Go to Where the Work Happens
The data analysis is important, but it has its shortcomings. If you’re looking at time stamps between two stages, and they all show about 10 minutes, it’s easy to assume that 10 minutes is about how long that step should take. But what may not be accounted for is that the workers may constantly require additional time to sift through disorganization or move around obstacles within the warehouse (for instance, between receiving and putaway). It’s hard to see those obstacles, frustrations, or additional effort in the software. However, you can see it when you go to where the work happens. By going and seeing for yourself, you gain a better understanding of what IS happening, so you can better form a plan for what SHOULD happen.
3. Document the Steps
Use your camera to document – photograph or video record movements and operations. For example, you could record a truck unload and pallet staging, record the receiving of a pallet and document processing, or record the putaway process.
Do this multiple times with different operators. The videos will tell you exactly what the process currently looks like, how long it takes and will highlight specific areas in need of immediate improvements. Document the step’s time and description as well as any additional notes in your spreadsheet. Then when you see a process taking 10 minutes, for example, you’ll not only know if that timing is valid, but you’ll understand why.
4. Talk with Your Operators and Front Line Employees
This one can’t be overstated enough. The employees who are working in the process day in and day out have ideas and insights that you may have never considered, despite an operation walk-through. Your employees know which days are really bad and the factors that make for a tough day, often the moment they enter their workspace. They have ideas for improvement not just in speed and efficiency but also in ergonomics. They know their physical aches and pains from the work, and if they trust you, will share that information. Most importantly, when you go to implement changes to those processes, if you’ve listened to them, the “buy in” becomes much easier and change adoption can happen much more smoothly.
Finding the Right Moment to Automate
“After 30 years in business, we’re finally at a point where we can automate.”
I had the privilege of participating in a panel in September, and during the Q&A, one of the attendees made the above statement. It’s unfortunate that so many years and opportunities passed before they felt comfortable to automate.
My response was that automation doesn’t always have to be a big, multi-million-dollar innovation projects. You can find ways to automate in smaller steps. The Japanese word “kaizen” means “continuous improvement” through small, incremental changes. The belief is that cumulatively and over time these small steps yield big returns. These steps can lead to more revenue and efficiency that can then be used to justify larger system innovations, potentially much sooner than what could have been afforded otherwise.
By first taking the time to understand “status”—where each step in your process stands in terms of time and function—you can more easily identify smaller automation opportunities. These changes can quickly add up to improvements in efficiency, process flow, and worker quality of life.
While you may not have the same worldwide fanfare upon the safe return of the astronaut crew as seen in Apollo 13, by using some of the steps above to “start from status”, you’ll be able to experience the success of automation deployment you’re looking for.
These principles and lessons learned, common to all projects, will help lead to success regardless of the industry or project. Let’s discuss today how we can help you find your “status” and set the stage for your success.
Matthew is a New Business Development Consultant for Bastian Solutions.
Comments
No comments have been posted to this Blog Post
Leave a Reply
Your email address will not be published.
Comment
Thank you for your comment.