.jpg)
Multi-Site Project Implementations: Consistency Drives Efficiency
Kyle McCarty | 18 November 2020
As the global effects of COVID-19 continue to play out, demand for contactless shopping via eCommerce is increasing putting pressure on fulfillment. Businesses are scrambling to identify opportunities to increase supply across their distribution networks. Many are seeking support from automation systems integrators (conveyor, robotics, software, controls) across several fulfillment sites at once. While multi-site implementations can be challenging, when executed successfully they can achieve greater results than single-site implementations.
Similar or identical automation designs across multiple sites can help businesses by providing efficiencies in business operational standards and training, streamlined support, and common spare parts - a classic case of economics of scale.
Businesses can tackle multi-site challenges and achieve these economies of scale by focusing on three key things during system implementation:
- Clear roles & responsibilities
- Transparent communication
- Local support system understanding
1. Roles & Responsibilities
Multi-site implementations are like a dance between business and system integrator. Without clear delineation of roles and responsibilities it can be difficult to understand who will lead and where the next step will be. Assigning teams and specific tasks ensures no one steps on each other’s toes the customer comes out smiling!
Here’s a diagram outlining these roles & responsibilities:
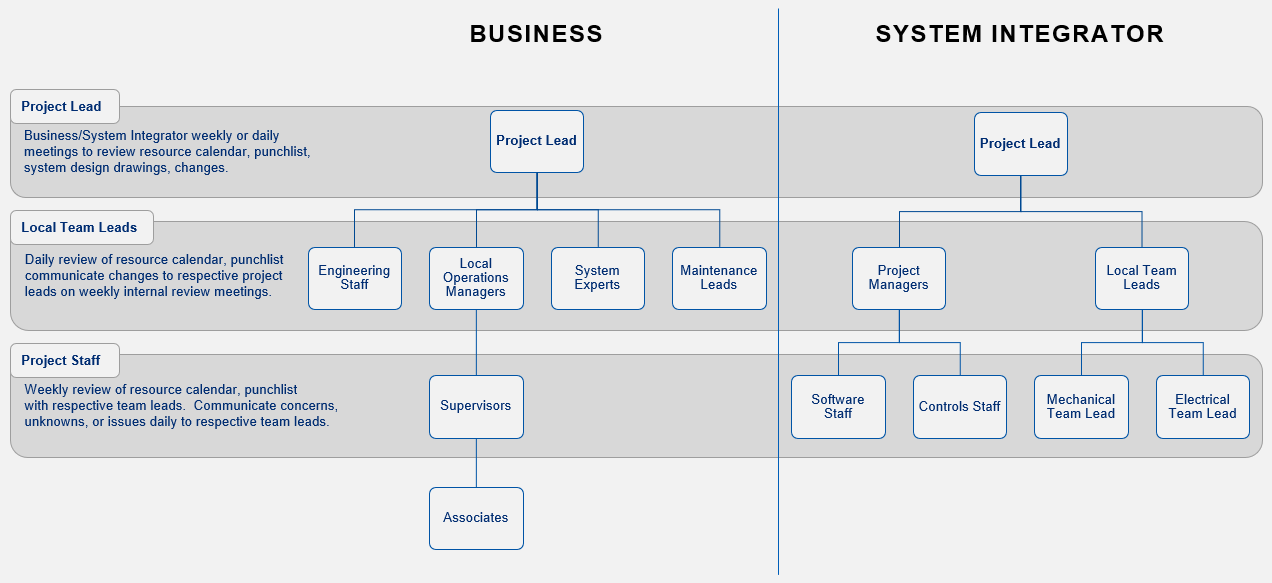
Figure 1: Business and System Integrator Roles & Responsibilities
2. Business / System Integrator Communication:
Communication between the business and the system integrator is paramount. Both teams, at all levels, need to be aware of the project status. Both teams need to know tasks to be completed and which resources are on site so surprises can be avoided during project implementations.
Here’s a description of different roles and typical communication on both sides.
- Two project leads, one for the business and one for the system integrator, take ownership of the implementation of the project scope across all sites. The two leaders work remotely to guide their respective project teams across all sites ensuring consistency across designs, installation, training, go-live, and support.
- Setup weekly or daily meetings between project leads.
- Reference a multi-site resource calendar to quickly understand which teams are on site at which sites and status of tasks to complete.
- Reference a multi-site punchlist to have visibility to issues at one site that may need to be resolved at other sites as well.
- Local resources for both business and system integrator provide on-site support, local project ownership and responsibility, and knowledge of the system for installation and support after go-live.
- Setup weekly meetings for the project leads to check in on the local teams to be sure communication is thorough. While project leads may not be on site, they still need to have a clear understanding of the project status.
- Project staff should reference standard documentation across all sites: system training and start up, typical troubleshooting, preventative maintenance, and user manuals.
|
 |
|
Figure 2: System Education for Local Project Teams
3. System Understanding:
Multi-site installations enable the economies of scale throughout the project lifecycle, but only if knowledge gained from one site implementation is passed along to the next site implementation.
Here are some opportunities for gaining system knowledge and applying it to multi-site implementations throughout the lifecycle of the projects:
Early Project Lifecycle (System Design and Project Setup) – Gain Knowledge:
- Consistent project leads and project managers (operations, software, controls) across multiple site implementations minimizes repeat mistakes. Lessons learned are carried over site to site.
- Local resources travel to existing sites prior to the start of the local project enabling hands-on reviews of sites already in operation with equipment similar to what the local project teams will soon be responsible for.
Mid Project Lifecycle (Installation) – Apply Knowledge:
- Videos, pictures, and measurements from existing sites for installation teams and local resources to reference during project implementation.
- Project leads travel to sites for key milestones to review installation, testing, and go-live progress.
Late Project Lifecycle (Testing, Go-Live, and Support) – Pass Along Knowledge:
- The business maintenance team training can be done at one time at a central site with experts and technicians from the system integrator rather than having multiple trainings across the network.
- For the system integrator, the local team gained valuable experience with the system during the installation phase and can now serve as on-site support as needed after go-live.
- Remote support provided by the system integrator recognizes that all systems operate the same or very similar and troubleshooting can be done at all sites more easily.
EXTRA! Common Spare Parts:
- All sites have essential spare parts on hand. It is not necessary to have full spare parts list available for immediate replacement. Some sites can have specialty items and if needed at another site, the parts can quickly be shipped overnight to have the site up and running while a replacement is sourced.
- Troubleshooting and part replacement procedures can be shared within the business maintenance network. If a certain site has a part failure and a recognizes the replacement as a critical part to have on-hand, it can be recommended to every site to order for inventory on-hand.
As you can see, there are key benefits to opting for multi-site implementations. Communication is key and understanding of your system will come easier when each system acts alike. Bastian Solutions has successfully implemented many multi-site projects and would love to help plan the next step in your supply chain network.
Kyle is a Senior Field Applications Engineer with Bastian Solutions based in California. He has a Bachelor of Science degree in Mechanical Engineering from the University of Southern California. Since starting with Bastian in 2012, Kyle has been based in both the Atlanta and Los Angeles regions. He’s developed strong relationships with his clients, designing and implementing material handling solutions.
Comments
No comments have been posted to this Blog Post
Leave a Reply
Your email address will not be published.
Comment
Thank you for your comment.