Machine Tending Robots: The Importance of Part Positioning
Steven Hogg | 10 February 2016
One of the key aspects of a robotic machine tending system is part positioning. It is critical during the design process to understand the interface between the part, machine center, and robot. The fixture design within the machine center will drive requirements within the work cell. This is because you want to avoid having the robot grip the part near the position where the fixture may be locating or gripping the part.
These fixtures are typically where finished parts are produced, so the design is often focused entirely on holding the part for that process and doesn’t consider how a robot might interact with the fixture. Many times the fixture will have a tight tolerance with regard to part positioning to ensure the machining process is producing consistent parts. In this scenario, the interaction of the robotic End of Arm Tool with the machine fixtures becomes even more critical to the machining process.
In some instances, parts may be delivered to a robot on pallets or “pucks”, typically aluminum bases with fixtures bolted to the top. For the robot to interact with these pallets, the pallet must be positively located in a precise position. This is often achieved with a lift-and-locate device on the conveyor that is conveying the pallets. In a fixture pallet design, the tolerance is reduced which allows the robot to pick the part with high repeatability. If parts are conveyed in, they must either be positioned into a fixture to be positively located, or vision is required to find the part for an accurate pick.
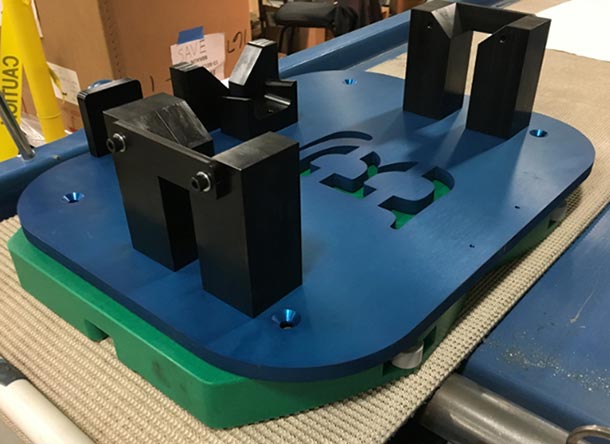
If parts are manually loaded into the system, orientation variability can occur between the part and EoAT during the initial pick sequence. Depending on the application and the amount of tolerance required, the robot may need to utilize a re-grip stand to re-orient the part for the EoAT into a fixed position. Typically, the re-grip stand will have guide pins and machined blocks integrated into the design to locate the parts to achieve a repeatable orientation.
One method Bastian Robotics uses to help protect the positioning stand that is contacting the part is the use of black oxide. Black oxide can provide corrosion protection to the surface of the metal and prolong the service life of the station. This process also provides dimensional stability to the fixture. Since the process is converting the surface metal to an iron oxide, there is almost no measurable increase in the critical dimensions which provides repeatable positioning. This process helps make the station suitable for corrosive and high-temperature environments typically found in machine tending applications.
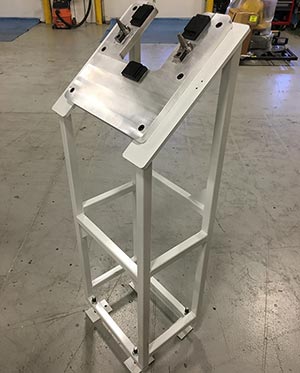
Another method to increase the longevity of the part position station is aluminum anodizing. This process increases the durability of the aluminum by providing a protective layer that is more resistant to wear. Additional benefits of aluminum anodizing include corrosion resistance, lasting color, and strength.
Interested in machine tending robots or automating your machining process? Contact our team today to learn more.
Steven is the Applications Manager for Robotics at Bastian Solutions. He helps lead the robotics automation solutions for picking, packing, palletizing, machine tending, turnkey options and more. He has a Bachelor of Science in Industrial and Manufacturing Systems Engineering from the University of Missouri-Columbia.
Comments
1SU41015 says:
8/28/2018 10:09 AM
Thanks, Valuable information!
Leave a Reply
Your email address will not be published.
Comment
Thank you for your comment.