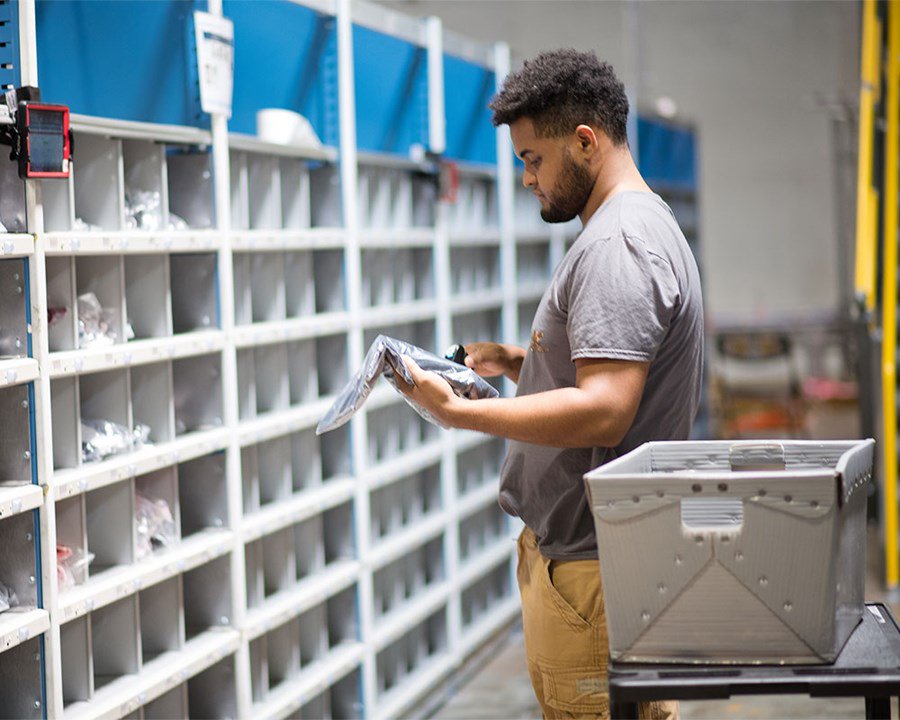
Leveraging 3 Common Put Wall Drawbacks for Improved Order Fulfillment
John Padgett | 21 July 2021
Put walls aren’t new but their many operational benefits continue to stand out and help drive distribution center efficiencies, despite some common drawbacks.
For companies with high order commonality and batch picking, put walls can easily have a dramatic impact to picking labor. Put walls are simply shelving units with several cubbies of the same or varying sizes, dependent on the orders being processed. Modern units have light indicators at the front and back of the wall to help direct operators to pick and put items.
The picking is done upstream of the wall where pickers pick in batches at the SKU level or in picking zones throughout the warehouse. These items are picked into a container and delivered to the induction side of the put wall where another operator scans either the container or each individual item and places it into the corresponding cubby location. Once all items for the order are consolidated in the cubby, another operator takes the contents and packs the order to be shipped out of the facility.
This paperless fulfillment approach is scalable, efficient and a widely accepted solution to solving picking capacity labor shortages. It reduces what would normally be 10 trips to the storage location, for example, to a single one. For manual order fulfillment solutions this means less walking and more ergonomic options. For automated solutions it consolidates inventory bin presentations that the system needs to perform.
At its core, a put wall is fairly straightforward but to maximize the best use of this type of technology it’s important to understand and take into consideration the limitations. There might be opportunities that you may be able to leverage for even greater efficiency.
Top 3 Put Wall Drawbacks
#1 Order Characteristics
Single line, single piece orders can have a negative effect on a put wall system.
For orders that only have a single unit, the double touch aspect creates more labor than just picking it into a shipping container. Also, these types of orders can quickly fill up a put wall and throw off the balance between the operators putting at the front of the wall and the operators packing behind the wall.
To confront this problem, most warehouse execution systems (WES) will segregate order types like these from multi-line orders and have them processed outside of the put wall. Leveraging the WES to manage these situations still allows for similar orders to be batch picked while eliminating some of the volume capacity needed in the wall and reduces the number of touches needed to complete these types of orders.
#2 Wave Management and Batching
Wave management and batching can also be a challenge with these systems. The key to running a put wall system efficiently is to make sure that there is balance between picking, putting and packing operations. Making sure that the walls are turned appropriately helps to keep the operations running smoothly.
If picking gets ahead of the put walls, it can create a backup that leaves operators waiting on the put walls to catch up. Similarly, if a single picking zone gets behind the wall can become locked up with orders that are missing an item from that zone.
To address these scenarios, physical accommodations can be added to serve as buffers that hold picked containers to decouple the processes and give the operation more flexibility.
#3 Sizing Constraints
Sizing a put wall is an important first step and one that will determine overall system efficiency and capacity.
In general, picking efficiency increases with the higher number of orders that can be batched together at one time. It is important, however, to consider that the larger the batch size, the longer it takes to process a single batch. This can have impacts to the system’s ability to complete work by certain cutoff times.
The physical size of the cubbies should also be consider as having a single size may make the wall more flexible but could decrease the number of potential of locations that can fit in a given space. Understanding the variations in order characteristics and changes in future fulfillment needs is key to sizing this type of solution.
Refining the Right Solution for the Task
Put walls play a key role in order fulfillment and they have the potential to reduce picking labor and streamline the operational flow through a warehouse.
Understanding the right circumstances in which to implement put walls is key to ensuring a smooth and sustainable operation. Let one of our many skilled warehousing consultants guide you through the process of determining the right solution for you and your organization.
John Padgett is a Solutions Account Executive based out of Bastian Solutions’ Indianapolis, Indiana office. He has an MBA from Butler University and BSME from Purdue University. John works with clients on the requirement analysis, design, budgeting, proposal, and implementation of larger integrated material handling systems. He guides projects throughout every phase of a project, from solutions development to support after installation.
Comments
No comments have been posted to this Blog Post
Leave a Reply
Your email address will not be published.
Comment
Thank you for your comment.