Is it Time to Automate Your Machine Tending?
Michael Cunningham | 18 July 2017
Is it time to automate your machine tending process? With the consistent growth in the automotive and aerospace industries, the mechanical components that contribute to these industries are in high demand. Factories are expanding, hiring more workers, and adding more shifts in order to meet the high production rates required.
With all this growth, site supervisors are constantly identifying certain processes in their production, and asking themselves “can I automate this?” While that that can be a difficult question to answer without a detailed look at the process, this guide will help you get a better understanding on whether that answer is “most likely,” “unlikely,” or “partially.” That way, when you reach out to a system integrator, such as Bastian Solutions, you will not be too surprised with what answers you get.
Handling Product
One of the first things you need to look at is how an operator handles the product through the various machine processes. Is the operator simply grabbing the product wherever it is convenient for them and placing them into the machines with little effort, or, does the operator have to jiggle or press the product with excessive force to get it into place just right? If it’s the former, then you have taken your first step into identifying a potentially automated process. If it’s the later, you will need to look into more detail as to why it’s not a simple placement.
Is it a worn out fixture that needs replacing, or could it be a tolerance issue? The next thing you need to analyze is how many unique product types get handled in the process. If there are a lot of unique products, is there perhaps a common surface amongst them that a robotic end of arm tool (EoAT) could engage for a secure grip?
Most machine tending EoATs have multiple grippers that allow the robot to exchange finished products with unfinished products right at the machine in order to reduce cycle time. This leaves little to no additional room on the EoAT for additional, unique grippers. If you have unique product types with uncommon surfaces of engagement, you may need to have multiple EoATs for the automated system. This drives up costs and requires additional time needed for tool change-over. 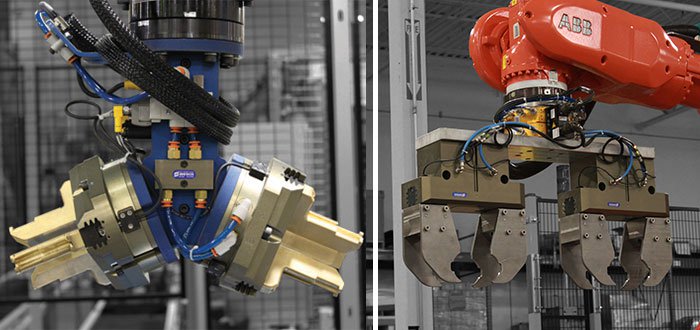
Product Infeed
There are numerous ways to infeed product to the robot. But the three most common ones you see are:
- Conveyor with justifier
- This type of infeed has an operator placing product onto one side of the conveyor, outside the cell. On the other side of the conveyor, inside the cell, is a device (typically a pneumatic actuator) that will push the product to the side of the conveyor, corner justifying the product for robot pickup. This is typically the most cost effective solution of the three common product infeed types.
- Conveyor with vision
- This type of infeed functions in a very similar fashion to the one above. However, instead of a justifying device, there is an overhead vision system that scans the orientation of the product. The vision system then tells the robot where the product is, and the robot adjusts itself accordingly in order to pick the product.
Vision systems are typically mounted above the conveyor, or on the robot’s end of arm tool. This type of solution is best used for when you need to accumulate a lot of products, but are unable to easily corner justify the product due to a complicated design. It is also a good solution for when you have multiple, unique product types that the system needs to handle.
- Fixture Conveyor
- This type of infeed falls into two subcategories: slat conveyor and puck conveyor. Slat conveyor will have custom fixtures mounted on each slat of the conveyor, where the product can be mounted on those fixtures. Puck conveyor consists of a series of pucks (also called pallets) that ride on top of a conveyor. Each puck has static fixtures that hold product. Fixture conveyor is best for when you have a product that is not easily conveyable with standard belted or roller type conveyor.
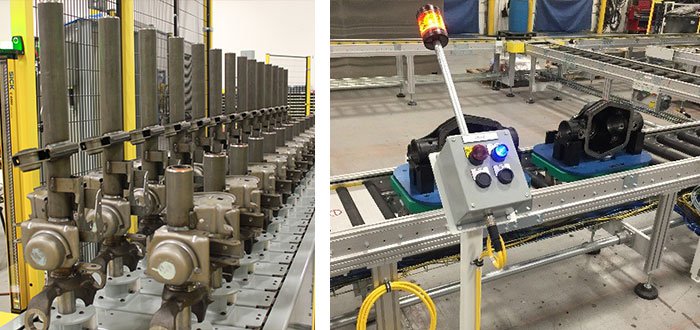
Environmental Factors
Luckily, with modern technology, typical manufacturing environments won’t play too much of a factor in whether or not you can automate the process. However, the manufacturing environment will be huge factor in terms of cost to automate. Is the environment extremely dirty, dusty, or have potential corrosion factors that come into play? If so, you will most likely need a more expensive foundry-grade robot. Is it a hot environment (i.e. products are in a furnace)? You will probably need to add an insulation skirt to the robot. The list goes on, but your systems integrator should be well-versed in what products work best for your unique environments.
Machines Used
Most modern CNC machines have the ability to be easily integrated into an automated system (typically it’s just a software package). However, many factories have CNC machines that are extremely outdated that are still used in production. When this is the case, a trick that is typically done is wiring the main I/O on the CNC machine to an Ethernet adaptor block, then running an Ethernet cable from the block back to the control panel. This process may require a little more system commissioning time in the field, but gets the job done for most situations.
Pre/Post Product Processes
Many machine tending processes involve the operator having additional duties besides moving product from one machine to another. The two most common additional processes are deburring products and inspecting finished products for major flaws. With modern technology, these additional processes can also be automated a majority of the time. Keep in mind, that the more unique product types you plan to run in the system, more cost is added to the system, as each unique product type has to be programmed and tested. More and more, robotic deburring is becoming a popular application the industry.
Standard robotic deburring tools and software dedicated towards robotic deburring, have made integrating a deburring process into your machine tending operation pretty simple. You even can utilize your existing robot to handle the deburring process as well! The easiest way to do this is by having the deburring tool mounted to a stand/fixture. The robot will pick up the product, take it to the deburring tool, then will rotate the product around the deburring tool, before placing the product into a machine.
If rate is an issue, another deburring solution is dropping in a dedicated deburring station within your cell. The deburring station is treated like its own machine. The product-picking robot will load and unload product to and from the deburring machine, in the same way it loads and unloads the CNC machines within the cell.
Inspecting finished products for major flaws can be done using a vision system. Major flaws that can be detected include chips in the product and deep scratches. If the inspection requires looking at blemishes or small scratches to the surface finish, inspection may still be possible. However, this type of inspection would require a camera supplier, such as Cognex or Keyence, to get involved and conduct testing. The vision system can typically be mounted on the robot EoAT or be on its own fixture. The vision inspection on the robot EoAT would be a good tie in if you are already using vision to pick products from the infeed conveyor.
Return on Investment
Alas, the biggest question that needs to be answered, especially in upper management’s eyes, is what is the ROI? Most companies look to see a return on their system investment within 18-24 months. A typical machine tending cell consisting of one machine tending robot with one EoAT, tending three CNC machines, costs in the range of $250K - $400K. Sometimes ROI isn’t the only factor that determines whether or not it’s time to automate your processes.
Another major factor in justifying the automated system is operator health and safety. Is the environment that the machine tending operation takes place a dirty or corrosive environment, increasing the health risk of your employees? Is the operation in an extremely hot environment, where dehydration and heat stroke are probable? Is the operator constantly having to pick and move heavy products, increasing the possibility of physical injury? Or, do you just find that it is hard to retain operators due to a multitude of reason? If you answered “yes” to any of these questions, then it may be time to automate your system.
Michael Cunningham is a robotics inside application engineer at Bastian Solutions' St. Louis, MO office. He has a Bachelor of Science degree in Mechanical Engineering from the University of Toledo. As an inside applications engineer, Michael works with clients on the requirement analysis, design, budgeting, proposal, and implementation of robotic material handling systems.
Comments
No comments have been posted to this Blog Post
Leave a Reply
Your email address will not be published.
Comment
Thank you for your comment.