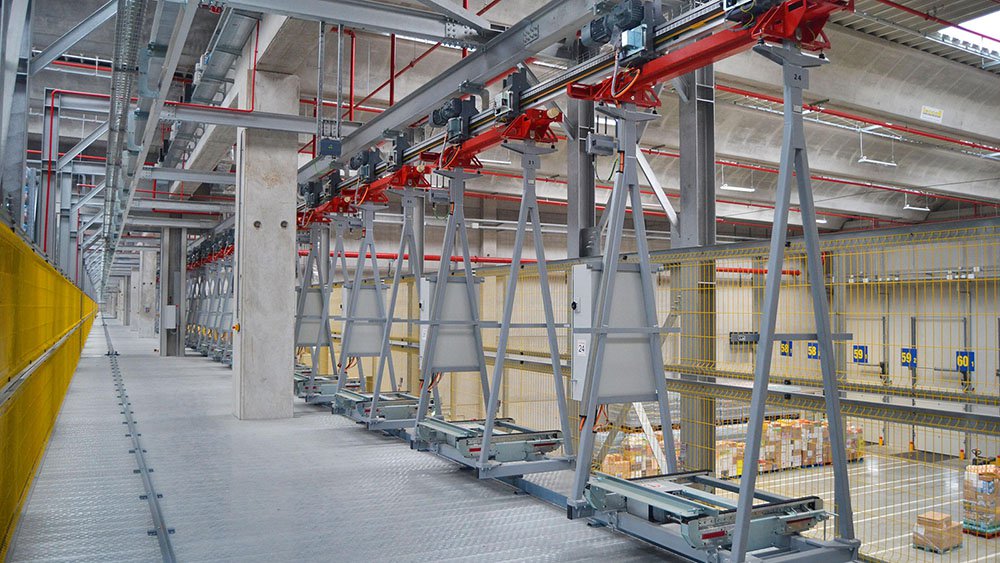
Is a Pallet Monorail System the Right Transport Solution?
Bastian Solutions | 8 September 2021
Goods to person and goods to robot solutions are trending topics when it comes to distribution fulfillment but what about heavier and larger pallet transport?
Pallet monorail systems are one of the fastest and most efficient ways to transport pallet loads throughout a facility. This technology goes by many different names including “Electrified Floor Track System (EFTS)”, “Electrified Monorail System (EMS)”, or sometimes just “Monorail.”
In the most general sense, a monorail system is comprised of two key elements:
- Track - provides guidance and power
- Trolleys - physically move the pallets along the track system; self-propelled
The scalability makes them a great investment, less than a roller conveyor system, and an option worth considering. Below we take a look at standard ways this solution can optimize your operations.
When Does a Pallet Transport Make Sense for Your Application?
A monorail system could be used within any system that features long distances of transport or accumulation pallet conveyor connecting various process steps, however, it is best suited for high-throughput applications or when there is pallet flow traveling in both directions (e.g. back and forth between process steps). This helps minimize the amount of time that a trolley may be traveling while empty. As this method of conveyance does not rely on friction or a pallet board moving along rollers or chain, it is possible to convey loads much faster than fixed conveyor.
When exactly does it make sense to integrate this type of solution?
- Connecting Different Processes – If the system includes a circuit of
pallet conveyor connecting different processes, monorail should be considered in place of the pallet conveyor. If the run of pallet conveyor is sufficiently long or the throughput is sufficiently high, a monorail system could offer significant cost improvement or functional advantages.
- Enclosed Environment is OKAY – For safety, the monorail system will need to be fully enclosed. For long runs that might NOT have extremely high throughput, adding safety enclosures could be too obstructive for the facility. An automated vehicle or forklift might be a better fit.
- High Speeds – As a general rule, we’d identify an application as good fit for monorail in place of pallet conveyor if the throughput becomes high enough that we’d need to have two separate levels of pallet conveyors to handle all of the volume. Once you have a system that requires this level of throughput, it will make economic sense to move to a monorail.
Considerations for a Monorail System
Before you dive into implementing a monorail system, also keep in mind the following details that you’ll want to consider in your facility and operation layout.
Empty Trolley Buffer – If the facility can accommodate the additional space, one feature that can improve the efficiency of the system is a by-pass for a holding area where trolleys can accumulate while not in demand. Without a holding area for trolleys to stage off the main loop, they will need to be recirculated around to stay out of the way for trolleys that are in use.
Safety – These systems require safety fencing which can sometimes be an
obstruction for the facility. Additionally, at the infeeds and outfeeds where the monorail system trolleys exchange pallets with static conveyor systems, light curtains may be required.
Track Switching – To further improve the flexibility of these systems, some manufacturers incorporate track switches which allow the system to feature multiple loops. This can allow the trolley to take shorter paths to their destination. It can also provide some redundancy since the system could feature a few smaller loops instead of a single large loop. A simulation can help clarify the pros and cons of track switches for your operations.
Trolley Design – There are many possibilities when it comes to types of trolleys. For example, a fully static trolley that is a simple load carrier.
It is possible to use either drag chain or rollers for the conveyor on the trolley. Some manufactures even offer dual conveyor trolleys to move two loads at a time.
Environmental – Manufacturers have designed their products to work in extreme environments like deep freezers. However, one important consideration while designing the system is to observe where temperature gradients might be present. If a portion of the trolley system is close to another area of the facility that is at a drastically different temperature, fogging, condensation or even freezing can occur. This can be avoided by ensuring proper space between these areas of the facility or carefully controlling the amount of moisture content in the air.
Exchange Points – The monorail system will only be as fast as where it interfaces with other systems. It is extremely important to minimize the amount of transfer time for the pallet conveying from the static conveyor onto the trolley conveyor. Bastian Solutions recommends increasing the size of the drives on the static conveyor that feeds the trolley conveyor to minimize transfer time.
High-Throughput Conveyance
Overall, one key advantage for pallet monorail systems is the investment cost. For high throughput applications, a pallet monorail system can be significantly less expensive than an equivalent roller conveyor system. Additionally, these systems offer better expandability with being able to add more trolleys in the future to support increased throughput needs. This can help minimize the initial capital for the project.
These systems also feature a spur where trolleys can be taken off the track for maintenance or repair. This allows the system to continue running without any disruptions due to trolley maintenance. This also helps consolidate the maintenance tasks to the maintenance area, instead of an operator needing to perform maintenance over the entire footprint of the system as would be necessary for a conveyor-based solution.
Accommodating various applications and adjustable for performance levels, pallet monorail systems offer a unique alternative. Keep these guidelines in mind when evaluating your next high-throughput pallet conveyance application. Our engineers are always standing by ready to assist with your evaluation.
Image credits:
Bastian Solutions, a Toyota Advanced Logistics company.
We are a trusted supply chain integration partner committed to providing our clients a competitive advantage by designing and delivering world-class distribution and production solutions.
Our people are the foundation of this commitment. Our collaborative culture promotes integrity, inclusion, and innovation providing opportunities to learn, grow, and make an impact. Since 1952, Bastian Solutions has grown from a small Midwest company into a global corporation with over 20 U.S. offices as well as international offices in Brazil, Canada, India, and Mexico.
Comments
Darren J Mabe says:
9/23/2021 09:21 AM
Great post Robert. Easy to read, very educational!
Leave a Reply
Your email address will not be published.
Comment
Thank you for your comment.