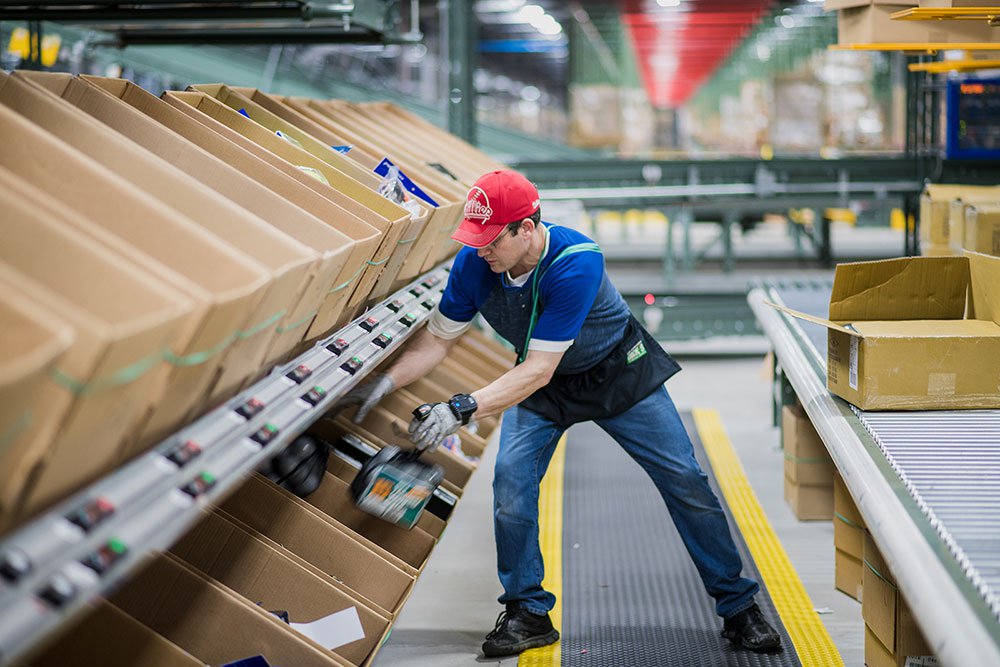
Increase Operational Throughput Using the Theory of Constraints Principles
Anshul Singh | 5 April 2023
All inbound and outbound warehouse operations such as receiving, putaway, picking or packing, for example, formulate a series of dependent events. These events occur in sequence and are, to some extent, interlinked to the events preceding or following them.
Dependent events always have a constraint or a weakest link, affecting the entire system’s throughput. Eliminating these constraints is the goal of any warehouse operation and can be achieved by adopting a continuous improvement process.
This article focuses on utilizing the Theory of Constraint (TOC) principles for continuous improvement. TOC utilizes Five Focusing Steps as guideposts for driving ongoing improvement. TOC efforts focus on finding and eliminating (or shifting) constraints or bottlenecks in the system. Once eliminated, the bottleneck will generally shift to another warehouse operation; for example, manually transporting containers to pick zones as a constraint can be solved by investing in a conveyor system, thus shifting the bottleneck from transport to the picking labor. Automating the picking process can further shift the bottleneck to the packing stations.
TOC application paves the way for modular automation investment that targets and improves the weakest part of the process, enhancing the system’s overall productivity.
The TOC Process
Continuous improvement in the TOC world follows a 3M process – Mindset, Measurement and Methodology.
Mindset
The ideal mindset is for each warehouse operator and supervisor to continuously look for the weakest link in the warehouse operations. To help build this way of thinking, adequate training should be provided to all the operators in the warehouse so that they understand the overall picture of the warehouse process and not their work zone alone. Each operator must be aware of how their work area connects to other operations in the warehouse.
Measurement
Measurement is a critical 3M process as it is the primary method of accounting for the results of actions being taken within an organization. As such, they can be considered a direct output of an activity undertaken within the system. Conventional accounting systems focus on net profit, return on investment and cash flow measurements. These measurements are difficult to calculate for day-to-day operating decisions, especially for the average worker. Thus throughput, inventory and operating expenses are the primary measurements undertaken in the TOC methodology. These metrics are directly linked to the long-term measurements of net profit, ROI and cash flow, and allow everyone in the organization to predict the immediate impact of an action.
Methodology
The final stage discusses the methodology of implementing the TOC concepts. Again, TOC principles aim to find and eliminate bottlenecks – or when demand exceeds capacity. TOC recommends using the following five steps:
- IDENTIFY the constraint. This could be a resource constraint as well as a policy, process, or even management constraint. The only caution to be exercised during this stage is to identify what is causing the delay, not where the delay is. For example, inventory built up at receiving dock could mean that the putaway operation is a bottleneck and not receiving. Frequent mispicks (erroneous or missed pick selection) may result from poor choice of picking technology and only sometimes the operator. Delays in order fulfillment from a particular zone may be due to inventory problems, not operator efficiency issues.
- EXPLOIT the system’s constraint, or make it work. This means ensuring the constraint is fully utilized and running at total capacity. It can be counterproductive to work on efficient areas before focusing on the weakest link.
- SUBORDINATE all other steps in the process to the constraint. Meaning, review everything the constraint requires of non-constraints to work according to the constraint’s resources. Cut back the production of non-constraints in the system. Now the throughput of the whole system is driven by the bottleneck. It’s the most efficient way to run the warehouse unless it needs to invest in the next step in the methodology.
- ELEVATE the system’s constraint. Elevating is when effort and sometimes money is spent to increase the capacity of a process or resource. This is where investment or modification in technology could be needed to take the system to the next level, as seen in the case study in the next section.
- REPEAT the TOC process. Once the bottleneck is alleviated, go back to Step 1 to identify the next weakest link. Don’t allow inertia to cause a system constraint.
TOC in Action: Case Study
The Bottleneck
Utilizing the TOC principles for continuous improvement Bastian experts were able to diagnose and eliminate the bottleneck of a picking system in a distribution center for a beauty and cosmetics company. Identifying and eliminating a constraint in this system was measured in terms of throughput or cartons picked per hour. The picking system was designed to process 700 cartons per hour, but the system was only producing a throughput of 550 cartons/hr. The goal was to identify and eliminate bottleneck to improve throughput and meet order fulfillment deadlines.
System Details
The layout has ten zones of pick-to-light technology. All cartons are inducted at the beginning of the pick module centerline conveyor. Each pick operator covers a zone of 4 picking bays and scans every carton entering their zone to initiate picks. The takeaway-powered centerline conveyor has bi-directional transfers for each zone (see illustration below). The transfers at the beginning of each sub-zone are to take the carton to its appropriate picking zones.
Resolution Attempts Before TOC Implementation
Many conventional solutions were deployed to increase throughput, such as:
- Perfecting the slotting of the pick module.
- Making the zones operationally dynamic, so operators are not limited to one zone.
- Increasing the pick-to-light system's pick density.
- Increasing the operator count by adding floaters in the system.
- Implementing operator productivity measurement in place with feedback.
TOC in Action
Despite using the several means stated above, the system throughput could not be improved. Finally, a team of dedicated experts utilized the five steps of Theory of Constraints methodology to locate and resolve the bottleneck, as seen below.
- IDENTIFY – Instead of randomly improving operations in all areas; the effort was focused on finding a single bottleneck in the system. The simulation was compared to actual operations to identify the system bottleneck. It was noticed that each carton on the centerline conveyor was stopping for 1.2 seconds at the scanner for diverting or going straight decision. Stopping cartons at the transfer was critical as the scanners were placed right against the transfer.
- EXPLOIT – Since every carton had to pass through the scanners, the process already exploited this constraint to the maximum capacity.
- SUBORDINATE – Floaters were removed from the system to reduce unproductive time. These operators were moved to static zones (this allowed for accurate productivity calculations).
- ELEVATE – To reduce the constraint of 1.2 seconds, the scanners were shifted away from the transfers to increase the time it took for a carton to reach the transfer after the scan. This reduced the time of cartons stopping at the scanner.
- REPEAT – The system hit the 700 cartons/hour target as soon as the change was made. Of course, the bottleneck then shifted to another part of the process.
Expertise That Makes Change Easy
Having reliable, efficient distribution operations is crucial to the success of any business, affecting customers and employees alike. Realizing there is an issue within your material handling system is one obstacle but pinpointing the issue and exploring all alternative solutions is another entirely.
Bastian Solutions can help by applying the TOC principles to your unique process, ensuring energy and capital are continuously invested in a focused manner. Get one step closer to reaching your operational goals by reaching out to an engineer today.
Anshul is a Senior Logistics Consultant with Bastian Solutions' software division. He has a bachelor’s engineering degree from the Indian Institute of Technology, a Master's in engineering from Purdue University and an MBA from the University of Louisville.
Comments
No comments have been posted to this Blog Post
Leave a Reply
Your email address will not be published.
Comment
Thank you for your comment.