Improve Your Automation System Safety with These 4 Components
Matt Kohler | 16 July 2015
In the automation world, safety is of the utmost importance. Not only do industrial robotics and other automated material handling systems perform difficult tasks that keep personnel out of unsafe and ergonomically difficult conditions, but these same automation systems must be inherently safe for personnel to work around as well. We utilize a variety of safety products to ensure the automation systems we design and manufacture are as fundamentally safe as possible. Here are a few of the most critical safety components when automated material handling systems are in use.
Safety Fencing
At the top of the list of automation system safety components is safety fencing. Safety fence prevents operators from accidentally reaching into the robots work envelope, and must be designed with operator safety and functionality in mind in order to allow for easy operator access to critical locations within the cell.
Robot Software
Industrial robot manufacturers have developed software (Fanuc – Dual Check Safety, ABB – SafeMove) that allows us to modify the robot’s work envelope. The ability to modify the envelope allows us to reduce the size of our robot cells and to safely bring the fencing in closer to the robot. This also gives the operators easy access to interface with the robot using additional safety devices such as light curtains, area scanners and safety mats.

Light Curtains, Area Scanners, and Safety Mats
Light curtains allow pallets of product to safely enter the cell while the robot is working, but will stop the cell if a person tries to enter. In similar fashion, area scanners and safety mats can be programmed to stop or reduce the speed of the system if an operator is in the area. If these components do not fit an end user’s needs, there are additional safety devices that can be implemented to suit each situation.
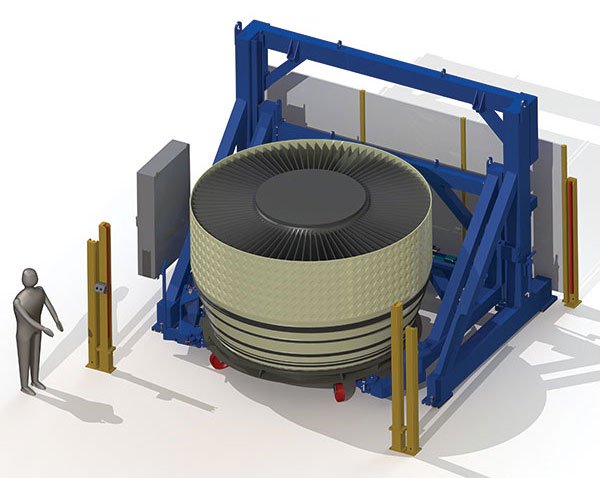
Allen Bradley GuardLogix®
Bastian Solutions' robotics has standardized on the Allen Bradley Guard Logix PLC and safety control platform. This technology allows Bastian Solutions' robotics to combine the robotic cell control with the safety controller to maximize functionality and minimize the overall system cost.
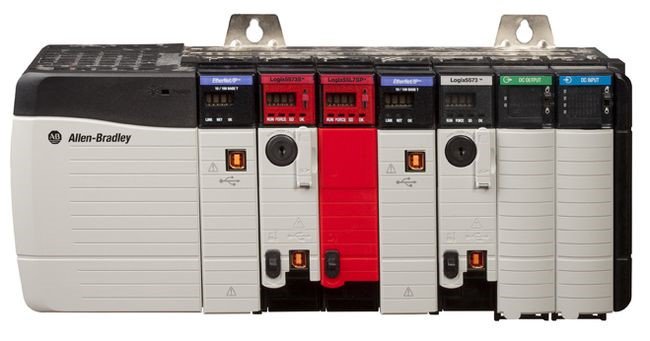
Lastly, with the demand for autonomous mobile robotics and collaborative robots (cobots) -- including robots on AGVs, robots on rails, etc.-- the proper utilization of the safety systems listed above will be imperative to make sure that these autonomous robots are able to move and work among humans in a safe and efficient way. If you have questions about improving the safety of your automation system, please contact us.
Matt Kohler, Bastian Solutions Director of Applications has been with Bastian Solutions since 2005, after receiving his degree in mechanical engineering from the University of Missouri - Columbia. The applications team at Bastian Solutions prides themselves on thoroughly understanding their customer’s unique needs and then tailors a solution that gives those customers a competitive edge in their business.
Comments
No comments have been posted to this Blog Post
Leave a Reply
Your email address will not be published.
Comment
Thank you for your comment.