Implementing AGVs with Robotic Palletizing Systems
Scott Hendricks | 05 August 2020
An automated guided vehicle’s (AGV) key role when interacting with robots is the delivery/removal of materials. Special attention needs to be given to interaction points in order to have a successful automation ecosystem. Typical material delivery/removal include empty pallet stacks, stacks of sheets, or completed loads. In the past, these materials would be handled by an operator or a forklift driver and if the operator was required to enter the robot cell, the robot would be required to stop production in order to provide a safe environment for the operator. For AGVs, this is not the case. AGVs can enter and exit the robot cell to perform work without any robot down time.
Critical decisions need to be made on how best to utilize AGVs and determine how they are going to interact with materials and the overall system layout. When handling pallets, either a lift style AGV or a conveyor style AGV can be used. Below are general rules of thumb when determining the best unit for your application.
Lift Style AGVs: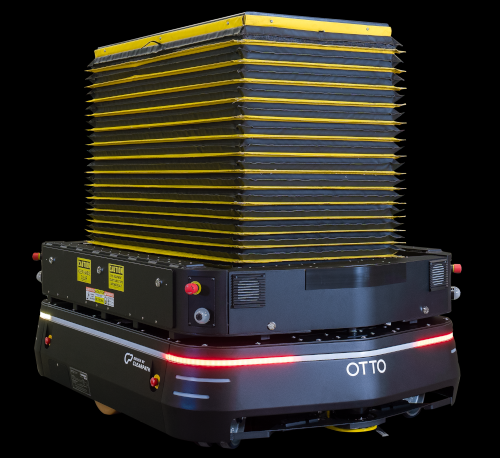
- Used when robotic cell space is at a premium
- Interaction points need to be at an elevation of 25” or higher
- Works well within robot cells
- Supporting equipment: Requires static stands and/or specialized pallet conveyor
Conveyor Style AGVs:
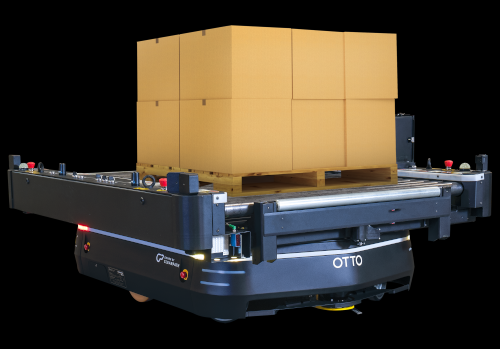
- More space required for drive lanes
- Needs a conveyor inside the robot cell to
- load and unload materials
- Interaction points need to be at an elevation of 22” or higher
90 percent of the time these two styles of AGV/SGV will cover a palletizing application. To account for the other 10%, Bastian Solutions’ custom automation division has the expertise to design, manufacture, and integrate custom AGV attachments for those truly unique payload conveyance challenges.
Another important factor is the communication required between the robotic palletizing cell and the AGVs. Communication is done through a network of PLCs and the AGV server in a much more harmonious way. The AGV server conducts the AGVs by telling each unit where they need to be and when. This is done by generating missions based on feedback received from PLCs around the plant. The palletizing cell PLC signals the server of the required task; that could be a request for a new empty pallet, sheet stack low condition, or load built complete signal. The AGV server then generates missions, assigns them, and coordinates the fleet.
Below is a network layer flow diagram of this communication.
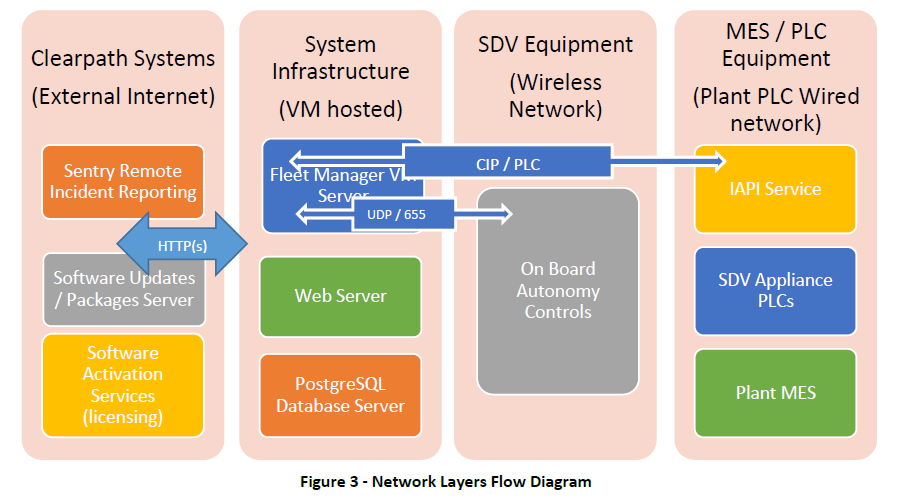
Summary
There are many aspects to designing an AGV system; even more so when robots are involved. Firstly, what is the best way to handle the materials to/from the robot cell? This is just the first decision of many in the design or integration of an AGV system. Bastian Solutions has integrated multiple solutions interacting with robotic palletizing systems and can help with your next successful AGV system – reach out to our engineers with any questions!