How to Select a Warehouse Management System
Marvin Logan | 06 February 2018
Searching for a new warehouse management system (WMS) can be a complicated matter. It is very important to have a plan for success before starting, and then work that plan to the best of your ability. The key to a choosing the right WMS is finding one that meets your specific business requirements and comes from a company that can work within your corporate needs and culture. No matter which platform you choose, the benefits of implementing a WMS should include:
- Increased productivity without adding labor
- Reduced operating costs
- Increased inventory control and accuracy
- More visibility within the warehouse
- Increased order throughput
- Reduced order cycle time
To get started in your warehouse management system selection process, below are the first four steps to finding the best provider for your company.
1. Form a Project Team
The first step is forming a project team for the WMS selection. It is very important that the team be made up of all the key stakeholders including senior management, operations, inventory, IT, etc. Also, it is important that you select a good consulting partner with experience in WMS selection. A WMS selection is often a once in a career project. So using a competent consultant that can guide you through the process and asking the right questions can be the difference between a successful selection project or a complete flop.
2. Understand Your Industry and Required Business Functions
With the help of a strong project lead person or consultant, the first step the project team will need to take is to understand the business requirements that the WMS will need to satisfy. Although many of these will be operational (e.g. RF receiving, QC checking, weight and dimension capture, rule based put-away, various picking methods, etc.), industry requirements are also important to understand (e.g. lot tracking, 3PL cost allocation, VAS processing, compliance labeling, etc.). This will take several meetings with cross-functional subject matter experts (SMEs) to compile all the elements. As someone’s “needs” may be perceived as another’s “wants”, it is often good to relatively rank the requirements. It is also a benefit to employ requirement categories such as “must have” (can’t operate without it), “nice to have” (a needed feature that may have a work around), or “advantage” (not really needed but would create an operational or business advantage). The categories can then be used later to weigh the supplier’s score cards.
3. Develop an RFI
The RFI, or request for information, should address your requirements and get information on all the potential suppliers. To achieve this, it should have a “fill in the blank” format. Besides asking the suppliers if they can provide the functions required, the RFI should also gather information about the supplier and its WMS product. Examples would be: Size of company, annual revenues, years in business, etc. When questioning the functional requirements, it is also important to know if the supplier can support each function in the “base” software or if a “modification” is required. The use of a spreadsheet that can easily be edited by each supplier is a format that is often used. A small sample of this method is shown below: 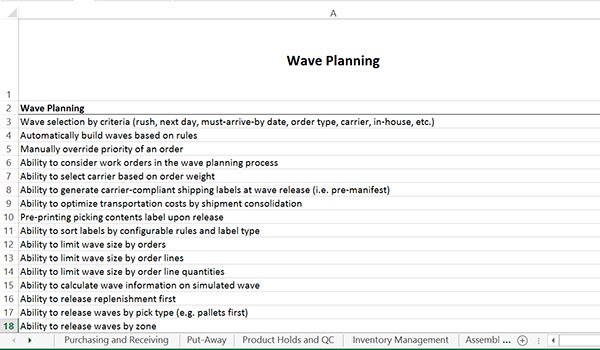
4. Create a List of Potential Suppliers
Once you have your RFI ready, create a list of potential suppliers. To do this, the first concern would be the type of WMS product to consider. You need to consider your existing systems and infrastructure compatibility (e.g. does is make sense to deploy an SAP WMS if you utilize an Oracle ERP?). Should you consider only Tier 1 WMS products, which will be feature rich, but will also come at a higher cost? Or should you only solicit responses from companies that provide Tier 2 or 3 systems that will be less costly initially, but perhaps limit future enhancements without modifications?
You will also want to consider the integration requirements (e.g. systems that will need input/output to the WMS). If the WMS implementation is part of a larger automation project, it might be possible to consider using a WES (Warehouse Execution System). A WES combines the features of a WMS with a WCS (Warehouse Control System) - which would be required for the automation (e.g. conveyor routing and sortation, goods-to-person technologies, robotics, etc.).
Once the type of system is determined, there are many ways to get a list of potential suppliers. Using your industry contacts, Internet searches (e.g. Google search “Warehouse Management System”), Gartner Magic Quadrant, industry trade organizations and trade shows are all some possible suggestions to explore. By following these four steps, you'll be well on your way to a successful warehouse management system selection. For more information or for assistance with your WMS selection process, please contact our team of consultants.
Marvin Logan is the Vice President of Consulting and Integration at Bastian Solutions. After graduating from Purdue University, Marvin started his career as an industrial engineer and quickly moved into management. He has had roles as a distribution system manager, operations manager, director of engineering, director of distribution, and vice president of distribution for several leading companies.
Comments
No comments have been posted to this Blog Post
Leave a Reply
Your email address will not be published.
Comment
Thank you for your comment.