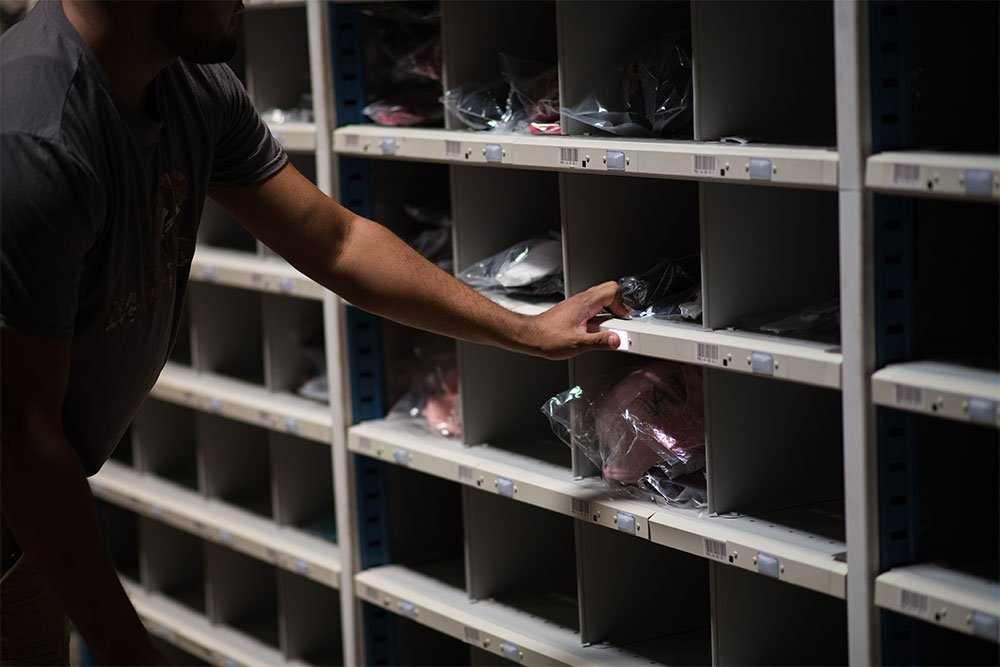
How Accessible Automation Can Optimize Distribution Amid Seasonal Fluctuations
Alex Haines & Matt Kuper | 29 May 2024
Distribution centers are increasingly at the mercy of fluctuating demand, a challenge amplified by clear seasonal and ecommerce trends. As consumer behavior shifts and online shopping events gain traction, these facilities must adjust to significant peaks and valleys in product flow. This unpredictability can strain resources and complicate warehouse logistics.
Accessible automation is a promising response to today’s distribution center challenges. By integrating automated point solutions into existing distribution frameworks, businesses can enhance process efficiency and adaptability without the substantial upfront investments required by larger, more complex systems. These solutions offer a practical pathway to modernizing operations and achieving a sustainable competitive advantage.
The Impact of Seasonal and Industry Demand Fluctuations on Distribution Centers
The continued growth of e-commerce and more defined seasonal shopping trends present a complex challenge for distribution centers. Major shopping events such as Cyber Monday, back to school, Mother and Father’s Day, and seasonal sales can spike demand dramatically. Conversely, during off-peak times, these facilities might experience significant drops in activity. Unpredictable factors like adverse weather can also trigger sudden surges in demand for specific products, further complicating logistics.
Holidays tend to impact the retail industry most, but it isn’t the only industry affected by seasonality. We also see seasonal highs and lows with industries like industrial distribution, for example, with the increase of SKUs to support aftermarket part increases. Other industries may also require full pallet handling to store additional finished products to support increased demand.
With these seasonal shifts, whether in retail, industrial distribution or general merchandizing, for example, a facility might handle three times its usual volume, requiring additional temporary staff and increased operational hours. In contrast, the months between seasonal peaks often see a sharp decline in demand, leading to excess inventory and idle resources. Such variability complicates inventory management and inflates hiring, storing and maintaining additional equipment costs.
These dynamics strain material handling logistics, often revealing inadequacies in current infrastructure and processes. Facilities that fail to adjust their operations to handle these peaks and troughs efficiently can suffer from delayed order fulfillment, increased backlogs, and customer dissatisfaction. The pressure to quickly scale operations up or down can lead to operational errors and reduced quality of service, further impacting profitability and brand reputation.
Understanding Accessible Automation in Distribution Centers
Accessible automation refers to the strategic implementation of automated solutions that are easy to deploy and scale according to a distribution center's specific needs. Unlike traditional, large-scale automation systems that often require significant restructuring and investment, accessible automation focuses on point solutions—smaller, discrete systems that can be seamlessly integrated into existing operations. This category includes technologies such as autonomous vehicles, goods-to-person systems and end-of-line automation.
Accessible automation solutions provide adaptability, with the added benefits of reduced downtime and lower initial costs. This enables significant operational benefits and allows businesses to stay agile in a competitive marketplace.
Advantages of Implementing Accessible Automated Point Solutions in Distribution Logistics
Accessible automated point solutions are targeted technologies that solve specific challenges within distribution centers, particularly in critical areas such as order picking, packaging, and shipping. These technologies improve the precision and speed of these operations.
The key benefits of these point solutions include:
- Scalability: These solutions scale with the business’s needs, supporting incremental growth without substantial upfront investments. This scalability helps in managing financial flow and investment risks effectively.
- Integration: Point solutions are designed to integrate smoothly with manual and existing automated systems. This integration preserves prior investments while enhancing operational efficiency, enabling continuous improvement with minimal disruption.
- Cost-effectiveness: With lower capital expenditure requirements than comprehensive systems, point solutions are financially accessible for many businesses. The combination of lower initial costs and improved operational efficiencies ensures a faster return on investment.
- Flexibility and Customization: Point solutions offer remarkable flexibility and can be tailored to meet specific operational demands. They easily adjust to seasonal peaks, accommodate new product lines, or scale operations up or down, providing the agility to respond to market changes swiftly.
Accessible automated point solutions align closely with the strategic goals of distribution centers, helping them stay efficient and competitive despite the ever-present fluctuations in market demands and operational challenges. This strategic approach enhances current operations and sets a foundation for future growth and adaptability.
Leveraging Systems Integration for Optimal Automation Implementation
Working with a systems integrator can provide substantial benefits to further enhance the effectiveness of implementing automated point solutions in your distribution center. A systems integrator specializes in bringing together various systems into a cohesive, functioning whole that operates seamlessly. This approach ensures that all components of your automation setup work together harmoniously, maximizing the efficiency and productivity of your operations.
Partnering with a systems integrator can streamline the process of incorporating new technologies into your existing infrastructure. They handle the complexity of design, coordination, and implementation, which can significantly reduce the risk of project delays and cost overruns. Furthermore, systems integrators have expertise in various technologies and can provide tailored solutions that fit your specific operational needs. They ensure that the automation scales properly with your business growth adapt to future technological advancements and integrates well with legacy systems.
The collaboration with a systems integrator also provides access to ongoing support and maintenance, ensuring that the automated systems function optimally long after installation. This support is crucial for minimizing downtime and maximizing return on investment. By leveraging the knowledge and experience of a systems integrator, you can achieve a higher level of automation success, making your investment into accessible automated point solutions even more rewarding.
Maximize Your Distribution Efficiency
Adapting quickly and efficiently to fluctuating demands is crucial for distribution centers to maintain a competitive advantage. Accessible automation and the strategic use of automated point solutions offer distribution centers the agility, scalability, and cost-effectiveness needed to meet these challenges head-on. By implementing these innovative solutions, facilities can enhance operational efficiency, reduce downtime, and significantly improve throughput, all while managing costs effectively.
To learn more about how accessible automation can be implemented in your operations, read our comprehensive whitepaper, "Accessible Automation for Point Solutions in Distribution." This resource provides you with the knowledge and tools to begin your journey toward a more efficient and responsive distribution system.
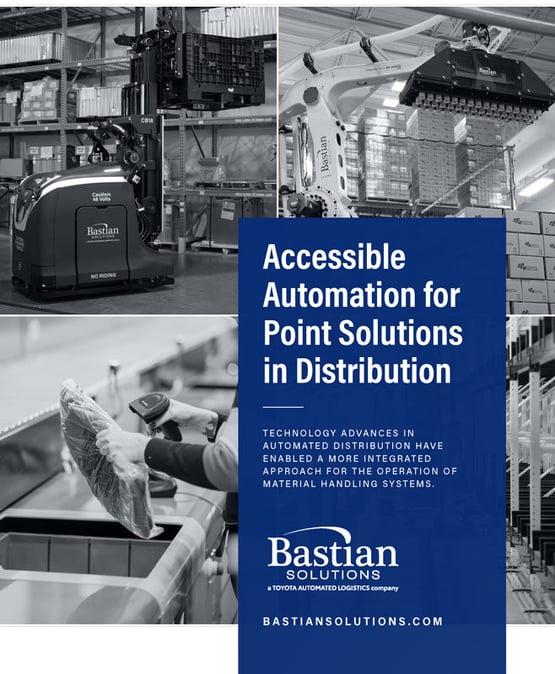
Download the whitepaper and discover how you can transform your distribution center to thrive through the ups and downs of today’s dynamic retail environment.
Alex Haines is the Director of New Business Development & Strategy Accounts at Bastian Solutions. Alex works with customers across various industries, looking for opportunities to help clients automate their supply chain to address both the pain points and opportunities posed by rapidly changing customer demands. Alex has more than 15 years of experience in global supply chain strategy, operations and sales.
Matt Kuper, the VP of Global Sales and Applications at Bastian Solutions, has more than 15 years of experience in the material handling industry handling a variety of systems projects and technologies including high-speed sortation, pick modules, goods-to-person, and pallet handling systems. He joined Bastian Solutions in 2013 and has since overseen some of the company’s largest and most complex integration projects.
Comments
No comments have been posted to this Blog Post
Leave a Reply
Your email address will not be published.
Comment
Thank you for your comment.