Get the MOST from Your Workforce
Nathan Busch | 19 November 2015
If your process rates are unknown or outdated, a measurement study called MOST can determine the rates needed to maximize output.
Do you or any of your clients have processes or tasks where employees’ expected rates are unknown, based on averages, or quite frankly conjectured from guessing? Processes can range from warehouse receiving, put away, picking, packaging, value-added services, etc. to clerical office tasks. Rates may also be unknown or need re-evaluation because of new or different layouts, or process changes. If any of these situations are affecting your employee production rates, then you should consider MOST!
What is MOST?
Maynard Operation Sequence Technique (MOST) is a predetermined motion time system used to measure the manual movement of objects. MOST was developed with HP Maynard & Co. in 1974 and is a well-established, nationally recognized system.
The goal of MOST is to create engineered standards for the time it should take to perform tasks. It achieves its goal by focusing on the methods used to perform tasks, as opposed to time studies and averages. Every motion within a task is measured separately and assigned values that represent standard time measurement units, or TMU. One second equates to 27.8 TMU.
How does MOST work?
Every motion within a task receives a Sequence Model--a technical story of what is occurring during the motion. Key words utilized in the Sequence Models include “gain control (of the object) from (location)”, the placement motion, and the placement location. Through the aid of data cards, index values are assigned to each component of a Sequence Model based on the difficulty, distance, complexity, and repetition of the motion. All the index values from all of the Sequence Models for a given task are summed for a total TMU. The TMU is then converted into time, which will represent the standard time to complete the task. Often, time is added for allowances. These allowances are typically well-known consistent times, or measured, before being included in the standard time to complete a task.
MOST in action
Bastian Solutions' consulting group performed a study for a client where MOST was utilized to measure picking rates. The client recently relocated its operation into a 150,000 square foot distribution center, with more than 55,000 square feet consisting of shelving storage for order fulfillment. Employees batch pick orders to carts as they are directed by voice technologies and walk the aisles of shelving. Orders are fulfilled by different processes based on the channel: direct-to-consumer or retail store fulfillment. The goal of the study was to validate the current picking rates, or recommend new rates, for the layout of the customer’s new distribution center.
Bastian Consulting’s study analyzed direct-to-consumer orders, direct-to-consumer single-line orders, and bulk retail orders. During the measuring phase of the study, we found there were two types of orders being fulfilled from the bulk retail processes--orders with many lines, but small quantities per line, and orders with fewer lines, but mostly full or almost full case quantities. The client was currently measuring both order types to the same hourly piece rate.
Bastian Consulting measured the order types independently and found the expected standard times varied greatly. The conclusion of the study yielded the standard time per pick for each respective order type, and converted it to hourly piece rates based on observed pieces per pick and pieces per order. Bastian Consulting’s final recommendations and the client’s current rates can be seen in the chart below.
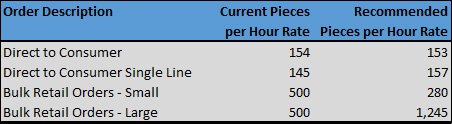
In summary, if you or your clients need to develop new rates or update current rates for any reason; new building, updated layout, process changes, etc., consider using MOST. If you have questions or would like assistance with this process, please contact our consulting team. We would be happy to help.
Comments
A 3-Step Method to Warehouse Optimization | The Material Handling Blog says:
8/28/2018 10:09 AM
[…] employees accountable, but also allows you to optimize your labor force. See Nathan Busch’s blog Get the MOST from Your Workforce for more information on […]
10 Common Warehousing Mistakes to Avoid This Year | The Material Handling Blog says:
8/28/2018 10:09 AM
[…] Related article: Get the MOST from Your Workforce with a Motion Time Measurement System […]
Leave a Reply
Your email address will not be published.
Comment
Thank you for your comment.