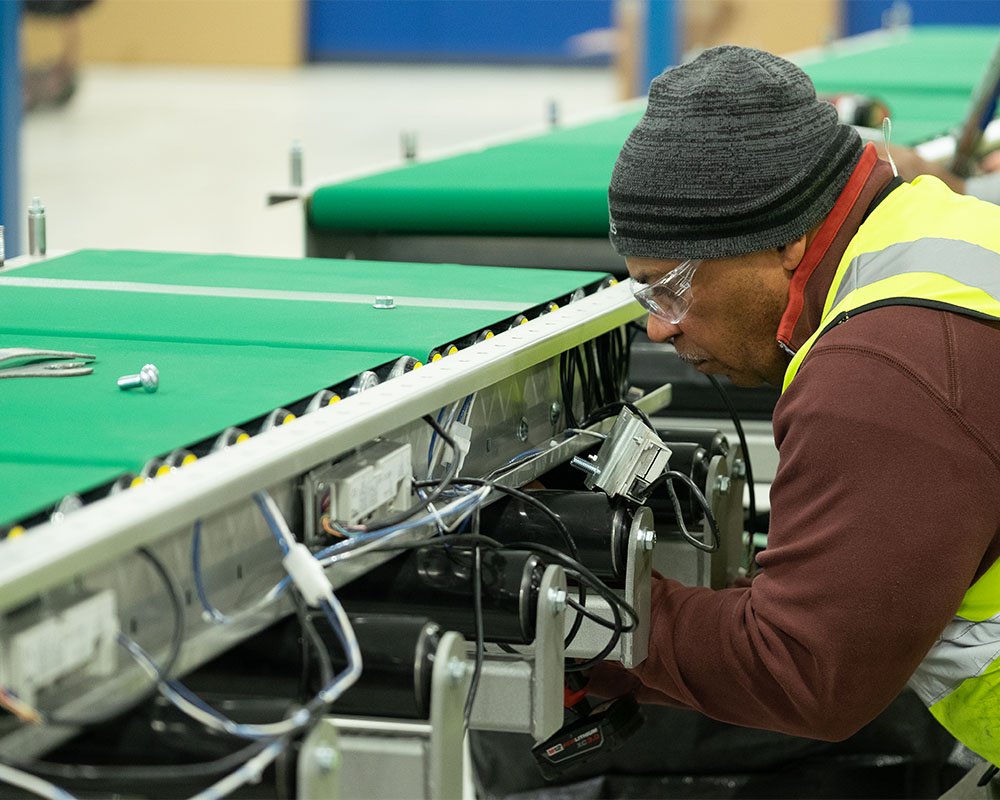
Fostering Innovation in Supply Chain & Logistics
Tiffany Greyson | 12 May 2021
One of the biggest benefits and challenges of being a supply chain and material handling independent integrator is that we work with a variety of industries and clients, from the latest technology in aerospace to streamlining manufacturing and leveraging new trends in ecommerce. Today, companies around the world are shifting their operations to meet the needs of market challenges – acceleration of ecommerce, microfulfillment adaptation. But, with that too comes a need for maintained quality and reliability.
That’s a tough, yet necessary balance to strike. How do you achieve it? It’s pretty well understood that innovation isn’t something that you can just make happen. New ideas take time and nurturing.
In our Research and Development (R&D) department, we face challenges regularly in developing solutions that meet clients’ needs and industry requirements. The nature of these challenges can vary greatly but what we’ve found to be an impactful aid is to create an atmosphere of out-of-the-box thinking.
Maintaining that balance and discovering new applications for existing technology or new technology for different applications, starts with a culture of “thinking big.” This Inventors Month and Week of Making (May 17-23) we wanted to take the time to highlight some of the ways we can keep innovation growing in supply chain and material handling.
From our experience at R&D in Boise, Idaho, there are three key considerations when building and encouraging innovation. It starts by building the concept into your work culture.
Consider a Makerspace
Innovation corners or makerspaces are common at technology and software firms. This concept can also be applied in supply chain and logistics. A makerspace is, in general, a collaborative workspace inside a facility that is dedicated for making, learning, exploring, and sharing using a combination of high-tech and low-tech tools.
While there certainly a lot of benefits derived from makerspace environments, there are three stand out points that we’ve noticed:
- Inspires collaboration – A dedicated, assigned space develops a focal point where individuals and teams can come together.
- Breaks down silos – These spaces attract people of all roles and disciplines, encouraging conversation, interaction, and knowledge sharing.
- Employee engagement and growth – This can be an opportunity for employees to comfortably explore crossover talent or hone their existing expertise to build confidence.
Elements for a Successful Space
How do you make for a successful space? While budget certainly plays a role in the resources available to your space, there are other elements that are crucial to creating an environment that is engaging, and most importantly, impactful.
Resources – You’ll want to have a dedicated space that features room for seating and storage of tools. You’ll want to have a combination of both high and low-tech tools for tinkering. Some have explored having packaged kits for check out or use during sessions.
Learning events – Depending on available resources, innovation corners can be leveraged for learning events to teach or dive deeper into engineering concepts – robotics or circuit boards, for example. This is also an opportunity to draw in community experts or have technology “show and tell” features from current or potential vendors.
An executive champion – An executive champion helps to drive support and excitement for a makerspace or innovation corner from the top down in your organization. This helps with funding, sharing of success, and promotion.
Accessibility – Like several of our clients who have had to consider new solutions for their warehouse and distribution center functions in light of the COVID-19 pandemic, makerspaces and learning events have also pivoted. Consider accessibility to your spaces and opportunities for virtual events.
Translating Success to Projects
No matter how small or large innovation corners or makerspaces are, they offer opportunities outside of assigned projects, deadlines, and deliverables for your teams. However, it’s important to capture the success and the value that they bring. This is important to justify the development or continuing of such a program but to encourage participation.
Often the impact is more concrete and visible than others. We’ve seen the impact firsthand in our supply chain and material handling projects:
- Creates a comfort in trying new technology combinations, innovations in problem solving
- A solution we considered in one place may work in another place
- Offers a space for a different thought process and approach
Creativity for Better Quality & Solutions
The impact of a maker space is not always easily quantifiable in throughput or picking statistics, but the benefits are above and beyond. The value of thinking outside of the box, whether it’s encouraged and developed through a makerspace at work or other method, is invaluable as companies and industries continue to shift to fit market changes.
At Bastian Solutions our core values center around the concept of continual growth and innovation – taking on and exploring challenges – to work better and bring value to our clients.
Tiffany Greyson is the Lead Electrical Engineer at Bastian Laboratories. She is the electrical systems architect of Bastian's Robotic Shuttle, which has been called the "Holy Grail" of automatic storage and retrieval systems. She works for Bastian’s Chief Innovation Officer and focuses on innovation enabling small businesses to compete with large retailers for one-hour delivery. In her spare time, Tiffany and her husband Adam are raising three little nerdlings.
Comments
No comments have been posted to this Blog Post
Leave a Reply
Your email address will not be published.
Comment
Thank you for your comment.