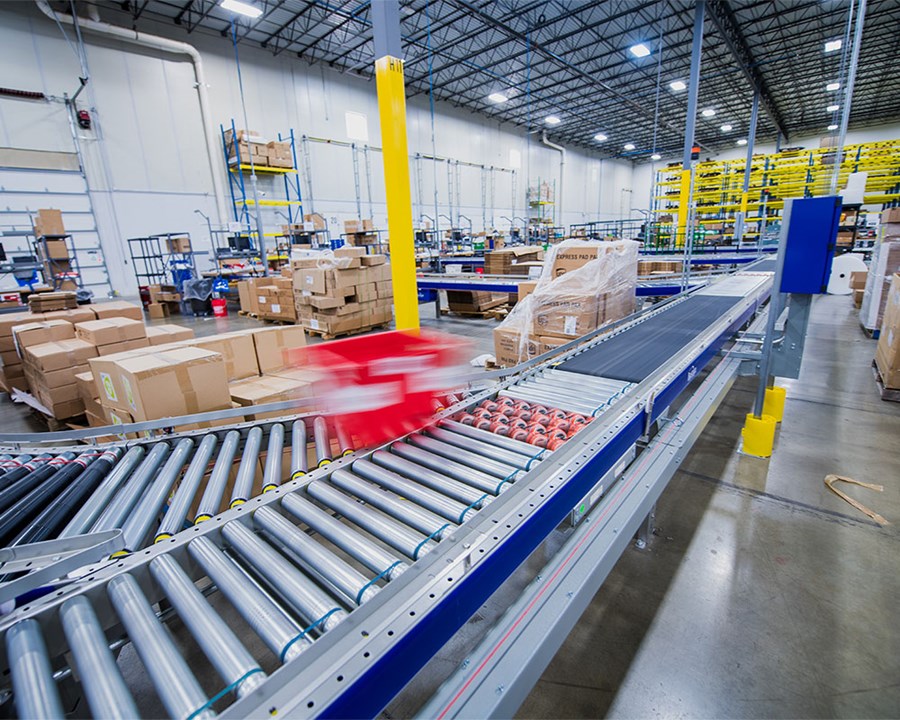
Elevate Your Warehouse Efficiency: Identifying Conveyor Opportunities
Lane Andrews | 13 December 2023
In the dynamic landscape of warehouse operations, efficiency is the cornerstone of success. As businesses strive to streamline their processes, there's a unique opportunity for warehouse operators to revolutionize material handling with conveyor systems.
Warehouses are undergoing a significant transformation, driven by the need for streamlined operations and increased productivity. Recognizing this evolution is the first step for businesses looking to stay ahead in an ever-changing market. Labor costs, inventory management complexities and navigating seasonal peaks are common hurdles. In this blog post, we'll explore how businesses can identify and leverage conveyor opportunities to elevate their operations.
Identifying Conveyor Opportunities
The key to unlocking conveyor opportunities lies in identifying areas where these systems can make a significant difference. Repetitive and manual tasks, high-volume operations and space constraints, for example, are indicators that a warehouse could benefit from conveyor system solutions. If you have pack-out stations, carts, gaylords, pallets or sortation needs to sort shipments by carrier, for example, you may benefit from conveyor automation solutions.
Once needs are confirmed, a systems integrator can help walk you through various analysis and review points to determine the optimal conveyor solution, placement in the facility and integration with other technologies. Some of those details include:
- Product or material traffic rate and routing
- Facility space and layout
- Special product handling needs
- In-line equipment – ID scanners, scales, print & apply label applicators
- Automation technology and system integration
Conveyors are versatile automation options that can handle a variety of sizes, shapes and weights. They can be designed to fit a variety of facility layouts. Generally, this technology can be classified as either sortation, accumulation or transport.
- Sortation conveyor directs products to different areas within the facility; commonly used to sort products for various shipping destinations, for example.
- Accumulation conveyor gathers and lines up cartons or units for further processing.
- Transport conveyor moves products, cases, totes or pallets from one point to another.
Customer Success through Conveyor System Automation
Cost savings, increased productivity and improved safety are compelling reasons for businesses to consider incorporating these innovative systems. ROI (return on investment) can easily be calculated, showcasing potential cost savings over time and highlighting revenue gains, Bastian Solutions ensures businesses can make informed decisions.
The system projects below highlight transformative applications using different conveyor technologies and integration provided by Bastian Solutions.
- Prime Distribution Services, Inc.: a 3PL in Plainfield, Indiana, was able to consolidate their facilities to one location, better positioning them for order volume growth and improving operator productivity. This site leveraged conveyor, conveyor merge, a two-level pick module, scan tunnel, and software and controls.
- Southern Glazers Wine and Spirits: the largest wine and spirits distributor in the U.S. consolidated their Florida facilities to a 1.2 million square foot site. This location featured pallet conveyor, case conveyor and sortation, carton flow and pallet flow racks, two five-level pick modules, and ExactaBev distribution software. This delivered a 22% increase in cases picked per hour, minimized forklift traffic due to automated conveyor systems and 25.5 million cases shipped per year.
- Mary Kay: one of the largest direct-selling companies in the world, boosted their hourly picking rates by 29% and maximized their labor efficiency with the help of pick modules using pick to light systems, Bastian conveyor, an automated pack process, and software and controls. This resulted in 100% system up time, improved throughput by 46% and average of 768 lines per operator per hour.
- Amway: a leading seller of nutrition, wellness, beauty and home care products, was looking to streamline their operations at its Midwest regional service center. The new facility system automation helped to expand their cartons handled per day to 30,000, reduced their shipping container waste and expedited their order fulfillment times. The site features pick to light systems, voice picking, in-line weigh scales and automatic labelers, two miles of conveyor, zero pressure accumulation conveyor, and software and controls.
Thrive with the Right Conveyor Solution
By identifying areas for improvement and presenting tailored solutions, companies position themselves to thrive in the evolving landscape of material handling. Bastian Solutions offers tailored conveyor solutions that can address these challenges head-on. By introducing appropriate conveyor systems, businesses can optimize material handling processes, reduce reliance on manual labor and enhance overall efficiency. Bastian Solutions' conveyor systems offer a compelling solution to these warehouse challenges. Our experts are available to discuss your needs and challenges to find the right automation solution.
Lane Andrews is a Field Application Engineer at Bastian Solutions, based in Northern California. Working closely together with the local Toyota Material Handling dealer, he works with the team to deliver integrated solutions to the Oregon and Northern California regions.
Comments
No comments have been posted to this Blog Post
Leave a Reply
Your email address will not be published.
Comment
Thank you for your comment.