Distribution Center Layout and Design - Part 1: Fundamentals
Marvin Logan | 25 October 2018
Distribution center layout and design is a complex discipline that takes experience and knowledge. My goal is to provide a general discussion on the concepts and methodologies used, with the hope that you come away with an appreciation of the complexities and concepts that make up the DC design and layout process.
In Part 1 of this series, we start with the basics. Before we move on to more complex topics, it is important to have a general understanding of the types of DCs and the functions that happen inside.
Types of Distribution Centers
There are four basic types of DCs that serve different purposes:
1. Consolidation – Takes in various products from various suppliers and creates consolidated shipments to its customers

2. Break-bulk – Takes large quantities of a few products and redistributes them in part to various customers.
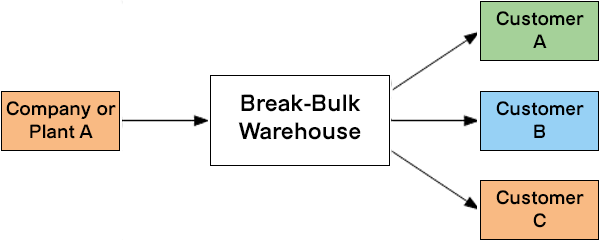
3. Cross-dock – A distribution center that holds little to no inventory, but merely redistributes the product it receives
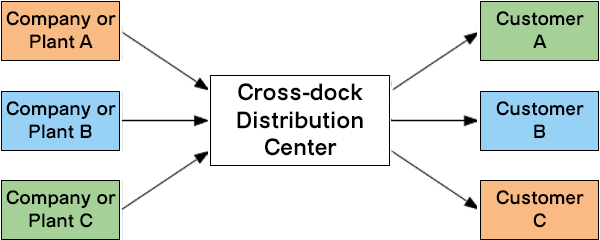
4. Mixing or Order Assembly – May do some or all the other three. It is what people typically think of when they consider the term “distribution center”
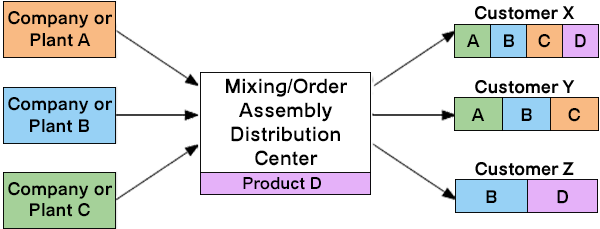
Inside a Distribution Center
Within a distribution center, there are two basic functions – inbound and outbound.
Inbound
Comprised of receiving and storage, the inbound function begins when material is delivered to the warehouse. The Receiving function involves all activities required to bring materials into the warehouse, including unpacking, inspection, and preparation for put-away into storage. Receiving is usually about 10% of total warehouse operating costs.
Put-away is the act of placing merchandise to storage and includes determining the actual storage location(s) that will be used, transportation to that location, and confirmation that the putaway was done completely. It is about 15% of total warehouse operating costs. Storage can be into reserve locations for later use or directly into forward picking locations.
Outbound
Comprised of order fulfillment and shipping, the outbound processes begin when an order is placed by a customer and enters the warehouse processing systems. Processing orders in a warehouse is typically done by the warehouse management system, or WMS, which will first check if the requested items are available to ship. It will dictate all events that are required to fulfill orders including initiating replenishment, coordinating any automation systems, and scheduling picking and shipping activities.
Order-picking is an especially labor-intensive part of order fulfillment, which can account for between 50-60% of total warehousing costs. Of that, half or more of the costs are attributed to pickers travelling from location to location to gather the materials necessary for fulfillment. A lot of effort in the warehouse design process goes into minimizing picker travel time since it can significantly affect overall efficiency.
Once orders are picked, they are often checked for accuracy. This step can be included in the packing activity or done as a separate process. Packing includes all the activities required to ensure the product will arrive safely and in good condition. It also includes adding any shipping documentation and labels to the packages.
The shipping process includes everything needed to consolidate packages to the order or shipment, preparing shipment level documents, and loading the carrier’s truck.
There are other outbound processes that are sometimes performed, depending on the specific needs of the operation. Some of these include handling of returns, performing value-added-services (like price stickering or gift wrapping), doing assembly work, etc.
Interaction Between Functions
In Part 2 of this post, we will discuss the laying out of distribution centers with respect to inbound and outbound functions. But first, we should step back and think about the planning process in context of the overall supply chain.
The physical activities within the warehouse, such as receiving, put-away, order picking, etc., are all tied to systems and procedures that have some level of interaction. For example, making sure that the product received is the correct product, is properly marked, and all necessary information is gathered and entered into the warehouse system will affect downstream inventory control and order-filling processes.
Warehouse functions also have outside influences and participants. The receiving functions can affect suppliers. Inventory control functions affect and are affected by the company’s material management functions. And lastly, end customers are affected and can affect the order filling activities.
To be truly effective, distribution center layout planning must not only consider basic warehouse functions, but also all the interactions that occur internally and externally. Part 2 of this post discusses the different approaches to layout planning and how to get the best results.
If you’re looking for the best distribution center design and layout to suit your needs, our material handling and supply chain consulting team is happy to help.
Marvin Logan is the Vice President of Consulting and Integration at Bastian Solutions. After graduating from Purdue University, Marvin started his career as an industrial engineer and quickly moved into management. He has had roles as a distribution system manager, operations manager, director of engineering, director of distribution, and vice president of distribution for several leading companies.
Comments
No comments have been posted to this Blog Post
Leave a Reply
Your email address will not be published.
Comment
Thank you for your comment.