Design: Step 4 in the DMADV Process for Supply Chain Improvement
Mike Clemens | 16 July 2014
It is not until the previous three steps are completed that we begin to put “pen to paper” and start the solution design process for your facility. We must also keep in mind that concepts should be in alignment with the problems we are trying to address and must support a viable business case to move the project forward. By leveraging the criteria, characteristics and flows developed in the “Analysis” step we can begin to look at alternative processes and associated technologies that may warrant further evaluation.
Related article: DMADV - The 5-Step Process to Improve Your Supply Chain
Our approach to the development of viable system layout options focuses on process flows, use of space, and labor productivity. We also look at information technology and innovative use of material handling technologies (manual or automated) and time to implement.
We start with a base-line option using current methods which meet all of the project design requirements for space and throughput for our facility design planning horizon. This planning horizon may be 5 – 10 years into the future; not too far as to be unrealistic; but far enough to make a project that may involve significant disruptions and investment worthwhile. This effectively establishes a way to compare new approaches and validate performance improvements and anticipated investment returns.
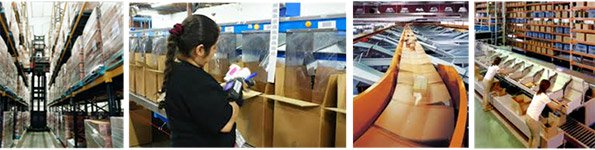
Next, we develop high level alternatives that represent best practice technologies and lean approaches that may result in significant performance gains, and may involve a range of investment, risk, and achievement benefits. These facility design and layout options range from low to high capital investment:
Low Capital
- Improved layout and use of cube
- High level product slotting
- Lower cost improvements (e.g. bulk storage, static picking locations, improved procedures, etc.)
- Typically 10-20% productivity gain
- Fastest implementation timeline
Medium Capital
- Improved layout and use of cube
- High level product slotting
- Strategies to concentrate high volume SKU’s to minimize labor
- Medium cost improvements to mechanize movement (e.g. conveyors, pick-to-light, etc.)
- Typically 20 - 30% productivity gain
- Longer implementation timeline
Higher Capital
- Improved layout and use of cube optimized for material handling solution
- High level product slotting
- Strategies to concentrate high volume SKU’s to minimize labor
- Medium/High cost improvements to automate as much as practical (e.g. unit sortation, carton sortation, voice picking, goods-to-person, etc.)
- Up to 50% total productivity gain
- Longest implementation timeline
For each alternative, we develop a viable operating conceptual design, and equipment layouts. Differentiators are projected invested capital (equipment, site, architecture, and structural elements of the work), space requirements, operating efficiency improvements, flexibility to adapt to the unforeseen, and risk. The entire team then reviews the alternatives, their pros / cons, and develops a consensus around the direction for the recommended solution.
This may be an iterative process as different approaches may be combined to result in a “hybrid” solution that best fits the project requirements, investment goals and risk tolerance. The recommended elements from the alternative evaluation process are finally developed into a recommended conceptual solution. This solution is clearly defined with associated design assumptions, layouts, descriptions, costing, and next step development schedules.
Keep reading: The Final Step in the DMADV Decision Making Process: Validation
Mike Clemens is a principal consulting engineer with the Bastian Solutions consulting group. Mike has more than 30 years of client engagement experience focused on the development, cost justification and delivery of automated material handling systems for manufacturing and warehousing applications.
Comments
No comments have been posted to this Blog Post
Leave a Reply
Your email address will not be published.
Comment
Thank you for your comment.