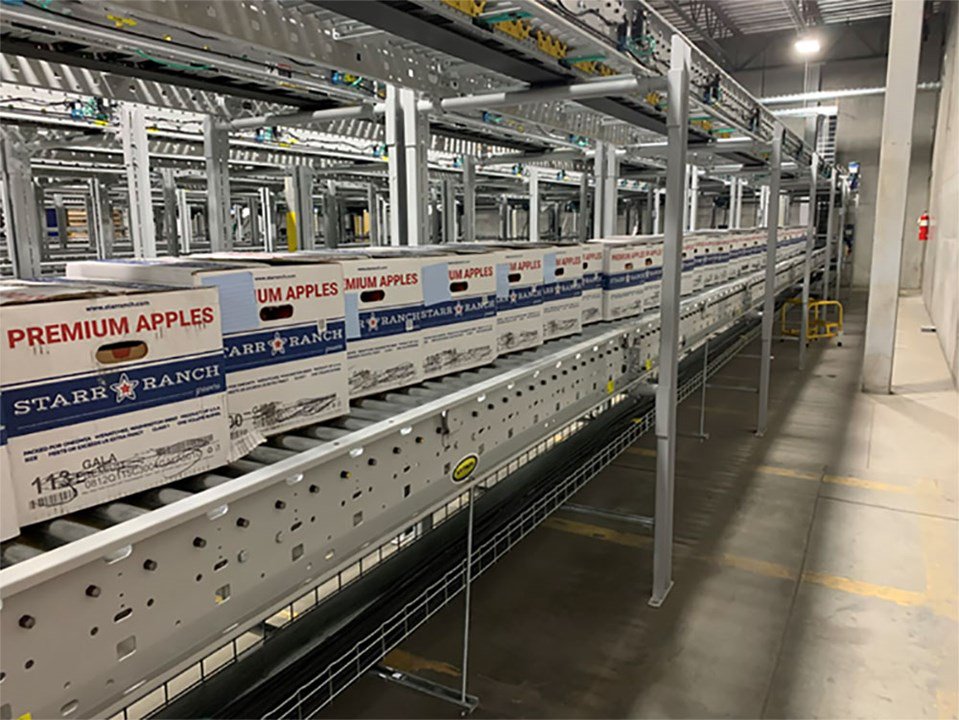
Custom Apple Packers Optimizes Production Flow with Integrated Automation
Trever Hofman | 23 March 2023
Looking to optimize flow of cartons from two production areas and reduce overall labor requirements, Custom Apple Packers turned to RH Brown for automated sortation and palletizing solutions. We were able to design an integrated system that increased throughput to meet the customer’s requirements, while utilizing existing accumulation lanes.
In 2021, RH Brown celebrated its 110th anniversary year and in November 2021, announced a partnership with Bastian Solutions, a Toyota Advanced Logistics company. RH Brown, together in partnership with Bastian Solutions, is a premier provider of material handling solutions in the Pacific Northwest and beyond.
Integrated Automation at Custom Apple Packers
For Custom Apple Packers, the system was designed so cartons of packed apples are received from two production areas and labeled. Cartons in line for sortation and palletizing are inducted to a 3:1 merge where zipper logic directs the cartons into a single line. Cases are then sorted to be palletized or hand stacked.
RH Brown’s WCS LeanLogix software, sends and tracks SKUs to palletizers and communicates the stacking pattern, pallet type and corner board requirements. Once a full pallet count of a SKU is available for palletizing that SKU is added to the queue for release. LeanLogix manages prioritizing the release of the full pallet load and communicates that release to the pallet dispenser based on FIFO (first in, first out) and accumulation availability.
Parameters
Design parameters required that we utilize the existing accumulation system as-is and provide for future expansion of additional accumulation lines.
The project required robust equipment suitable for accumulation and transportation of heavy cases. The conveyor system was designed to transport cases up to 45 pounds each at a rate of 50 cartons per minute for production and sortation conveyance and with a rate of 40-42 cartons per minute palletized.
Tray packs and RPCs (reusable plastic containers) of different sizes, with weights ranging between 38 to 45 pounds are handled by the palletizer with some items diverting to hand stack.
Full pallets with a weight of up to 2,600 pounds are then conveyed to a corner boarder that receives information regarding which height of corners borders to apply and then the pallet proceeds through an automated stretch wrapper and each pallet has a label with barcode and information applied to the lower corner.
In summary, our target was to:
- Optimize the flow of cartons from two production areas into a single line
- Integrate automated palletizer and reduce hand stacking
- Expand accumulation lanes, utilize existing lanes and plan for future growth
- Increase throughput to run production line at 50 cartons per minute
- Manage heavy cases and a wide variety of packaging
Key Technology
To accomplish the laid-out objectives, the following key technology were selected:
- RH Brown’s WCS (warehouse control system) software
- Infeed palletizer
- Robust zero pressure accumulation that reduces product damage, maintenance, bearing wear and noise
- Photo eyes
- High-speed merge
Achieved Speed and Optimization
Once fully integrated, Custom Apple Packers was achieved faster production, automated palletizing, while reducing required manual labor. In summary:
- Increased conveyance and sortation from to 30 to 50 CPM (cartons per minute)
- Achieves 40-42 CPM (cartons per minute), palletized cartons
- Produces 200 customized pallets per day
- Saw an 85 percent reduction in hand/manual stacking
Food Northwest Expo
Join RH Brown at the largest regional food manufacturing trade show in the United States! See you April 4th - 6th!
RH Brown, founded in 1911, is a fourth-generation family-owned business with offices in Seattle, Washington and Portland, Oregon. RH Brown, together in partnership with Bastian Solutions, a Toyota Advanced Logistics company, is a premier provider of material handling solutions in the Pacific Northwest and beyond. When your business needs material handling equipment or advanced material handling solutions, we'd appreciate the opportunity to learn more and see how we can help you meet your goals.
Trever is the Systems Manager at RH Brown, now proudly part of Bastian Solutions. Trever and his integration team serve customers primarily in Washington, Oregon and Idaho. He has over 25 years of experience in mechanical engineering specializing in conveyance and automation.
Comments
No comments have been posted to this Blog Post
Leave a Reply
Your email address will not be published.
Comment
Thank you for your comment.