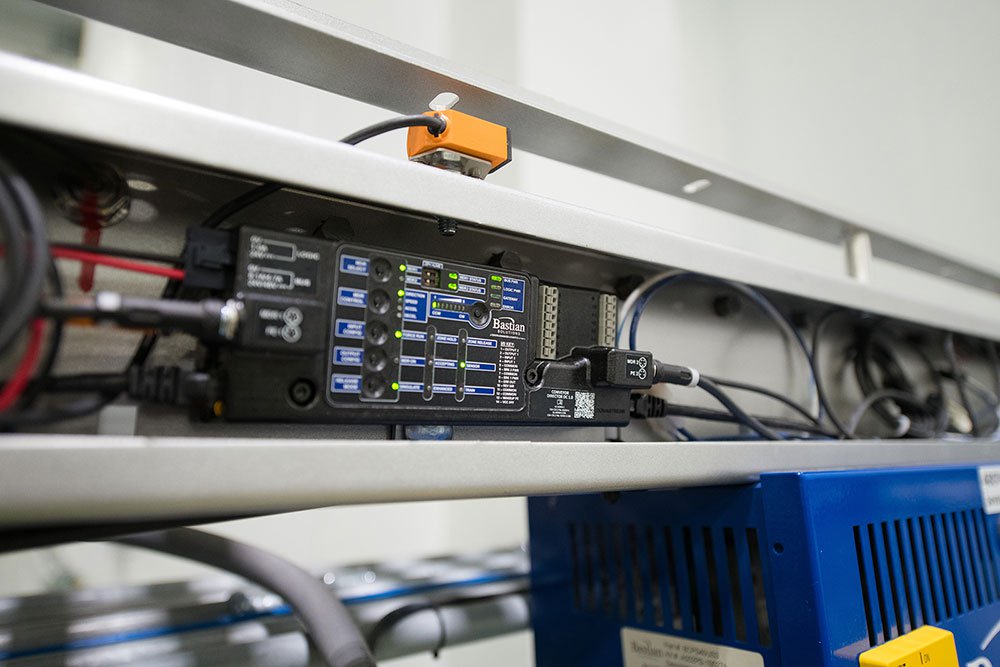
Conveyor Control Reimagined
Sam Osterhout | 7 August 2024
In modern material handling warehouses, efficient product transport through conveyor systems plays a pivotal role. While conveyor systems are pretty straightforward, there are various elements that help to achieve that efficiency.
A key facet of any conveyor solution is the control card, which manages the flow of goods through conveyor zones. These cards provide users complete control over product singulation and release, ensuring products are moved precisely when and where they are needed to optimize the entire automated material handling system.
Improving Human Interaction with Conveyor Cards
Goods-to-person workstations and human machine interfaces (HMIs) are some of the many ways users interact with equipment in a modern-day warehouse. However, the end user is not the only audience that warrants consideration when designing a new product or material handling system. For most conventional systems, the integrator provides a commissioning team as needed to install, configure, integrate and get the system up and running. A maintenance team-whether provided by the integrator or employed by the end user-is needed to keep the system in good working order.
Typical high-performance conveyor control cards require a PC for individual card configuration. They may also require special tools or hardware for addressing discrete wire landings. On the other hand, more cost-effective cards are often de-featured, requiring elevated commissioning time. Now consider large conveyor systems that have thousands of control cards, without a simple, intuitive way to understand and adjust how each card is configured.
The Future of Conveyor Control is Now
Bastian Solutions’ Conveyor Director cards (AC and DC versions) are the answer to the material handling industry’s need for a capable and cost-effective conveyor control card. Offering a button and LED-based, intuitively labeled, UL-compliant card with a Windows-based UI brings a keen focus on human-centered design to conveyor control.
Essential Considerations for Quality-Of-Life in Commissioning
Conveyor control cards of all kinds are handled and reconfigured most often during the commissioning process, especially when in the vicinity of transfers, merges and sorters. While working through the implementation of desired system control logic, flexibility and repeatability are equally critical to the commissioning process. Below are some key features of the Conveyor Director that support easier, faster commissioning.
- Two variants – Conveyor Director comes in two variants – CDDC which drives DC motor-based ZPA conveyor and CDAC which actuates solenoids which control AC motor-driven ZPA conveyor. When connected over the communication ports, these two variants recognize each other and can communicate with each other seamlessly out of the box.
- Manual configuration – The unique button and LED interface of each Conveyor Director card is intuitively labeled and provides zone-level adjustment of all industry-standard features:
- Release mode – Singulation, Enhanced Singulation or Train Mode
- Configurable inputs – Force Run, Zone Hold and Zone Release
- Configurable outputs – Motor Status, Zone Status and Sensor Status
- Zone Control (DC Variant Only):
- Speed/Acceleration/Deceleration – Set in linearly scaled intervals of 1 – 8
- Zone Control (AC Variant Only):
- On Delay/Off Delay – Set in linearly scaled intervals of 1 – 8
More advanced settings or operations such as dynamic zone allocation and factory restore can be set with multi-button combination pushes, all of which are detailed in the product manuals.
- Multi-card flashing – Reconfiguring a single setting on a string of connected cards (e.g., changing a section of conveyor from singulation to train mode) is a frequent activity in the commissioning process. With a simple button combination on Bastian’s Conveyor Director card, one can enter multi-card flashing mode, and simultaneously adjust any setting of every connected control card from a single control card.
- Unsolicited error and photoeye state broadcasting – In addition to offering configurability of all settings from the PLC, using a PLC enables both error and photoeye state changes to be broadcast without being queried (i.e., unsolicited) regardless of the selected configurable inputs and outputs.
- Pass-through IO – While making use of 24V wakeup photoeye power for other peripheral sensors is common practice, any signal can be passed directly through the Conveyor Director card’s configurable input ports to the PLC without affecting the card’s behavior.
- On-the-fly motor testing – Conveyor Director cards offer the ability to turn on a zone of conveyor regardless of system configuration, which can be a great diagnostics tool. Two dedicated DIP switches (one for each zone) are provided on each card for just this purpose and can be used at any time (unless the gateway lockout is in place) to force a motor on. This feature is offered on both the DC and AC variants, and the AC variant offers a global motor start feature that is invaluable for belt tracking purposes.
End-User Experiences, Made Easy
More than ever, the end user needs to be empowered to understand their equipment and what it’s doing. Equally as important is ensuring the cards are intuitive and data mineable, so if something goes awry they can get things back online quickly. It’s imperative for the customer to have confidence in the troubleshooting and corrections they are performing. Both efforts are critical to minimizing downtime and maximizing the life of equipment. The following functionalities were included in the Conveyor Director cards to improve user experience.
- PC-based monitoring and control – A Windows-based UI, called Conveyor Director Configurator, was developed to enable the user to better visualize how a series of connected cards are configured without removing the side covers from their conveyor.
- Find and jog – The Configurator can be used to make specific cards blink, so they are easier to physically identify. If one of the zone’s motors or solenoids are suspect, the user can then jog that motor directly from the UI.
- Neighbor restore – When something has gone wrong and a card simply needs to be replaced, getting your system back up and running shouldn’t require a service ticket. If a failed Conveyor Director card had at least one functional card connected to it prior to failure, the functional card will give the replacement card its intended settings during initial bootup.
- Gateway lockout – In critical parts of systems, commissioning teams and end users alike sometimes wish they could reverse a change they made and go back to the settings that were previously on the card. The gateway lockout can be put in place by the commissioning team prior to system go-live or retroactively if a specific set of configurations are deemed critical to throughput and general system performance. When in place, changes made by the end user will automatically clear after a short timer has elapsed, returning the card to its intended settings.
- User Manual QR code –The QR code provided on the front of the card will take the viewer directly to the latest manual online. For example, if a user is unsure of what an error blink code means, or just wants to know more about the card, they can pull out their phone camera, hover over the QR code, and navigate to the resulting provided URL.
- Project file – This feature, available through the Configurator, allows the user to copy the settings of all connected cards and save them for a later date or apply these settings to any new conveyor system matching an existing equipment configuration. This can be beneficial to return existing equipment to any previous configuration and makes optimized, proven system settings repeatable.
Maximize Up-Time
The Bastian Solutions Conveyor Direct DC and AC cards noticeably and clearly revolutionizes users’ experience with their conveyor systems; simplifying monitoring, adjustments and expansions. These industry-leading cards can also improve customers’ operations by cutting down on commissioning and maintenance time, getting your new material handling system up and running faster.
Ready to maximize your up-time? Reach out to one of our system experts to discuss your conveyor and automation needs today.
Sam Osterhout is a Project Manager and works as a part of the program management team for Bastian Solutions’ research and development division located in Boise, ID. He works with a cross functional team to develop, test and implement advanced technology. He has a Master of Science degree in Mechanical Engineering from Colorado School of Mines.
Comments
No comments have been posted to this Blog Post
Leave a Reply
Your email address will not be published.
Comment
Thank you for your comment.