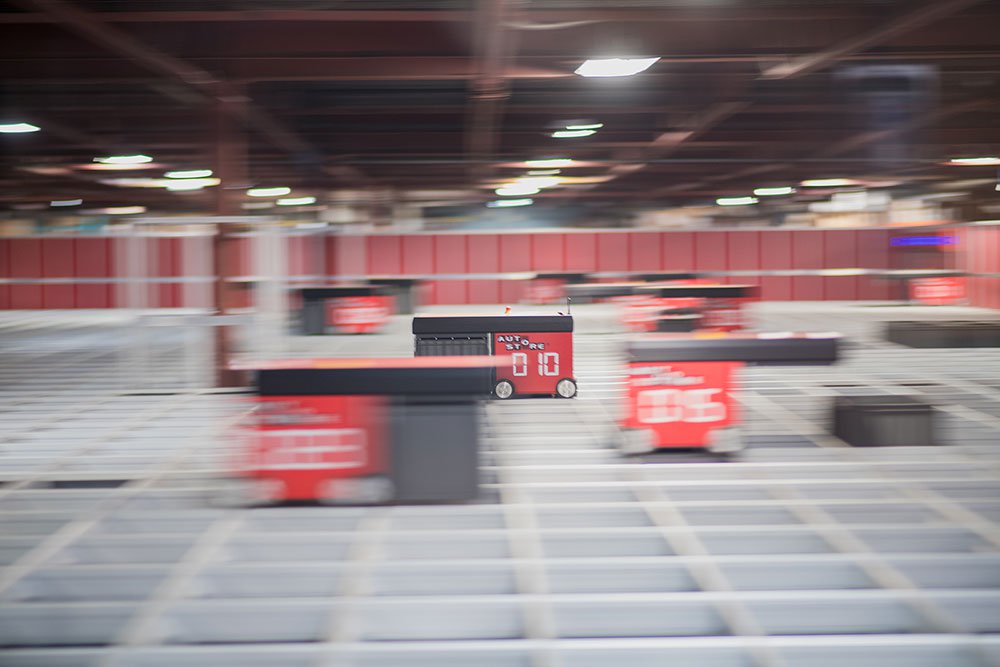
Continuous Improvement with Goods to Person Technology
Claire McDonald | 24 April 2024
When new material handling automation equipment is introduced to a manufacturing or distribution center, it is easy to lose focus on continuous improvement efforts. Often it is assumed that technology and automation have created a process which completely maximizes efficiencies and therefore cannot be improved. Kaizen, meaning continuous improvement, is a core tenant in TPS (Toyota Production System) and empowers individual team members to identify areas for improvement and suggest immediate, yet practical solutions. A facility that focuses on continuous improvement does not stop once a process is automated.
Maximizing Fulfillment Operations
Order fulfillment is a very commonly automated process in modern warehouses with GTP (goods to person) solutions becoming a standard technology implemented to improve operations. However, installing a GTP system does not mean fulfillment tasks are fully optimized. Consider evaluating for inefficiencies by analyzing inventory, conducting operator time studies and analyzing order profiles.
Examine Inventory
One reason inventory data is analyzed prior to implementation of goods to person technologies is to determine the size of the automation. Typical growth is accounted for when deciding between GTP systems, however eventual or rapid outgrowth of a system is possible. The easiest solution would be to build the system to account for the space needed, but this is not always the most cost-effective solution. Looking into inventory quantities, fast and slow moving products, as well as SKU and lot tacking rules can be beneficial in these situations.
For example, your GTP solution has fewer locations open than is recommended and expansion of the system is not possible. A Kaizen approach to this problem would be to consolidate products located in multiple bins/locations into fewer to open up more bins/locations. Note that consolidation should only be done with identical products with identical lots (if tracked).
Analyze Order Profiles
Like inventory data, order profile data is analyzed prior to implementation of goods to person technologies. However, order data can change over time, resulting in diminished impact of your GTP system. Analyzing this data again and taking into account quantities per order, lines per order and peak season fluctuation may illuminate beneficial Kaizen opportunities.
For example, a large number of your orders are for the same products. Rather than completing each order one at a time (otherwise known as discrete ordering), a Kaizen approach to this situation would be batch picking these products and sorting to shipping containers downstream. This new process may be an improvement that could save order fulfillment rates.
Time Studies
Time studies can shed light on inefficiencies by revealing real time issues and delays that operators face. When shadowing and timing an operator, it is easy to notice bottlenecks and small inconveniences that can add up to major time delays. These delays are not always obvious through reports and data. Notice any stops in operation due to quantity of work as this may be an easy resource planning fix. When observing an operator, also pay attention to excessive movement, potential ergonomic issues and non-value added steps.
For example, operators are having to short orders or frequently finding inventory discrepancies that delay their operating speed. A Kaizen approach to this issue would be to perform cycle counts or inventory checks on the system.
A Total System Approach
A Kaizen, or continuous improvement, mindset doesn’t just apply to goods to person solutions. Each task and process within warehouses from material transportation to storage should be evaluated for optimal efficiency. These evaluations ensure throughput rates are met, ROIs are achieved and both equipment and employees are maximized. As a Toyota company, Bastian Solutions engineers are experts in applying both TPS principles and Kaizen philosophies to manufacturing and distribution operations across a variety of industries.
Claire went to the University of Louisville and has a bachelor’s degree in industrial engineering. She is a part of the logistics consultant team and is based out of the software office in Louisville, Kentucky.
Comments
No comments have been posted to this Blog Post
Leave a Reply
Your email address will not be published.
Comment
Thank you for your comment.