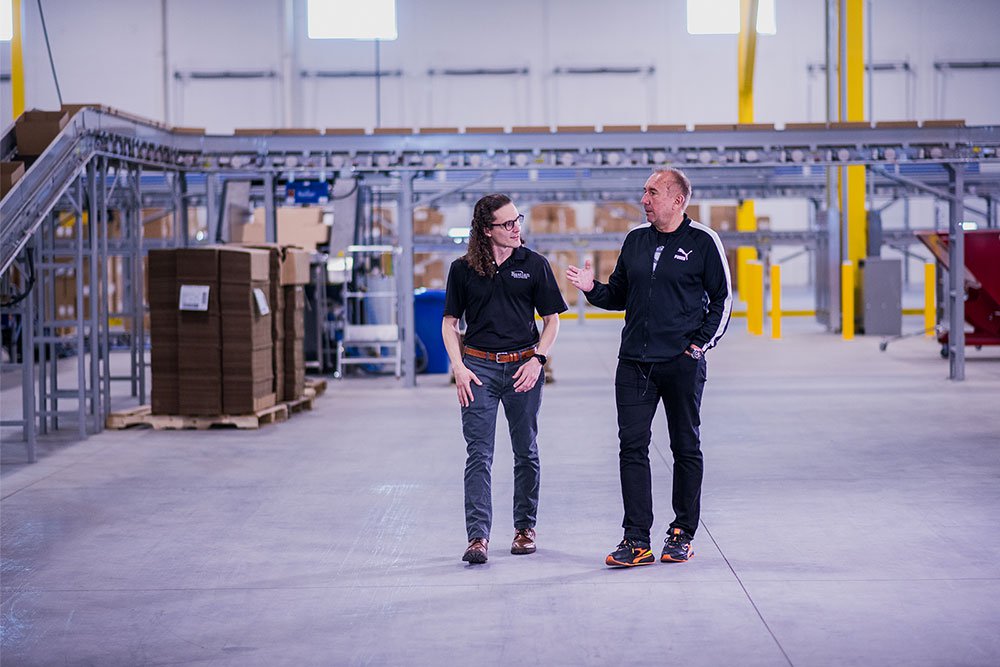
Clear the Fog of Peak Season: 4-Step Process
Ahmed Arif | 1 November 2023
The fog of peak season. Does this sound like a similar experience to all warehouse operations team members? It’s earlier than usual and you know you have a very long day ahead of you.
The building pulses with an electrifying energy but it's a frenetic, anxious feeling that everyone has in the pit of their stomach. The team knows that its “go time” as the customer order volume is going to be 3X the norm. As you walk out of the office and into the warehouse you are met with the sound of conveyor belts humming and the ceaseless beeping noise of forklifts darting all over the building. What is normally an orderly row of neatly stacked goods near pack out, now resembles a maze, as your team scrambles to locate items with urgency. Every corner of the warehouse is in motion, every aisle alive with the chaos of associates picking, workstations loaded with boxes for packout, and trailers are everywhere.
Sound familiar?
The last thing anyone on your team wants to hear is the “conveyor’s down”, “associate absenteeism”, “low inventory”.
This is peak season.
Your company has the potential for record breaking profits. You can’t let operational weakness put you and your company at risk.
Your two main priorities:
1. Take care of your customers.
2. Take care of your employees.
The key to getting your products out the door and your employees well cared for is preparation and planning.
4-Step Process for a Successful Peak Season
Below is a 3-step process to make this peak season your very best for both customers and employees.
Step 1 – Start with Lessons Learned
To start, ask yourself the following questions:
- What happened last year?
- Was there a particular area (receiving, putaway, picking, packout, shipping) that really struggled in your “assembly line”?
- What equipment failed most often?
- What shifts and days were the most difficult to staff?
- Review previous years safety sheets throughout peak season, anything stand out?
- Did you apply any operational changes? Track those areas the closest, did they solve the problem you were trying to solve, did they create new problems?
- Review customer experience surveys, what did you customers say went well and what didn’t?
Never done a “lessons learned”? Start this year.
Empower your staff to document the problems they encounter this year, so you have a strong list to review in January and begin your Kaizen journey. Do you need help getting started? Check out this list inspired by the Toyota Production System (TPS).
Step 2 – Root Cause Analysis
Documenting lessons learned can be draining but putting in the time can help you go beyond. Between lessons learned and solutioning, is where you’ll be able to take the vital step of identifying the root cause. Before you jump into potential technologies and processes, make sure you are addressing the actual problem instead of a symptom of a problem rooted in another area.
This can be done by identifying the root cause of the problem. Root cause analysis helps to ensure your solution address the problem without disrupting anything up or downstream of the issue.
Through Bastian Solutions 70 years of experience in material handling warehouse distribution and supply chain integration, we commonly see these problems and their root cause.
PROBLEM |
ROOT CAUSE |
Difficulty in maintaining accurate inventory counts and tracking product locations. |
Inventory Management |
Errors in order picking, packing, and shipping, leading to customer dissatisfaction and returns. |
Order Accuracy Issues |
Struggles to handle increased order volumes during peak seasons. |
Order Volatility |
Poor layout and space management, leading to underutilized or overcrowded storage areas. |
Inefficient Space Utilization |
Difficulty in finding and retaining skilled labor, especially during peak season. |
Labor Shortages and Turnover |
Lengthy order processing times that result in shipping delays. |
Slow Order Processing |
High rates of product returns due to quality issues. |
Quality Control and Returns |
Workplace accidents and safety hazards. |
Safety Concerns |
Step 3 – Solutioning
The good news is, once you have your list of lessons learned and root cause analysis, you are ready to start evaluating solutions. Building upon the previous table, below are some potential solutions our engineers have seen work for our client’s most commonly reported problem areas.
PROBLEM |
ROOT CAUSE |
Potential Solutions |
Difficulty in maintaining accurate inventory counts and tracking product locations. |
Inventory Management |
Implementing WMS/WES solutions with Radio-Frequency Identification (RFID) technology to track and manage inventory in real time. |
Errors in order picking, packing, and shipping, leading to customer dissatisfaction and returns. |
Order Accuracy Issues |
Adopting order picking technologies like voice-picking systems, pick-to-light systems, and automation to reduce errors and enhance accuracy. |
Struggles to handle increased order volumes during peak seasons. |
Order Volatility |
Using automation technologies, such as autonomous robots, conveyor systems, and goods-to-person, to streamline operations and meet high demand efficiently. |
Poor layout and space management, leading to underutilized or overcrowded storage areas. |
Inefficient Space Utilization |
Redesigning the warehouse layout for better space utilization and implementing shelving/pick modules, goods-to-person (GTP) or storage & retrieval systems (AS/RS) to maximize vertical space. |
Difficulty in finding and retaining skilled labor, especially during peak season. |
Labor Shortages and Turnover |
Implementing automated picking solutions (robotics) to reduce labor dependency and improve operational efficiency, thereby mitigating the impact of labor shortages. |
Lengthy order processing times that result in shipping delays. |
Slow Order Processing |
Streamlining order processing workflows and integrating a Warehouse Control or Execution System (WCS/WES) to automate and optimize order fulfillment. |
High rates of product returns due to quality issues. |
Quality Control and Returns |
Implementing automated quality control processes, including computer vision systems, weight check, putwalls, to mitigate, identify and/or rectify defects before shipping. |
Workplace accidents and safety hazards. |
Safety Concerns |
Employing safety improvements, such as guarding, motion sensors, automated safety gates, and providing comprehensive safety training programs for employees.
|
Step 4 – Schedule
Once you have potential viable solutions identified, it’s time to schedule your plan. The key to success here is time. You must get started early enough to accommodate the time needed to put the solutions developed in Steps 1-3 into place. Here is a practical guide on timelines that can help you schedule.
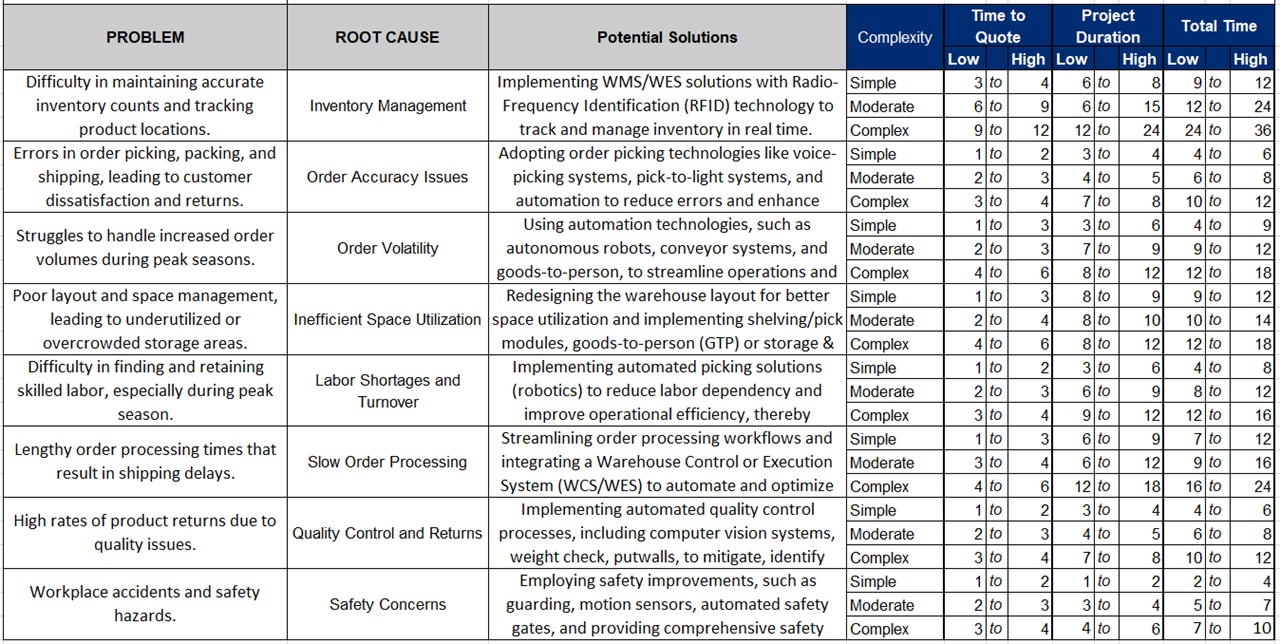
Strategize for Improvement
The key to conquering this tumultuous time is preparation and planning. Begin with a thoughtful review of lessons learned from previous peak seasons, focusing on identifying the areas where operations broke down and the root causes of those issues. Once the pain points are identified, it's time to evaluate solutions. Seek the expertise of a systems integrator to provide recommendations and strategies for improvement so that you can process improve while still producing. We look forward to solutioning with you to make next year’s peak season the most profitable yet.
As the Senior Director of Regional Office Solutions for Bastian Solutions, Ahmed and his teams are responsible for helping our customers achieve their goals in manufacturing, distribution, warehouse management and logistics. A graduate of Purdue University, Ahmed has been with Bastian Solutions for more than sixteen years in a variety of roles.
Comments
No comments have been posted to this Blog Post
Leave a Reply
Your email address will not be published.
Comment
Thank you for your comment.