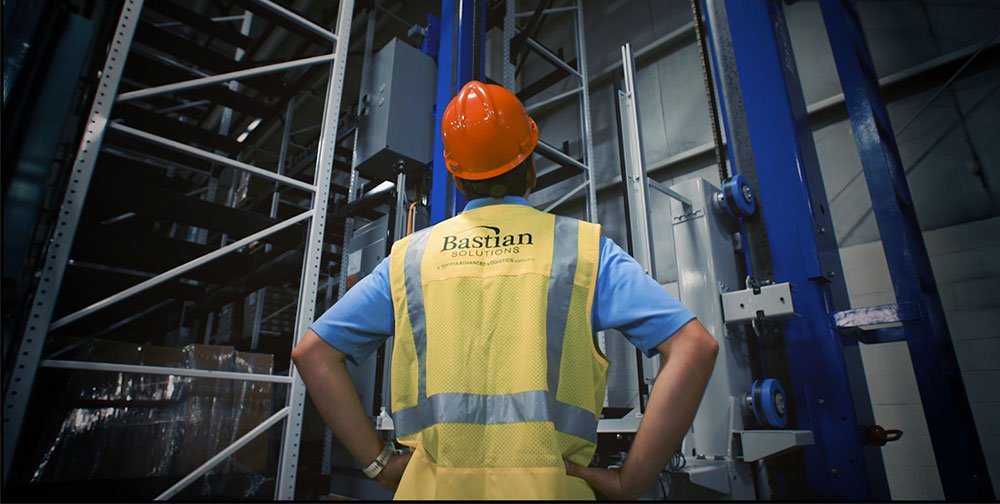
Celebrating Manufacturing Day
Jim Clark | 7 October 2022
My son Austin and I really enjoy steam trains. Often our travel plans revolve around going to a train museum or visiting a location where we can ride in passenger coaches pulled by restored steam trains. Our interest is leading us to plan travel to England at some point and traverse a large portion of the country via several restored steam trains and lines.
My son’s curiosity is in the mechanical nature of a steam train. No computer
chips, no electrical generation, or fueled propulsion such as gasoline or diesel fuel. Simply the use of coal, to heat water, to create steam, to push cylinders. And, all of this attached via mechanically operated components.
I am now talking to him about the manufacturing of these massive pieces of mechanical artwork and how it compares to today’s environment of manufacturing. During the time of the steam engine, “manufacturing” was in its infancy. There were no CNC (Computer Numeric Controlled) machining centers to precisely turn axles, wheels or cylinders that had to work with precision. These tasks were all accomplished via the craftsmanship and hard manual labor from the tradesmen of the time. They used their skills learned over years of experience but also toiled manually without the assistance of today’s modern manufacturing tools.
From the introduction of steam trains and the automobile the world of manufacturing has changed dramatically. The first innovation was the "assembly line", accredited to Ransom Olds in 1901, but quickly modified and taken to a new level by Henry Ford. This led to the introduction of "unified assembly," where multiple departments ferried sub-assembled parts to the main assembly area through the use of small assembly or conveyance lines. Both of these removed a lot of the laborious manual tasks from team members and allowed them to focus solely on the process of assembly.
In 1948 Toyota Motor Corporation released a system of manufacturing principles
called Toyota Production System, often called Lean Manufacturing today. A main focus of Toyota Production System is on the team members inside the manufacturing environment. Always searching to remove waste in human effort, or tasks that do not add value to the product or to the team members. This system of manufacturing flourished over the years and still dominates today in how we think about our team members and the work that they are doing.
Robotics and automation were the next changes in the manufacturing environment. Actually the first robot was introduced in 1926, called the Televox. In 1933 R.J. Wensley was quoted as saying, “In the time to come the only work to be done by men and women will be that which requires faculties of discernment, discretion and judgement. All other work – anything repetitive, routine, standardized – can better be done by machine.”
Wensley was way ahead of his time. Today it is still my vision to achieve Wensley’s goal. Eliminating work that does not engage, excite, or allow a team member to make judgements or decisions. Work that does not allow our team members to grow and learn new skills, are opportunities for us to automate or eliminate.
And today, we stop to celebrate ALL the Team Members that have, and continue
to make this amazing process of manufacturing possible. From the great Steam Engines of the 1800’s to the autonomous vehicles of today. It is not our machines that allow this to happen, it is the Team Members who are continuously striving to make improvements and modernizations that has powered this great revolution of manufacturing. We should continue assisting all of our team members in manufacturing and those supporting the manufacturing operations. Support them by removing barriers to their creativity and learning, thus opening the door to the next generation of manufacturing innovations!
Today we celebrate all who chose to pursue a career in manufacturing!
Jim is Bastian Solutions' VP of Manufacturing Strategy and Operations. Bringing more than 25 years of experience, Jim has an established record in guiding manufacturing processes with sound experience in Lean manufacturing principles and Toyota Production Systems.
Comments
No comments have been posted to this Blog Post
Leave a Reply
Your email address will not be published.
Comment
Thank you for your comment.