Bastian Solutions’ Complete Guide to Conveyor Systems
Bastian Solutions | 16 May 2013
At Bastian Solutions, we are dedicated to providing the best material handling equipment and systems available to meet our clients' specific needs, and one of the most common needs we see is the necessity of handling materials. In cases like this, we often suggest installing a conveyor system. This is one of the most efficient and effective ways to ease the burden of handling large or heavy materials on the production, packaging, or shipping floor.
Conveyor systems are an excellent resource for operations in several unique industries, and as we work with a variety of industrial corporations, we are often asked for more information about the different types of conveyors available, the benefits a conveyor system provides, and how it affects productivity in the workplace. To answer all these questions and more, we are happy to provide our complete guide to conveyor systems.
Conveyor System Operations
A conveyor system can be a very basic or extensive material handling tool that relocates a variety of materials from one location within a warehouse to another. In operational processes featuring over-sized, heavy, or a multitude of products in quick secession, conveyor systems can be a very helpful tool to improve productivity and employee protection. Several companies throughout the globe consider and install conveyor equipment to improve material handling and improve working conditions for employees. The search for workplace safety and increased production has been a key factor in machinery development for centuries, beginning as early as the Old Kingdom (2686–2181 BC) in Egypt.
Ancient Use of Early Conveyors
Many scientists and historical experts suggest that primitive conveyor systems played a large part in the creation of ancient civilization marvels such as the Egyptian pyramids and Stonehenge. Many experts believe that these wonders of the ancient world were created with the help of wooden logs working as rollers to move heavy pyramid blocks or relocate the large Stonehenge stones across several miles of rough terrain and trying landscapes. These wooden rollers worked similar to our modern day conveyor systems, except that man power moved the heavy stones across the logs. It is thought that it took hundreds to thousands of slaves or dedicated druids to relocate the materials that created these two wonders that still stand today.
Shaping the Conveyors of Today
Following the ancient wooden rollers of Europe and Egypt, further progressive civilizations of the past worked to create improved conveyors with the use of wood and a belt that consisted of leather or canvas. These belts were powered by a geared system that worked by the turn of a handle and later through the use of a water mill. It is these renaissance period designs that were the forefather material handling systems that shaped the conveyors we have today. However, it wasn’t until the end of the 18th century that history began to see machinery that truly resembled the conveyors systems operated by electricity that we have in our workplaces currently.
The Forefathers of Modern Conveyor Systems
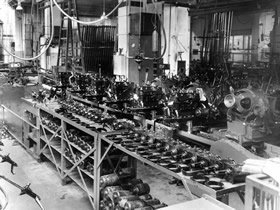
The first modern conveyor systems were invented in 1891 by a man named Thomas Robins, who is considered the forefather of modern conveyor systems and material handling development. Robbins created his first conveyor system to move heavy materials for iron mines, and this was the first time that steel idler rollers and rubber belts were used for rock relocation. By 1896, Robins had patented the three-roll idler and formed his company, the Robins Conveyor Belt Company.
In 1905, an Irish mining engineer by the name of Richard Sutcliffe developed the first underground conveyor belt system for the coal mines, which in turn increased productivity within the mines while improving conditions for coal mine workers. By 1913, conveyor systems were fairly common within the mining industries but Henry Ford rounded out the second industrial revolution when he introduced the first ever conveyor belt assembly line in his car production factory. This handling and location system worked to assemble Model T cars in a quick and efficient way, resulting in this type of conveyor system being implemented into nearly all of the production and manufacturing factories at the time.
The Last Hundred Years
Over the last hundred years, conveyor systems have seen nothing but constant improvement, leading us to the technologically advanced systems we have today. Below are a few of the most notable years for conveyor improvement that have led us to the conveyor systems currently available to assist industries across the globe.
1920s - Conveyor systems began to be manufactured to relocate items over long distances. The keynote conveyor of this time was an 8 kilometer long conveyor belt that ran underground, moving coal. This particular conveyor’s equipment was made of natural materials such as cotton and rubber and set the standard for conveyor materials for the next 20 plus years.
1939-1945 - With the beginning of World War II, the natural materials that were conventionally used to create quality conveyors were sparse. However, ingenuity prevailed and the synthetic material conveyor belts were invented. This would change the face of conveyors forever and open up conveyor belt use to several different industries.
1957 - This year saw the invention and patent of a Turnover Conveyor Belt System that utilized a half turn in the belt system to ensure all areas of the conveyor belt wore down evenly, resulting in the prolonged durability of the belt.
1970 - OSHA requires that conveyor systems work quieter in the workplace to improve employee safety, and companies begin implementing newly-designed, quiet rollers and precision bearings to limit wear and noise.
1972 - By 1972, conveyor systems had come a long way, and the French REI Society celebrated by creating the longest straight conveyor system in the world at the time. The “New Caledonia” was conceptualized by Hyacynthe Marcel Bocchetti and ran the length of 13.8 km or just over 8.5 miles.
1972-1999 - Through the next few decades, several improvements to conveyor technologies were developed, creating internally-powered rollers and electric pulleys as well as lowering regular maintenance costs and needs.
1999-Present - The constant development of new technologies and conveyor configurations keeps conveyor equipment and systems consistent and up-to-date, resulting in cutting edge designs created to meet the exact needs of several unique industries. Computers can now provide control over applications and have increased the automation process to help organizations become more efficient in materials handling in the workplace.
Conveyor Equipment in the Workplace
As history shows us, conveyer equipment has been used in the workplace for centuries. As the years have progressed, the benefits of using conveyors has increased and broadened to meet the needs of several unique industries. With the implementation of computers, a variety of conveyors systems, and ever-improving technologies, we expect to see even more industries convert to the use of conveyor management for their material handling needs. Just a few of the numerous advantages for these organizations include:
- Durability and stability in handling/transporting important materials of all weights, shapes, and sizes
- Improved prevention of workplace and equipment accidents
- Saved expense and strenuous employee labor by using a conveyor to relocate materials across a warehouse or up/down multiple levels
- Easy installation and positive ROI
- Increased workplace safety for employees and reduced need for other potentially dangerous machinery
- A vast array of conveyor types meet almost any industry’s materials handling need
Industries that Use Conveyors for Better Productivity
As you can see by our brief list above, there are several key reasons why industries would consider a change or an upgrade to modern conveyor equipment and systems. While industries such as car manufacturing have used conveyors for over 100 years, other industrial work genres are just now beginning to understand the value of implementing conveyor equipment to handle materials. In alphabetical order, a few of those industries are:
- Brewery and distillery industries – The relocating and production of ingredient materials, containers, and barrels
- Chemical industry - The moving of heavy containers, pallets of salt, and bags of sand
- Ceramic industry - The transportation of large pallets of clay, boxes of plates/dishware, and ceramic materials
- Food industry - The imputing of ingredients, sorting of finished products, and shipping of food products to stores
- Pharmaceutical industry - Transport of medication materials, pallets of completed product, and bottles to be filled with products
- Printing industries (paper, silk screen, etc…) - The transportation of large boxes, movement of unpackaged materials, relocation of barrels of color, solvent, and inks
As showcased above, it is obvious to see how conveyor use can transition across several different industries. This is primarily possible due to the numerous unique types of conveyor systems that are available today.
A Variety of Conveyors to Choose From
There are several types of conveyor systems available--something for every industry, operation, and product relocation need. Depending on an organization’s specific needs, they may require a belt, bucket, or chain conveyor system. Other industries may request conveyor equipment that works as a cart-on-track conveyor, a magnetic belt conveyor or a conventional roller conveyor. Food manufacturing industries often use a chute conveyor or incline conveyor to place ingredients in large steel mixing tanks, while abrasive industries may use a vibrating conveyor to sort out sand and rocks. There are several other systems available to choose from including flexible gravity roller, live roller and zero pressure roller conveyors.
The Selection Process
With so many options, how does a company select the conveyor system that is right for them? Selecting the right conveyor equipment for a business can be accomplished through extensive research, working with material handling consultants, and implementing quality systems that improve employee safety and business productivity.
The first step to selecting the right conveyor for a company is to determine what classification of conveyor you will need and then ask a consultant for the best type of conveyor within that category. Each conveyor is classified into three main categories--load conveyors, accumulation conveyors, and location conveyor--each serving a different purpose for business management and handling.
Systems categorized as load conveyors, transport materials that are being handled by employees and deal with bulk loads. Accumulation conveyors are defined as conveyor systems and equipment that allow (or do not allow) product materials to accumulate on the conveyor. In most cases, these conveyor systems work with computer programming to prevent backups, delays, or problems on the warehouse level. And finally, location conveyor is traditionally located within the floor or overhead in a warehouse.
Maintaining a Conveyor System
Once the proper conveyor system has been selected and installed, the next issue to tackle is maintenance. A conveyor system is a very important part of an organization’s livelihood. The transporting of heavy or awkward-shaped materials can be nearly impossible without conveyor equipment, so it is vital that it be maintained to work properly for the life of the company.
It is also important to select the right conveyor type and to work with a consultant to ensure it has been installed properly. After that, the consultant should inform businesses about the proper care and maintenance of these conveyor systems. If regular maintenance is maintained, the life of the conveyor should be prolonged for several decades. Regular maintenance practices should include monthly inspections, correct training for employees, the monitoring of all working parts (including oiling, lubing, or replacing protectors), and testing of the emergency stop button.
Conveyor Systems Improving Production
We are dedicated to providing the best material handling equipment and systems available that meet our clients' specific needs. As you can see through our guide above, conveyors have been a part of manufacturing for centuries, and there are several different types of conveyors available for unique business needs. We work to consult and provide our clients with all the benefits a conveyor system provides and showcase how it affects the productivity of the workplace.
References: http://news.nationalgeographic.com/news/2011/12/111222-stonehenge-bluestones-wales-match-glacier-ixer-ancient-science/ http://history-world.org/Industrial Intro.htm http://www.themhedajournal.org/content/3q04/conveyors.php http://en.wikipedia.org/wiki/Conveyor_belt#History http://www.wikimheda.org/wiki/Conveyor http://en.wikipedia.org/wiki/Conveyor_system
Bastian Solutions, a Toyota Advanced Logistics company.
We are a trusted supply chain integration partner committed to providing our clients a competitive advantage by designing and delivering world-class distribution and production solutions.
Our people are the foundation of this commitment. Our collaborative culture promotes integrity, inclusion, and innovation providing opportunities to learn, grow, and make an impact. Since 1952, Bastian Solutions has grown from a small Midwest company into a global corporation with over 20 U.S. offices as well as international offices in Brazil, Canada, India, and Mexico.
Comments
Conveyor Manufacturer says:
8/28/2018 10:08 AM
Hi
First of all i wanna thank you for this great article, i am doing business related with Engineering works, i just came to this article while i am searching some solution for Conveyor Manufacturing, and i really love this article. I am totally agree with your points. I will keep watching this place for more knowledge. Thanks again.
Leave a Reply
Your email address will not be published.
Comment
Thank you for your comment.