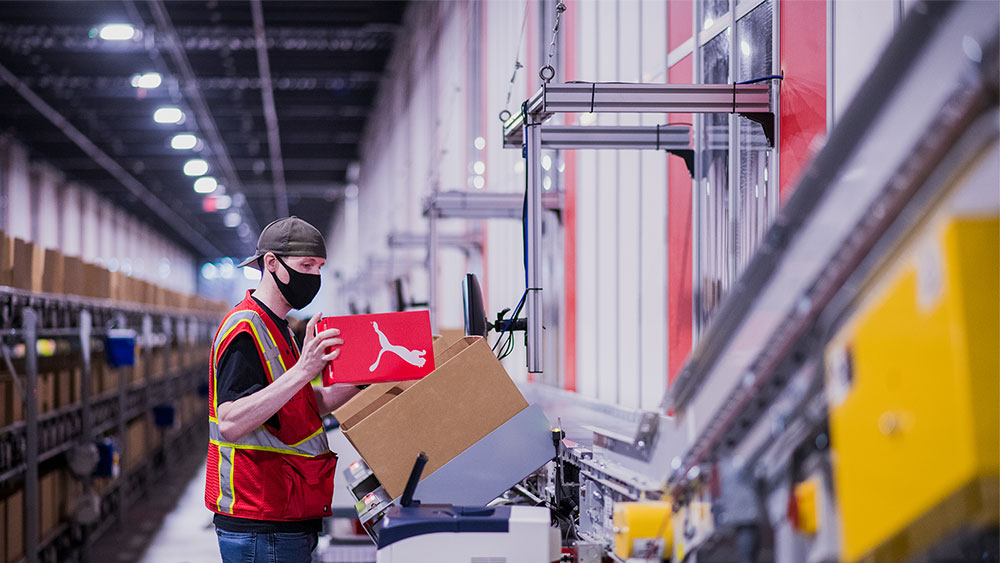
Automated Order Routing & Business Intelligence in Retail Distribution
Mohammad Shaban
AOR Defined
Automated Order Routing (AOR) provides intelligence for the tracking of order fulfillment containers on conveyor belt network to the correct work areas in a distribution center. It communicates with the conveyor controls systems to gather barcode data and retrieves carton information from a database.
AOR makes all routing decisions and gives the result to the control system to be executed. For examples, as orders are released to the floor, AOR is releasing cartons out of a carton erector for picking and is responsible for the automated print and apply application of shipping labels or carton IDs (LPN).
Retail Distribution Essentials
Starting from the top with Interfaces, the routing software should work as a single point of communication to your host system or ERP. It should be capable of handling the transmission of data from any/all equipment on the floor back to the top (ERP/WMS), and back down for order fulfillment.
If you are like me, you may prefer one manufacturer over another - the routing software must be hardware-independent. It must be modular in architecture - your problem is unique. You need a certain set of modules to control the equipment we have chosen to solve for this unique problem. Makes sense to only pay for what you need. Adding a Print and Apply machine to apply shipping labels before packages leaves the building? Your routing software should be designed in a way that accommodate easy, less costly expansions as your business evolves and demand increases. Having all of this functionality is great, right?
Along with the functionality you need to have visibility. Clear visibility to the work going on in all areas of your distribution facility with remote monitoring, built-in diagnostic tools, with both graphics and reports. A User-friendly and intuitive color coded graphical interfaces can't hurt either, and should be custom built to depict the system you and I both designed and have come to love.
Exception alerts to handle small problems before they have an opportunity to grow, Real-time visibility to balance the workload, and Tools set to help monitor and track work flow, system up time and provide alerts to problems. I know I am throwing a lot at you here, so here is a quick break down of the things that can really propel your retail order fulfillment operation.
Smart Conveyor Automated Order Routing
- Directs the flow of totes or cartons around the system, into designated pick zones, and on to packing.
- Interfaces with the conveyor equipment controls through fixed scanners.
- Provides container location information and overall system material flow.
- Redirect order containers to other work areas in the warehouse if an inventory location has no inventory available for the order, or if it predicts a full lane condition.
Priority Routing
- Preferences specific containers into queue on the conveyor system based on their priority level.
- Allows early day freight carrier pickups to get through the system quicker.
Zone Preference
- Allows manual override of default zone routing sequence allowing specific orders a quicker path to pick zones.
- Often used by supervisors to re-direct work into an under-utilized pick zone.
Order Pre-scanning
- A fixed scanner scans all incoming totes into a universal picking zone.
- Allows the carousels to begin pre-positioning without having to individually scan in each tote manually.
Dynamic Lane Assignment
- In Pack and Shipping area, the system recognizes the load in each of the lanes and equally distributes the workload between the lanes.
Sortation Control Utility
- Sort code configuration: allows assignment of sort codes to various sortation lanes. Find lane configured for the sort code to determine the packing and shipping lane destinations for the container. The system also allows multiple lanes to accept the same pack or ship sort code name. Advanced sortation processes may call for more advanced functionality. Allows sortation to a truck route, product type, and then store location in a put to storage medium.
Proactive monitoring event subscriptions and alerts for the following:
Application Monitoring
- Services Started/Ended
- Applications Started/Ended
- Automation Activity
PLC Monitoring
- Faults
- Estops
- Read Rates
- Jams
WCS Functionality & Performance
- Scanner/Sorter Statistics
- No Read Count
- Divert Confirms
- Full Lane Conditions
- Milestones Reached
- Absence of Activity
- Read Rates
System Pacing
- System behind schedule
- Work area behind schedule
Mohammad is a logistics consultant with Bastian Solutions software division, based in Dallas, TX. He has worked for the company since 2011 and has a master’s degree in engineering management and a BS in Industrial Engineering from J.B. Speed School of Engineering (UofL). Mohammad focuses on helping clients design and implement supply chain software solutions and maintains on-going customer relationships.
Comments
No comments have been posted to this Blog Post
Leave a Reply
Your email address will not be published.
Comment
Thank you for your comment.