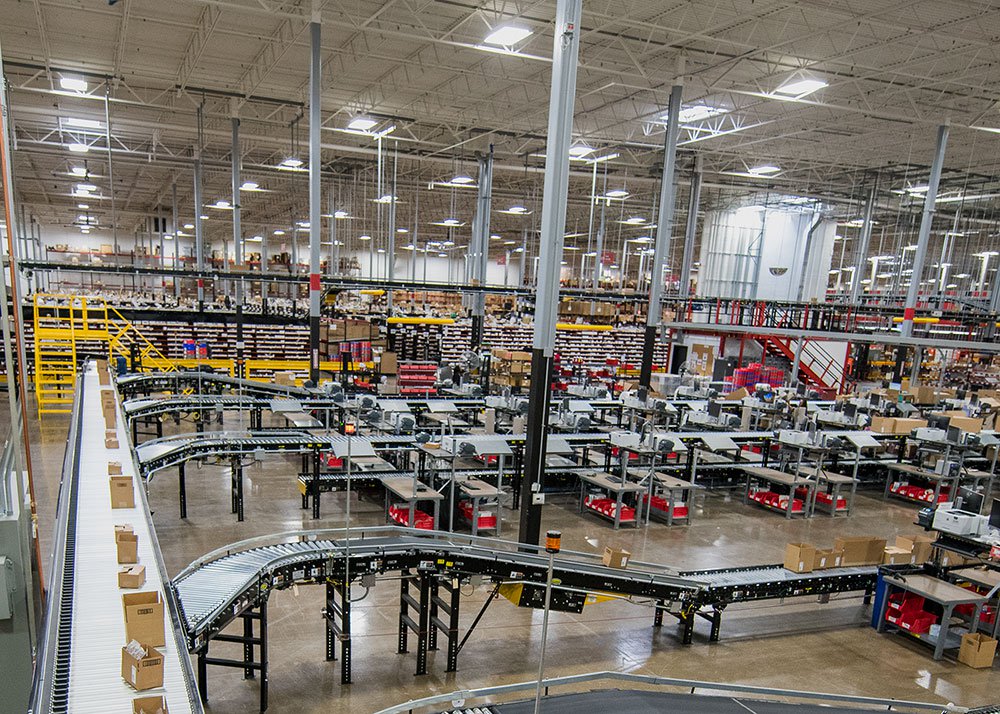
Applying Theory of Constraints Principles: A Case Study
Anshul Singh | 30 October 2024
In today's dynamic business landscape, companies face numerous external challenges such as ever-expanding competitive landscapes, supply chain issues and changing customer demands. To overcome these and improve their internal processes, businesses are increasingly adopting TOC (Theory of Constraints) principles. This blog presents a compelling real-world application of TOC at one of the world's leading home appliance suppliers. This case study not only underscores the effectiveness of TOC but also provides practical insights on how these principles can significantly boost operational efficiency.
TOC Principles Overview
In a previously published blog post, we explored the practical application of the Theory of Constraints principles to enhance throughput. A potent tool for continuous improvement, TOC revolves around identifying and eliminating constraints or bottlenecks within a system. Once a bottleneck is resolved, it often reemerges in another area of the operation, highlighting the iterative nature of TOC as an ongoing process.
TOC utilizes the five focusing steps as guideposts for driving ongoing improvement:
- IDENTIFY the constraint.
- EXPLOIT the system’s constraint or make it work to its maximum.
- SUBORDINATE all other steps in the process to support the constraint.
- ELEVATE the system’s constraint.
- REPEAT the process to identify and address the next constraint.
Please review the previous blog for an in-depth look at each TOC step. Then, let's explore how these principles were applied in another practical scenario.
TOC in Action System Details
A leading American home appliance supplier was struggling to meet fulfillment goals demanded by their customers. Their system included:
- A three-level pick module
- A fast-picking area
- A shipping sorter
All cartons were picked in the pick module and fast-picking area and then inducted onto the centerline conveyor. Cartons picked from the three-level pick module travel outside the pick module and merge into a single conveyor line, which then goes towards the shipping sorter to be sorted down eight divert lanes based on transportation carriers. Each shipping divert lane has five pallet build areas where the operator scans the cartons to palletize.
Orders were released in waves, with a single wave consisting of eight trucks being fulfilled simultaneously, to get the largest volume out of the pick module and high-velocity picking areas.
The (Unmet) Goal
The customer could not fulfill orders on time. The goal was to ship 12,000 cartons daily, but the system could not produce more than 7,000 to 8,000 cartons daily.
Before TOC Implementation
Several operational issues were identified in the system, such as:
1. Replenishment Pick Priorities – The WMS (warehouse management system) software failed to prioritize replenishment picks for the pick module area properly. As a result, replenishments were delayed, leading to short picks within waves. This caused incomplete pallets to remain in the shipping sorter lane, preventing the next wave for that lane from being released. Consequently, shipments from the DC (distribution center) were delayed, particularly affecting subsequent waves.
2. Inventory Inaccuracy –The accuracy of the pick module inventory was compromised due to a few inventory movements that were not recorded within the WMS. This led to picking errors or short picks, resulting in several incomplete pallets at the shipping lane. Operators needed to manually retrieve the missing items from the pick module to complete these pallets, causing delays. Additionally, these incomplete pallets blocked the shipping sorter lane, preventing the release of subsequent fulfillment waves.
3. Slow Replenishment – The pick module replenishment process involves selecting inventory from the reserve, staging it at various zones within the pick module and completing the putaway process. Due to the product slotting strategy, which included mixing some slow-moving SKUs within certain locations, replenishment became a slow and tedious task. This caused delays in moving inventory from the reserve to the forward picking area.
4. Low Productivity – Despite the high pick density in the pick module, resulting from simultaneously picking for eight trucks (wave size), productivity reports indicated that the operators' pick rate (order lines per hour) was well below industry standards. This was primarily due to the mixing of some of the SKUs within a location.
5. Unreliable Picking – Picking accuracy was low due to the slotting strategy of mixing some SKUs within the same location to maximize SKU density within the pick module footprint. This resulted in mispicks, contributing to incomplete pallets in the shipping sorter lane.
6. Limited Software Capabilities – The capabilities of the WMS software were limited. For instance, if a user left their shift without logging out of a task, the task would remain locked, preventing others from picking it up. Additionally, pick waves were released without verifying proper stocking levels.
7. Downtime and Underutilized Time – Unfinished pallets at the shipping sorter caused significant downtime in the shipping area. To maintain workflow, operators in the pick module continued picking the next wave, resulting in cartons accumulating on the conveyor. Once all pallets for the current wave were cleared from the shipping area, these accumulated cartons were released simultaneously, creating a surge toward the shipping sorter. This sudden influx caused lanes to fill rapidly, leading to carton recirculation and further complications, such as misreads, which diverted cartons to the hospital lane. The cartons in the hospital lane then had to be matched with pallets in the shipping area, resulting in additional delays.
To address these issues, several conventional solutions were deployed:
- Incentive Measures: Implemented to boost pick operators' productivity.
- Slotting Improvements: Efforts were made to enhance the slotting of the pick module.
- Software Enhancements: Features were upgraded to facilitate faster picking.
- Operator Training: Provided to improve pick accuracy and productivity.
- Inventory and Picking Accuracy: Focused efforts were made to address short picks and mispicks, which were the primary reasons for shipping lane locks.
While significant improvements were made within each individual area of concern, these isolated solutions only improved system performance in pockets. However, when viewed holistically, the overall system experienced only a marginal increase in throughput, which was insufficient to meet the established shipping goals.
Applying the TOC
Despite employing various strategies, the system throughput could not be maximized. Ultimately, the five steps of the TOC (Theory of Constraints) methodology were applied to identify and resolve the bottleneck:
1. IDENTIFY – The first and crucial step in the TOC methodology. Instead of making random improvements across all areas, the effort was focused on identifying a single bottleneck in the system. One of the core recommendations of the TOC model is to try to maintain a steady flow in the system. This sometimes means prioritizing a steady, lean flow over an intermittent volume flow, which might seem counterintuitive. However, the lack of steady-state flow was identified as the key bottleneck.
2. EXPLOIT – To maximize steady-state flow, breaking the wave into four trucks instead of eight was recommended. Four shipping sort lanes were dedicated to each wave instead of eight. While incomplete pallets were being processed in the four lanes, this setup would release the next pick wave to serve the remaining four lanes. This change ensured a continuous flow of cartons towards the shipping sorter, maintaining a steady flow.
3. SUBORDINATE – This principle is the TOC's most essential and counterintuitive part. Exploiting the system constraint sometimes requires sacrificing productivity in other areas, which can be difficult to gain acceptance for and implement. In this case, reducing the wave size led to lower pick density in the pick module, thus lowering overall pick productivity. Since most operators were in the pick module, this reduction in productivity faced stiff resistance from the client and their team of warehouse automation experts. However, the client was convinced to experiment with this for a day. It is important to note that smaller wave sizes, which reduced pick density, actually increased pick accuracy. There were fewer instances of picking multiple SKUs from a single location (for multi-SKU slot locations), and inventory consumption in the pick module was more evenly spread. This allowed more time for stock replenishments, reducing the number of short picks in the system.
4. ELEVATE – There was no need to elevate this constraint further, as the system met its goal after implementing the changes.
5. REPEAT – After the TOC changes described above were made, the system immediately achieved the target rate, demonstrating the effectiveness of the TOC methodology. As anticipated, the bottleneck shifted to another part of the process.
A Holistic Perspective to Solving Operational Warehouse Challenges
As depicted in the customer example above, there are countless ways to try and address an operational issue in the distribution center. Time, money and human capital certainly aren’t expendable in regular operating hours, but these resources are even more strained during peak season. Having a trusted partner that understands the whole picture and offers targeted, data-driven recommendations will help bolster your company against external factors, ultimately protecting your investment and improving customer satisfaction.
Bastian Solutions experts can apply the TOC principles to your unique process, monitoring system productivity and ensuring continuous improvement efforts are well-planned and executed. Contact an engineer to get started on improving your distribution operations today.
Anshul is a Senior Logistics Consultant with Bastian Solutions' software division. He has a bachelor’s engineering degree from the Indian Institute of Technology, a Master's in engineering from Purdue University and an MBA from the University of Louisville.
Comments
No comments have been posted to this Blog Post
Leave a Reply
Your email address will not be published.
Comment
Thank you for your comment.