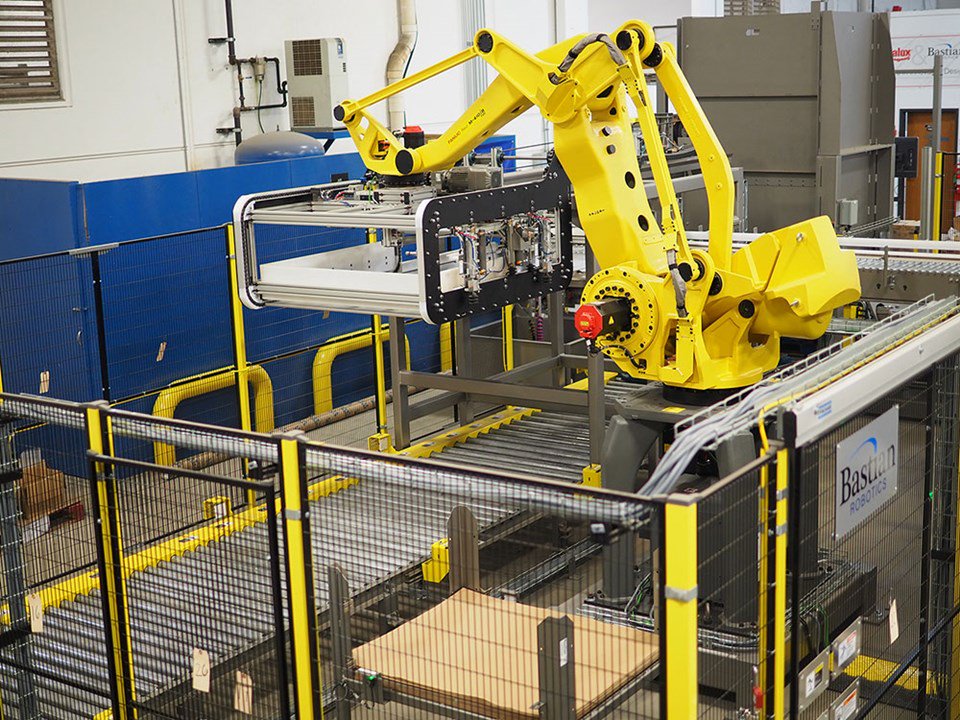
AI-Based Robotic Depalletizing vs. Robotic Layer Depalletizing
Mitch Stevens | 20 November 2024
Manually unloading pallets is a time-intensive, repetitive process that can lead to physical strains for operators and job dissatisfaction. Moreso, unintentional human errors can result in miscounts, misplacement and bottlenecks. The process of removing product from a pallet can be automated through the use of industrial robotics, in a process is called robotic depalletizing.
In recent years, the advancement of machine vision, specifically AI-based vision (artificial intelligence), has allowed robotic systems to identify products on a pallet and relay their coordinates in 3D space back to a robot. From there, the robot autonomously picks the product from the pallet and places it onto a conveyor. This technology is continuing to evolve and advance at a rapid pace.
While depalletizing with AI-based vision is now possible, there are also other more traditional robotic depalletizing solutions such as robotic layer depalletizing with a product descrambler conveyor. This type of system includes more basic machine vision – a larger robot with a full-layer EoAT (end of arm tool) and a descrambler conveyor. If you’re looking to automate this inbound process, it’s important to evaluate both types of robotic depalletizing processes and identify which type may be best for your application.
Adding Intelligence to Robotic Depalletization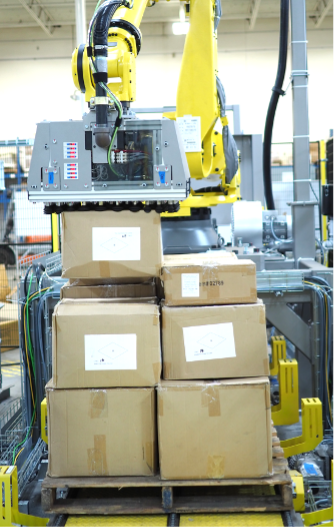
AI-based robotic depalletizing uses an advanced 3D vision system to quickly identify and accurately locate products on the pallet load, then relay the product location to the robot. The robot then moves to the product’s location on the pallet, completes the pick with the robot’s EoAT and places the product to a standard conveyor that transports the product to downstream processes.
The AI vision system uses a library of images and complex algorithms to identify and locate the products on the pallet. As the system is used, the library of images continues to grow and the algorithms allow the system to learn, becoming better at locating future products. This type of vision technology is especially powerful in facilities where there is a high SKU mix. The AI vision can differentiate between individual similar-looking products, allowing it to pick a single box among products that all appear the same. It can also identify different product types on a single pallet load, allowing the robot to depalletize a pallet constructed of multiple SKUs.
While AI vision is a powerful tool and enables robotic depalletizing to be possible for some applications, there are some drawbacks with the current technology. At this time, AI is an emerging technology that is continuing to be developed, which could lead to quick obsolescence. Additionally, these systems generally require an outbound internet connection to allow for data transfer and the continued vision learning. With many institutions, an outbound internet connection can be an issue for network security. On a financial front, there is typically an annual subscription cost for the AI vision service, which could erode ROI. Also, system throughput is typically limited to one or two products per robot cycle, which can mean that this solution is slower than a manual depalletizing process.
Leveling Up with Layer Robotic Depalletization
Robotic layer depalletizing is another method used to remove product from a pallet. This type of system uses a larger robot with a large EoAT that can handle up to a full layer of product. A conventional sensor or vision system is used to locate the product on the top layer on the pallet load. The top layer can be comprised of a single or multiple products and can be either single-SKU or mixed-SKU products. The robot moves the EoAT to elevation of the top-most product(s) and complete the pick. The robot then places them to a conveyor system to “descramble” and singulate the products, then convey them to the downstream process.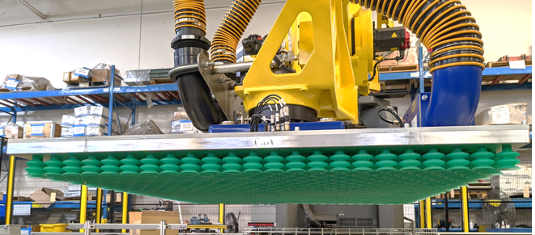
This layer depalletizing system does not require an outbound internet connection due to its use of conventional sensing equipment, which allows for easier implementation at the installation site. Also, throughput can be significantly higher (up to 4x) than AI-based depalletizing systems because the robot is handling full layers of product each robot cycle. However, layer depalletizing systems are generally larger in footprint and, therefore, take up more space within the facility. Also, the initial investment for a layer depalletizing system is typically greater than an AI-based system; but, this may be offset by the savings obtained by the system’s higher throughput.
Tailor-Made Solutions that Improve Employee Safety and Throughput
Both AI-based robotic depalletizing and robotic layer depalletizing have their benefits to certain applications and drawbacks to others. AI-based depalletizing systems utilize an advanced vision system to locate product on a pallet, allowing a robot to pick the product. While the AI-based system footprint and initial investment are smaller (in comparison to layer depalletizing), throughput is lower and the implementation can be complex due to IT-related requirements. Layer depalletizing systems provide more throughput without the IT complexity, but at a higher cost and larger system footprint.
The robotics team at Bastian Solutions can work with you to understand which depalletizing system is best for your process, employees and facility. Our engineers design, test, manufacture and integrate each system, ensuring quality and customer satisfaction through each step. Reach out to one of our experts today!
Mitch is a field application engineer for Bastian Solutions' robotics division. He has Bachelor of Science degree in mechanical engineering from the University of Illinois. As an application engineer, he helps Bastian Solutions’ customers find the right robotic solution for a variety of applications, some of which include palletizing, machine tending, packaging and assembly.
Comments
No comments have been posted to this Blog Post
Leave a Reply
Your email address will not be published.
Comment
Thank you for your comment.