A Food Bank Supply Chain: The Logistics of Feeding the Hungry
Dustin Crandall | 13 November 2018
In the United States, over 41 million people struggle with hunger [1]. This means roughly 1 in 8 people suffer from what is otherwise known as food insecurity. At the same time, it has been estimated that America wastes 72 billion pounds of safe, edible food each year. Landfills and incinerators receive more food than any other solid waste material. Hunger-relief organizations, such as Feeding America, provide an alternative to landfills whereby farmers, manufacturers, and grocers donate discarded food to be stored and distributed to the hungry. Food banks serve as the hubs of these food donation and distribution networks.
From a legal perspective, a food bank is a non-profit organization that collects and distributes food to hunger-relief charities. From a supply chain perspective, a food bank is a warehouse that receives, stores, processes, and ships millions of pounds of food out to the community. These facilities act as food storage and distribution depots for smaller, front-line agencies in much the same way retail distribution centers service storefronts. While many readers are likely familiar with the presence and mission of their local food bank, most do not realize the scope and scale of these operations, particularly large food banks, such as the Houston Food Bank.
Food Bank Logistics
The Houston Food Bank (HFB) distributes 122 million nutritious meals through its network of 1,500 community partners in 18 east Texas counties each year [2]. They distribute 750,000 pounds of food daily, which equates to 18 trailer loads. A distribution network of this size and volume requires modern, reliable equipment and facilities to ensure food is not wasted and meals are not missed.
“Our core is really about logistics. We receive donations of surplus food from all over the country, and we’re distributing product through a network of about 1,500 partners on a daily basis,” Houston Food Bank President Brian Greene said recently in an interview with Houston’s Channel 2.
Accomplishing this feat of logistics begins and ends with HFB’s fleet of over 30 refrigerated food trucks and mobile food pantries. The fleet consists of medium and heavy-duty trucks including single-axle vans, tandem-axle tractors, and long-haul tractors. The medium-duty trucks are used to pick up and deliver throughout the greater Houston area while the heavy-duty tractors extend HFB’s network beyond east Texas.
Within any given month, the food bank fleet covers more than 113,000 miles and makes over 7,600 stops [3] while collecting food and non-perishable items, distributing these items to HFB’s community partners. Partners include food pantries, soup kitchens, shelters, senior centers, schools, and social service providers.
Inside The Facility
Fresh produce, meat, and non-perishable items are distributed from Houston Food Bank’s 308,000 square foot warehouse. The facility holds an estimated 12 million pounds of perishable and non-perishable items at any given time. With the help of many volunteers, the warehouse operation inspects, sorts, packages, and stores the items in preparation for distribution to the community. Standard pallet racking, the prevailing storage media, is utilized in the dry, cold, and freezer storage areas.
The operation deploys a variety of fork lift equipment to move pallets around the facility. Sit-down counterbalanced trucks are primarily used to load and unload trucks and trailers. Pallet jacks, walkies, walkie-riders, and reach trucks are utilized to deliver and pick up loads from the various processing areas. Sorting and packing activities for non-perishable items take place in the ambient warehouse wherever space can be found. Often this takes the form of temporary assembly lines with pallets staged on the floor of racking aisles. Volunteers work together to sort goods and pack boxes that will ultimately be delivered to people in need.
For cold and frozen items, there is a cool pack room equipped with an extensive monorail system. The monorail delivers hanging shelves loaded with boxes and totes to work tables situated in rows spaced evenly across the room. Volunteers inspect, sort, and repack items into boxes destined for the community.
Production at HFB is not limited to pre-packaged items. Keegan Kitchen is their state-of-the art commercial kitchen that produces nutritious hot meals for the food bank’s Kids Café program. The kitchen’s wide array of food processing equipment includes a custom conveyor belt that runs above a steam table, allowing volunteers to scoop food into meal trays as the trays pass. The conveyor belt carries filled trays to a sealing machine capable of sealing 12 trays per minute.
Help From The Corporate Community
The Houston Food Bank’s ability to assemble and maintain such an impressive supply chain infrastructure relies heavily on outside assistance. New Kenworth trucks were purchased in 2018 after Hurricane Harvey, using funds donated by the Justin J. Watt Foundation. Mitsubishi Caterpillar Forklift America Inc. donated an electric-powered walkie pallet truck in 2014. Even the warehouse itself, which has become an iconic symbol of HFB to Houston residents, was acquired in 2010 with help from JPMorgan Chase arranging tax credits.
As impressive as HFB’s operation may be, it is estimated that 1 in 5 people in the 18 counties served still struggle with food insecurity. Given the national statistic, it is clear hunger relief organizations across America are fighting an uphill battle.
As supply chain practitioners, we are uniquely positioned to add value to these non-profit organizations. Whether through knowledge sharing activities, discounted service offerings, equipment donations, or even just volunteering, our assistance can positively impact food banks and the communities they serve.
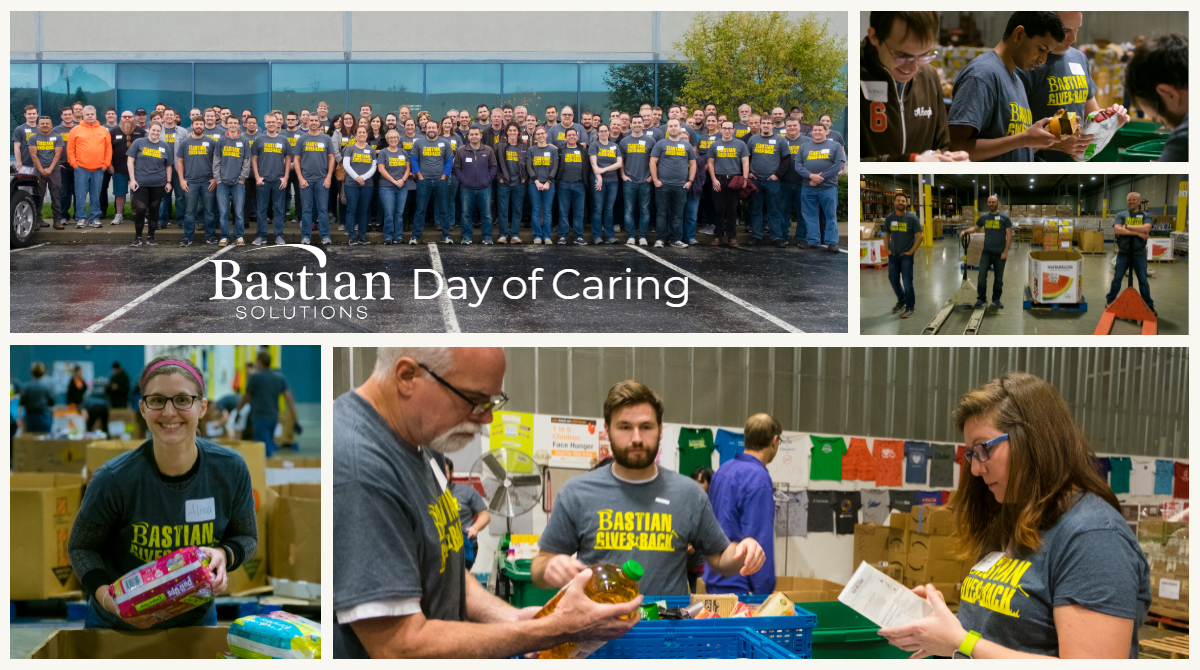
Bastian employees volunteering at Gleaners Food Bank of Indiana
[1] Feeding America website: https://www.feedingamerica.org/hunger-in-america/the-united-states/
[2] Houston Food Bank website: https://www.houstonfoodbank.org/about-us/
[3] Kenworth Trucks website
Dustin Crandall - Dustin is Ops Engineering Team Lead at Bastian Solutions. Dustin has over 10 years of experience in process engineering, conceptual design and project management. Dustin attended the University of Missouri – Columbia where he earned a B.S. in Industrial Engineering. Outside of work, Dustin is an active member of Missions of Mercy, a ministry that provides charity and aid to homeless individuals in Houston, Texas.
Comments
No comments have been posted to this Blog Post
Leave a Reply
Your email address will not be published.
Comment
Thank you for your comment.