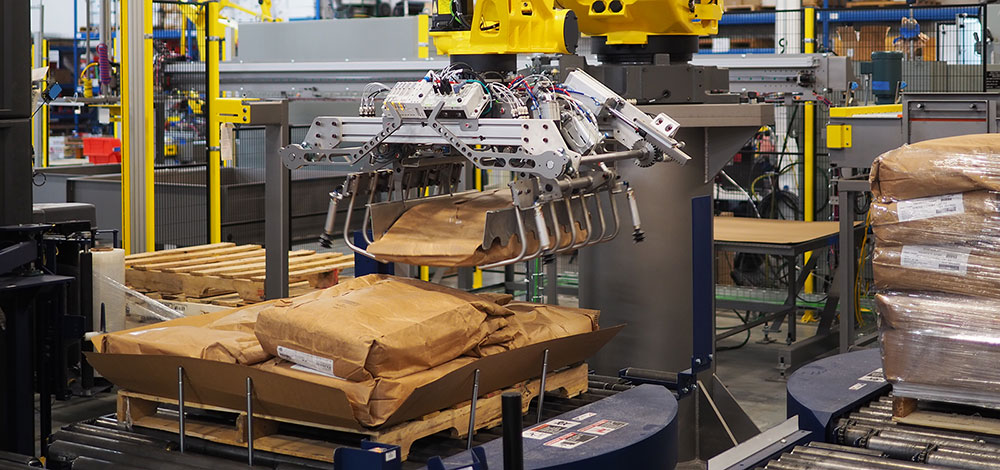
A Few Points to Remember When Palletizing Bags
Mark Zeilinger & Steven Hogg | 16 December 2021
Products that are commonly offered in bags are often filled, sealed and stacked in a highly automated environment. As we all know, pallets and bags, although uniform in appearance, have many variables. The product they contain and the material they’re made from can vary greatly, and like most packaged items, marketers and retailers are constantly devising new shapes and materials to optimize their product offerings.
Putting a bag on a pallet and conveying the pallet is a simple enough concept; however, the variations in product must always be kept in mind.
Here are eight crucial points to remember when using bag palletizing systems:
- Product Positioning
Pallet overhang is one consideration that can vary with product and can affect reliable performance of your bag palletizing system. The system can be designed to trigger a mechanical stop if bags extend beyond the edge of the pallet to correct placement. Pallets with overhangs can results in changed pallet positions which can create issues during transfer or during other operation sequences.

Product overhang on the pallet can also cause issues with a load transferring through a light curtain out of an automated robotic bag palletizing system. If the overhang is non-uniform, the light curtain can be triggered before the muting photoeyes are blocked in sequence on the pallet conveyor. In this scenario, an emergency stop will be triggered because the light curtain is signaling an intrusion through the safety monitoring system.
- Plates and Transfers
Chain conveyors that take away product should have gap plates to ensure pallets don’t fall into those gaps. The conveyor in the picture to the right does not have any steel plates between the chains. If loads being transported are not properly positioned on the conveyor, they can dive between the chains. As you can see in the picture, the pallet is tipping over and no longer properly aligned.
Pallet conveyor 90-degree popup transfers should be designed with the drag chain conveyor frame extending through the CDLR (chain driven live roller) conveyor frame versus a between frame configuration. This also allows for interlacing of chains if a seamless transition is required for load stability. A turntable with transition rollers is another option to ensure a smooth transition between conveyor sections at a pallet junction point.
- Arrange Photo Sensors
Laser-based photoeyes can be utilized in these pallet bag transport applications for more precise sensing. However, photo sensors need to be arranged and configured so that they can properly account for product contrast and shape variations.
- Guard and Bracket Placement
Other aspects that can misalign your pallets or damage product are the guards and brackets on your palletizing conveyor. Paper bags and film, for example, can easily catch on these guards and tear. Any guards or brackets above the conveying surface should be smooth and free of any catch points.
- Stretch Wrapping

Wrapping bagged product can sometimes be difficult. The different contours and gaps can make the film miss the surface of the product. For stretch wrapping unstable loads, there are a few options to consider. You can make the conveyors reversible to reintroduce the pallet to the wrapper when needed.
A spinning turntable is another option. However, if the load cannot be rotated on a 360-degree spinning turntable where the film carriage is static, consider switching to a rotary tower or rotary ring wrapper where the load remains static and the film carriage rotates around the load. A top platen can also be added to most stretch wrapper configurations for increased load stability.
- Pallet Quality
In an automated system, consistent product, pallet, and dunnage quality drives consistency in the pallet build and system performance. Bad pallet quality can diminish your ROI. In many robotic bag palletizing systems, a bottom sheet is utilized on top of the empty pallet in order to provide a more uniform palletizing surface and reduce the inconsistency between pallet types and quality.
- EoAT Configuration
When designing a robotic bag palletizing system, each product type and bag construction should be evaluated to ensure the proper configuration is selected. The interaction of the EoAT (end of arm tool) with the bag pick conveyor is very important and the conveyance system needs to ensure the bag is staged in a repeatable location. 
Typically, the EoAT will be a clam shell style design and the infeed conveyor rollers are spaced so the EoAT fingers can nest beneath the top of roller. Once the bag is in position, the EoAT will close to remove the bag from the conveyor and it will sit on the fingers during transport to the pallet. Side squaring and a pneumatic top platen can be integrated inside the EoAT to ensure the product stays in place during transport and is placed on the load in an accurate location.
- Contingency Planning
Planning for how to handle bags that don’t meet quality criteria can help mitigate problems down the line. There are a couple of options to consider. For example, if a bag fails a quality inspection – barcode scan, checkweigher or metal detector failure – the bag can be diverted off the line prior to the robotic bag palletizing system. Another option is to have the robot continue to pick the bag but place it to a reject pallet inside the cell. Either setup allows for separating the potentially damaged or low-quality product to the side for further review.
Have a question about pallet conveyor design or starting to plan for an automated bag palletizing system? Talk to a Bastian Solutions expert today.
Mark Zeilinger is a Field Application Specialist out of our Grand Rapids, Michigan office. In his role he supports various customer applications and projects in multiple industries. He has over 27 years of experience in technical sales and design.
Steven is the Applications Manager for Robotics at Bastian Solutions. He helps lead the robotics automation solutions for picking, packing, palletizing, machine tending, turnkey options and more. He has a Bachelor of Science in Industrial and Manufacturing Systems Engineering from the University of Missouri-Columbia.
Comments
Tyler Johnson says:
10/30/2019 12:04 PM
That's a good idea to make the conveyor reversible. I would think that could make it a lot easier to fix any mistakes. I'll have to consider getting a skid wrapper that could do that.
Leave a Reply
Your email address will not be published.
Comment
Thank you for your comment.