8 Questions to Consider When Choosing Warehouse Racking
Cody Caissie | 17 May 2019
So, you’re moving into a new distribution center and need product storage. What to do?
Most distribution centers and warehouses are filled with standard selective racking. This can be a blend of different types of racking systems. “Racking” is basically a static type of storage for pallets, boxes, or parts in a warehouse. Standard racking consists of uprights and crossbeams.
While it’s pretty simple and easy to construct, the art of properly choosing and implementing racking can either optimize or inhibit your storage density. Below are some questions to consider with your team before installing 1000 bays of racking at the same height and depth in your new warehouse, since there may be better solutions you haven’t considered.
1. What does your order data look like?
Did you complete a data analysis of your on-hand inventory and past year’s sales data? Is your business a store fulfillment operation, ecommerce, or direct to consumer? Do you pick individual boxes, specific products from a pallet (eaches), or do you pick full pallets and then ship them? These factors are important to determining the best storage solution, as specialized technologies may be worth considering in addition to racking.
One area of extreme growth in North America is automated storage and retrieval systems (ASRS). Although these require a much larger upfront capital investment, they can yield a much quicker ROI given the reduction in manual operators and MHE (material handling equipment) required. That, along with an increased efficiency, allow ASRS (pallet or product style system) to drastically increase the overall production of a distribution center, and may be worth considering for your facility.
2. What type of MHE do you have on site?
Are you prepared to purchase new MHE if your new building has higher ceilings? Keep in mind that the type of racking you select can change your fleet of fork trucks and order pickers. For example, if you plan to pick individual boxes from a pallet at a high level, you will need an order picker rather than a standard fork truck. Deep lane racking storage will also require a fork truck with either an extendable fork or fork extensions.
3. Do you have a standardized pallet size?
The industry standard is 40” by 48”. Are your incoming pallets in good condition? These factors will greatly affect your racking design.
4. What type of product are you storing?
Weight and size can all play into the final design of racking. For example, if you have a new building with a foundation (concrete slab) that is already poured, and it has a pre-determined point load capacity or strength of the concrete, this can drastically limit your storage needs. Although there are ways to increase point load rating by increasing the baseplate size and thickness, this is not always the most economical solution when installing a large amount of pallet racking.
5. Do you require wire mesh decks (WMD)?
This will be required if your pallet size is inconsistent or in poor condition. You will need either a safety bar (runs perpendicular to the cross beam) or a WMD to ensure your pallet is stable with all points of contact on the racking.
6. What type of product are you storing?
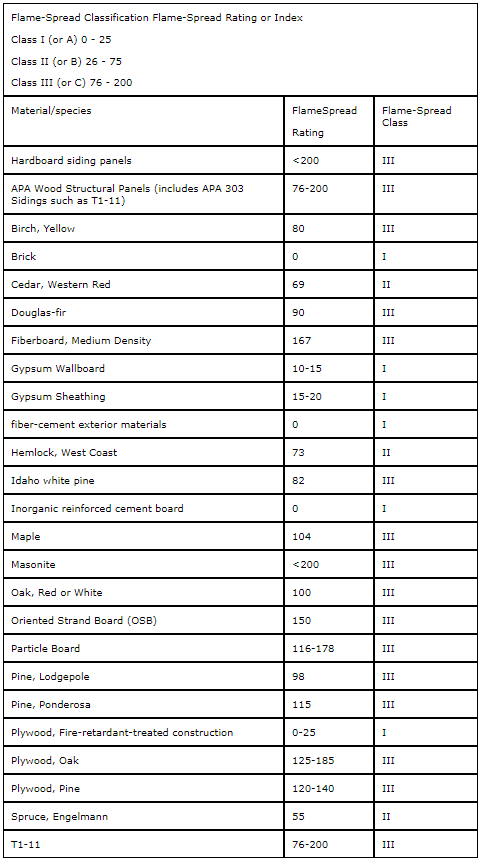
Materials that are highly combustible can cause great concerns when it comes to getting a fire engineer to sign off on your new racking. There are different class ratings of materials (see below) that all have different fire/sprinkler specifications. Consult your local permits and fire code for the most relevant information.
7. Is your facility located in a seismic zone where earthquakes are prevalent?
This is a major point when considering a racking design and should be identified early in the design process.
8. What price and ROI are acceptable?
These are typically the deciding factor. Given the complexity of your new warehouse and storage requirements, there are a few ways to limit the overall investment. Utilizing a team of experts can be one of the most economical routes to assist in defining the best solution for your process to drive overall efficiency and the bottom line. At a very high level there is also a used market for racking that can still be verified and approved by an engineer as structurally sound.
Pallet racking is an important factor to get right in your distribution center or warehouse, as it plays a huge role in productivity and overall efficiency. Although it can be easily implemented by an in-house team, the advantages of a well thought out and defined plan are worth the cost of outside expertise.
Bastian Solutions can not only help you find the best racking options for your operation, but we can help you implement them as well - from data analysis, slotting studies, and then sourcing and installation of the new system. We can help improve all aspects of your distribution center to make sure your business operates at peak efficiency. Contact us to learn more.
Cody Caissie is a Field Application Engineer based out of Toronto, Canada. He is a graduate from McMaster University in Hamilton, Ontario. He excels at creating customer relationships and creating solutions for companies to compete in their markets by providing the best material handling system solutions and technology.
Comments
Jenna Hunter says:
11/11/2019 04:55 PM
I can see how it could be really helpful for a business to make sure that their materials are stored safely on pallets. It was interesting to learn about how racking design and materials should be looked at when choosing new racking and they should look at fire and sprinkler specifications. It would be really nice for them to be able to get some pallets that are the best racking for their warehouse.
Leave a Reply
Your email address will not be published.
Comment
Thank you for your comment.