5 Ways to Supercharge Your Barcode Scanning System with Camera Vision
Bastian Solutions | 30 November 2015
If your barcode scanners are underperforming, it might be time to upgrade to the newest camera vision systems to ensure read rates above 99.9%.
Does your current single line barcode scanner underperform, resulting in excessive no-reads or read conflicts? Today’s case conveyor barcode reading systems need to experience good reads at a rate of 99.9% to 100%. If your system is not reaching this percentage, it’s time to re-evaluate your technology.
Mis-aligned cartons or wrong label orientation will cause single line laser scanners to experience a high number of no-read conditions. If you experience no-reads of 1% or greater, you might overwhelm your conveyor recirculation line, reject line or exception line. On top of that, each no-read condition will require an operator to reconcile that specific case, thus making that person less productive and adding extra overhead to your operations. 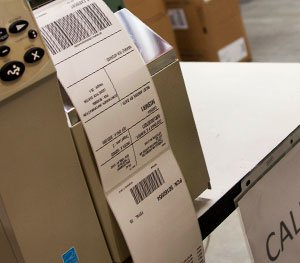
Essentially, single line laser scanners do not always provide a high degree of good read rates in your distribution systems, but there is a solution. You can solve the most challenging barcode scanning applications with advanced, fixed-mounted camera vision systems. Here are 5 ways camera vision can improve your label read rates.
- Today’s omni-directional camera vision scanners will allow you to read case barcode labels that are misaligned and/or out of position by up to 180 degrees. This will help when your existing conveyor system does not properly maintain correct case orientation and label orientation while passing through your single line laser scanner. Accurate picket fence orientations or ladder orientations must be maintained for single laser type scanners to obtain high read rates. Omni-directional cameras will also omit “mis-aligned label” issues.
- In some instances, case labels may have multiple barcodes like UPCs, SKUs, LPNs or shipper labels. Advanced camera software can read the multiple barcodes on a case label and then decipher which label to report to the local warehouse control system. For example, you might only be interested in deciphering the shipper courier label such as a UPS label or FedEx label. This feature will also omit “Read Conflict” type messages.
- Does your application require 2-D Matrix - Direct Part Marking (DPM) codes or Quick Response (QR) codes? Today’s cameras are powerful and fully configurable to read these codes.
- Future of Hazmat labels: You might need to verify that a particular package has a specific Hazmat label applied to the package. Today’s camera technology is set to capture a picture of each package and validate that the correct Hazmat label has been applied. The picture can then be stored on a database for future validation if ever needed.
- Better inventory control can be achieved by using the camera’s ability to read the Stock Keeping Unit (SKU) label. Or, you may also need to read case lot numbers for product traceability.
In summary, advance camera technologies can be used in a wide swath of applications. Benefits from utilizing camera reading include:
- Improved conveyor efficiencies to reduce the number of rejects and jackpot issues, leading to higher throughputs and less manual sorting
- Improved multi-label deciphering on cases to reduce read conflicts
- Part traceability and inspection to read 2-D DPM codes and QR codes
- Addressing future federal mandates of matching shipping packages with the proper Hazmat label requirement
- Aiding in inventory management
If you would like to learn more about using camera vision systems for improving your label read rates, please contact us. Our team can help you identify whether camera vision is right for your operation.
Bastian Solutions, a Toyota Advanced Logistics company.
We are a trusted supply chain integration partner committed to providing our clients a competitive advantage by designing and delivering world-class distribution and production solutions.
Our people are the foundation of this commitment. Our collaborative culture promotes integrity, inclusion, and innovation providing opportunities to learn, grow, and make an impact. Since 1952, Bastian Solutions has grown from a small Midwest company into a global corporation with over 20 U.S. offices as well as international offices in Brazil, Canada, India, and Mexico.
Comments
No comments have been posted to this Blog Post
Leave a Reply
Your email address will not be published.
Comment
Thank you for your comment.