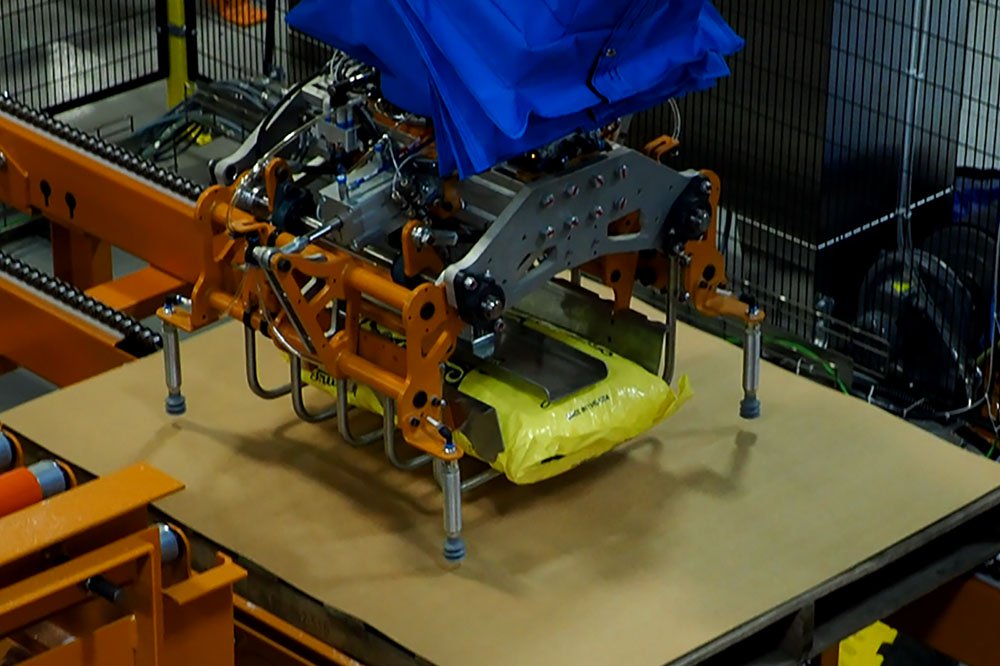
4 Ways Warehouse Industrial Robots Can Maximize Your ROI
Trent Wideman | 30 June 2021
In order to maximize your return on investment (ROI) for a robotic system, it is vital that you optimize the tasks that the robot is assigned. If the rate at which the robot handles product does not completely utilize the robot’s capabilities, you just might be leaving opportunities on the table.
Analyzing the tasks, rates and capabilities can help not only maximize the robotic system but also help reduce the need for ancillary equipment and additional investments, creating a more streamline operation.
Below are the top four most effective and popular ways that you can get the most of your robotic solution.
1. Pallet Handling
Pallet handling is a common task that can be taken on by a robot, replacing the need for a standalone pallet dispenser or pallet stacker.
When palletizing, stacks of empty pallets can be placed within the cell allowing the robot to pick the top pallet from the stack and place it to the load build location. In a depalletizing system, once the load has been completely depleted by the robot, the empty pallet can be picked and placed to a stack of pallets to be removed from the system.
Pallet handling is accomplished by having pneumatically actuated forks that are fixtured on the robotic end of arm tool (EoAT). The forks are placed within the voids of the pallet, allowing for the robot to effectively grip and lift the pallet.
2. Sheet Handling
An additional task that can be handled by the robot is sheet handling. Depending on the pallet pattern and load build requirements, a robot can handle bottom sheet, tier sheet, or top sheet placement with the end of arm tool.
Sheet bins are placed within the robot’s reach envelope. The robot then utilizes vacuum cups on the end of arm tooling to pick and place individual sheets on the load. By integrating this functionality into the robotic EoAT, conventional sheet dispensers can be eliminated from the system.
3. Infeed Conveyor Configurations
Within a palletizing application, the infeed conveyor can be robustly designed to orient cases to form rows. If the necessary pallet patterns require multiple row orientations, this can be achieved by having the robot pick multiple cases and perform multiple drops. However, this method can be time consuming as the robot will have to reposition itself for the drops.
A more time efficient method to meet this requirement, is to utilize a selective turner or a 90-degree transfer with a bump turn mechanism to form the rows.
When paired with the row forming conveyor, these pieces of equipment provide the functionality needed to orient cases in both a wide and narrow side leading fashion.
This robotic solution consolidates what would otherwise be single picks with multiple drops and also frees the robot to perform other tasks within the system.
4. Tool Changers
The industrial robotic arm is a versatile tool that can be leveraged for several different operations. A tool changer is a fixturing mechanism that is installed on the end of the robotic arm that allows the end of arm tool or gripper to be rapidly swapped for another tool.
Tool changers can be configured to be a manual process that requires an operator to switch the tools during a system lockout or as an automatic process that is handled solely by the robot.
Tool changers can significantly diversify the types of products that are handled by the robot. It can also provide opportunity for a single robot to handle multiple processes with different end of arm tools. For example, within a palletizing application a robot could accommodate a diverse range of products utilizing a tool changer – a bottom support end of arm tool, and a vacuum style end of arm tool.
The image to the right is side cut view of a pneumatically actuated coupling device that allows for a robot to change tools on the fly.
Rigorously Designed Robotic Solutions
While each route to get the most out of your robot may not be right for your application, it is likely that one of the listed can be integrated. Each robotic system that is provided by Bastian Solutions is rigorously designed to best fit the specific customer application, so the system is both reliable and cost effective.
Have an application that you think is a fit for robotics? Talk to an engineer today to discuss how we can help you accomplish your goals.
Trent is a field application engineer with the robotics group of Bastian Solutions in St. Louis, MO. He has a Bachelor of Science degree in Industrial & Manufacturing Systems Engineering from the University of Missouri – Columbia. As a field application engineer, his duties include working with clients to determine their material handling needs and developing layouts for robotic systems.
Comments
No comments have been posted to this Blog Post
Leave a Reply
Your email address will not be published.
Comment
Thank you for your comment.