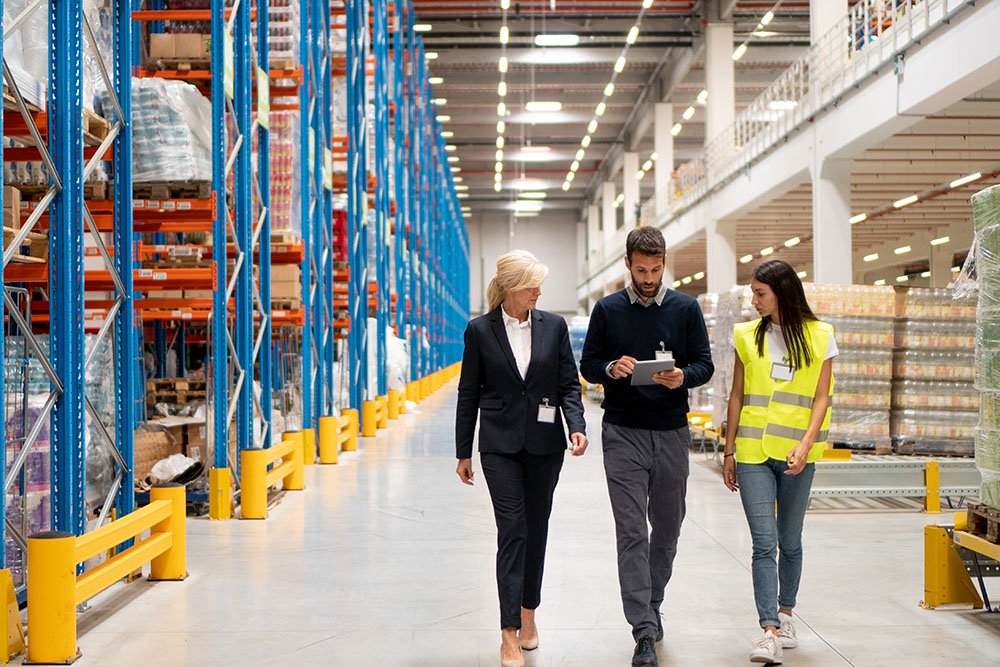
30 Years of Industry Experience: Creating a Strong Foundation for Improved Kaizen Processes
Sean Ito | 27 January 2021
Coronavirus (COVID-19) has penetrated every industry and forced changes throughout. Business processes have required accelerated reviews for the safety of the workforce and to adjust to changes in consumer demand. Supply chain and logistics has been in the spotlight with concerns about how shipments will get from one location to another, replenishment changes due to ecommerce trend acceleration, and demands for same day deliveries. This leads to process and management decisions.
2020 was a year of uncomfortable but necessary process change. Paralleled with new year’s resolutions and facing the “new normal” discussions, business around the world are working to have a more planned outlook with a better understanding of how to react and adjust.
What aspects of your business processes should you protect and what do you change?
While this feels chaotic and new, the philosophy behind Kaizen or Lean manufacturing and logistics management reminds us that it does not require revolutionary thinking or changes to get through these times.
At such times, it is important to always return to the base and reflect.
In my 30 years of experience in manufacturing and supply chain and logistics I have worked in a variety of different roles, different countries, and with different cultures. I have had to constantly go back to the foundational learnings and build from there. It’s no different now. Your foundation is key no matter what business philosophy you may subscribe to.
Letting Go of Assumptions
Freshly graduated from university in electromechanical instrumentation and maintenance technologies, I did not have practice in technical engineering drawings. Yet, when I started my first role, I was assigned to the engine design department. I worked for three years designing diesel engines for commercial vehicles and petrol engines for forklift and heavy-duty equipment generators.
I got the hang of it but not before I broke through my own mental blocks. It was a challenge and I didn’t have the knowledge and experience to “just dive in.” With the help of a coworker, I learned how the engine worked and how to assemble it. I began to understand the impact of the designs I was working on and how that relates to the customer.
Once I was able to look beyond my assigned tasks and forward to the customers concerns, I could better visualize the problem and consider how to solve it. One year later, I felt more confident and was able to do it on my own, thanks to the fact that I was able to take a firm step towards letting go of the assumptions that I brought to the role.
Identifying the Challenge, Reflection and Improvement
At each career transition I’ve had a point where I need to return to the basics. In the same engine design role, at a certain point it was decided that we needed to design an engine and radiator hose.
At the time, more precise computer programs like CAD were a thing of the future. Handwritten blueprints for technical drawings was common practice. As expected, our design elements ran into interference issues with the engine.
The challenge was clear – the design did not work. After reflecting and analyzing the situation, I turned to my coworkers who brought their experience and knowledge to the situation. Together we made the necessary design adjustments and improvements.
Importance of Teamwork
Teamwork goes beyond the people that you are physically working next to. In the engine design example, numerous individuals came together to work on a single drawing. Each of their input was important and brought something new to the solution. This reaffirms the importance of your own input and reminds that you are not working alone.
I keenly realized that it was necessary for me to acquire practice-based knowledge, like my colleagues, and be open to team input in order to make my designs work well in real world applications.
Applying Experience and Creativity to New Challenges
Three years passed after graduation and I now had experience that went beyond my first job role. I had exposure and experience in developing production line systems, managing factory production, leading new projects and so much more.
Customer requests for shorter lead times was common in factory production management. In general, it went like this:
- Create project team with the customer
- Carry out improvement activities
- Try various options and suggestions
- Analyze the impact
- If it didn’t work, try again
Using a strong foundation of an open mindset and teamwork mentality, I was able to find solutions that worked.
Fast-forward to 2003 and I was assigned the task of setting up a new production plant in Poland. Using my production management skill set I selected a site and layout, established systems and rules, and recruited and trained a team of 160 members. This didn’t come easy. The culture and language were different, among other barriers.
We had hired educated, qualified team members and yet we were facing challenges. Why wasn’t it working? Could we supply good quality and affordable products without delay? I was rightfully worried and facing a major hurdle. I felt like I was back at the start of my career.
I was reminded – it’s natural to not be able to do things. Even if you face a challenge and fail, you are not alone. You have the team.
It’s common for people not to show their mistakes or struggles but the harm can be far worse down the line. Creating a culture, in manufacturing especially, where problems are discussed openly and worked on together encourages knowledge sharing and helps the company grow.
In the end the factory project was successful without adjusting the project scope because we focused on human resource development. By increasing the knowledge of the members and giving them a lot of experience, the power of the team increased. Improvement progresses.
Continuous Learning
The factory launch in Poland was followed by a move to Brazil to execute another launch. Likewise, the cultures and languages were different, but the real challenge was the same. We developed a common understanding of clear strategy and goals supported by a culture of having an open mindset. We are all human and mistakes happen. Ignoring challenges is always more problematic than facing them and failing. We can learn from failure, but we can’t learn from inaction.
In my 30 years in the manufacturing and logistics industries I continue to carry this through my personal career and work with others. Kaizen and Lean management principles are great tools but it’s that basic foundational growth and learning mindset that needs to exist for these philosophies to thrive.
Now as part of Bastian Solutions with over 60 years of history with supply and logistics, I will go back to my starting point and embrace the challenges.
Sean is Director of Corporate Quality with Bastian Solutions. He has an engineering degree in electromechanical instrumentation and maintenance technologies. Bringing 30 years of project management and manufacturing and logistics knowledge, Sean has worked with Toyota Manufacturing and Industries Corporation and more recently, Toyota Advanced Logistics North America. Since 2017 after acquisition, he came to the US to start the install of TPS & Toyota Culture for Bastian Solutions’ manufacturing business units. It was a success and now his focus is on other business units to develop our entire solution quality.
Comments
No comments have been posted to this Blog Post
Leave a Reply
Your email address will not be published.
Comment
Thank you for your comment.