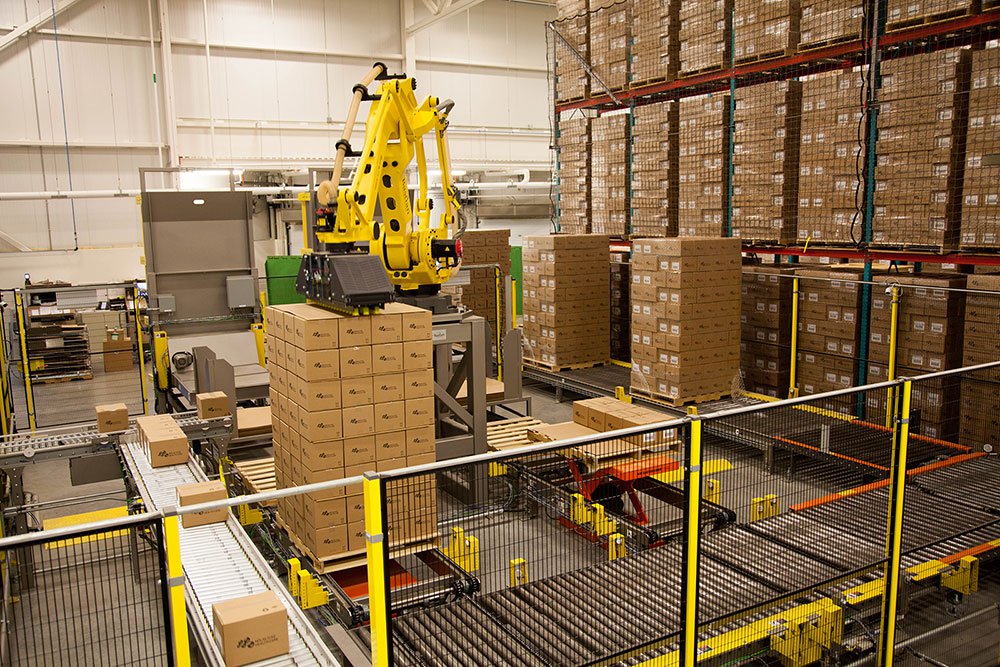
3 Key Technologies to Automate Inbound Pallet Handling
Arlan Ohrt, Michael Yochum and Eric Kinn | 6 November 2024
Building, storing and moving pallets is often what most people think of when they hear the word “warehouse.” And they’re not entirely wrong, pallet handling operations are critical to the effective flow and performance of many manufacturing and distribution facilities. Outbound pallet handling is often the focus of most companies in this space, as these processes appear to be most impactful to the end-customer. However, inbound pallet handling operations can be equally important to the overall production and fulfillment process.
Manual palletizing and movement of inbound product in distribution and manufacturing centers often presents challenges due to labor-intensive processes, ergonomic concerns and safety risks. To address these issues, automation can be implemented to streamline operations and improve efficiency.
Automating the Process: from Dock Door to Storage
The inbound process of pallet handling typically involves receiving products from trailers, palletizing them and storing them. Automated solutions can be integrated at each stage to enhance productivity. Intelligent case conveyance orients cases as needed and sorts to one or more robotic palletizing systems based on the required throughput. Pallet conveyor, shuttles and transfer cars transport palleted loads across facility floors. Automated storage systems efficiently hold, track and protect inventory, even in chilled or cold temperatures.
Let’s take a look at each of these pivotal technologies and how they seamlessly work together to improve inbound pallet handing.
Robotics
Robotic palletizing systems can efficiently place products onto pallets, reducing manual handling and increasing throughput. To fully realize the benefits of these integrated systems, they can be customized to handle various product types and sizes as well as other related manual processes (slipsheet or tier sheet placement). The robot EoAT (end of arm tool) should be carefully selected to safely handle your unique SKUs. Other factors outside product dimensions and weight to consider are operation movement patterns and cycles, environmental conditions and upstream and downstream technologies.
To address current and future palletizing needs, Bastian Solutions StackOrder™, our standard palletizing system, incorporates our proprietary, dynamic pallet pattern software. This software allows customers to visualize, edit and implement various pallet patterns in real time as new products are received. Additional pallet handling equipment and downstream automation technologies such as pallet dispensers, pallet labelers, pallet dimensioners, stretch wrappers and AGVs can also be integrated into the system.
Conveyor
Handling large and heavy items manually tends to be slow and taxing on operations. A proven way to automate this is with pallet conveyor. The product being handled and necessary product control are key factors in pallet conveyor system design.
Properly supporting these products is the first key design note to consider. Chain conveyor generates support parallel to the direction of travel and roller conveyor does the opposite, so understanding the product and layout can dictate conveyor model selection. Next, accessories can be used to control the product in a certain way for surrounding processes. Fixed and actuated stops can help square and stop products consistently, whereas guardrail and fork truck entry guides can help center the product on the conveyor. The design of these components is critical since it is important to find the best way to contact the product and maneuver it throughout the layout while satisfying all process requirements. Finally, the power method of all drives (AC vs. DC) and actuations (pneumatic, electric or hydraulic) can be tailored to the system needs of the end-user.
Effective collaboration between a system designer, pallet conveyor supplier and end-user can yield a very successful integration of pallet conveyance.
ASRS
Manual storage of pallets within rows of static racking is a cumbersome process that is labor intensive and can result in lost or misplaced product. This method can also introduce risks to your operators such as falling pallets or product that is not properly loaded within the designated racking structures. Unit Load ASRS (automated storage and retrieval systems) are designed to handle palletized product quickly and efficiently while also managing the inventory data of the product within storage and most importantly isolating man and machine within the warehouse.
Within the Unit load ASRS space, there are several technologies from which to choose depending on the application. The unit load technologies include ASRS cranes (also referred to as storage and retrieval machines), aisle captive pallet shuttles and non-captive pallet shuttles.
- Unit Load ASRS cranes have been around since the late 1960s and are configurable to any number of pallet shapes and sizes based on the end user requirements. Within the unit load ASRS segment, there are fork-based cranes which leverage telescopic forks to handle the underside of the pallets and deep lane cranes which leverage single-axis shuttles that travel between the ASRS racking to store product within deep-lane racking.
- Aisle captive shuttles are a more recent expansion of the unit load ASRS product that involve a parent/child shuttle setup to move product to and from designated storage lanes. With these being aisle and level captive, this technology leverages lifts to move the product between storage levels as well as to and from the inbound and outbound operations.
- Non-captive pallet shuttles are the newest unit load ASRS technology to enter the market. These unique shuttles work using two sets of interchangeable wheels to allow the shuttle to move in both the X and Z axis on a given storage plane. These shuttles and/or product can then move vertically using lifts as well.
To understand the best Unit Load ASRS technology for your operation, critical information about the footprint available for storage, the storage environment as well as product specifications and throughput are required.
Selecting the Right Automation for Today and Tomorrow’s Challenges
By automating inbound material handling processes, distribution centers can improve operational efficiency, reduce labor costs, enhance safety and increase overall flexibility. To understand the best assortment of technology for your operations, it’s crucial to capture and analyze data about your current process as well as determine your goal end state. A trusted independent systems integrator, like Bastian Solutions, can help you assess the wide range of automation equipment and software applications. Through our decades of experience, innovative computer models and physical testing and commissioning, our engineers can work with you to develop an automation plan for your facility that future-proofs your processes, optimizes your ROI and improves employee satisfaction. Contact one of our systems experts today to learn more!
Arlan is a Project Engineer with the Solution Delivery group of Bastian Solutions in Indianapolis, IN since 2020. He has a Bachelor of Science degree in Mechanical Engineering from Florida State University. As a Project Engineer in the Solution Delivery group, Arlan concepts and implements some of the most complex and large automation systems for customers.
Eric is the ASRS Technical Lead at the Bastian Solutions headquarters in Carmel, Indiana working for the Systems team. He has a Bachelor of Science in Mechanical Engineering from Purdue University. As the ASRS Technical Lead, Eric works with clients to advise on the best automated storage solution for their needs and ensures that the proposed system follows standard design practices allowing for the most cost-effective solution for the clients.
Michael is a Senior Application Engineer with the Robotics group of Bastian Solutions in St. Louis, MO since 2014. He has a Bachelor of Science degree in Industrial & Manufacturing Systems Engineering from the University of Missouri – Columbia. As an application engineer, Michael works with customers to design and integrate automated solutions for their material handling needs in manufacturing, distribution, and logistics.
Comments
No comments have been posted to this Blog Post
Leave a Reply
Your email address will not be published.
Comment
Thank you for your comment.